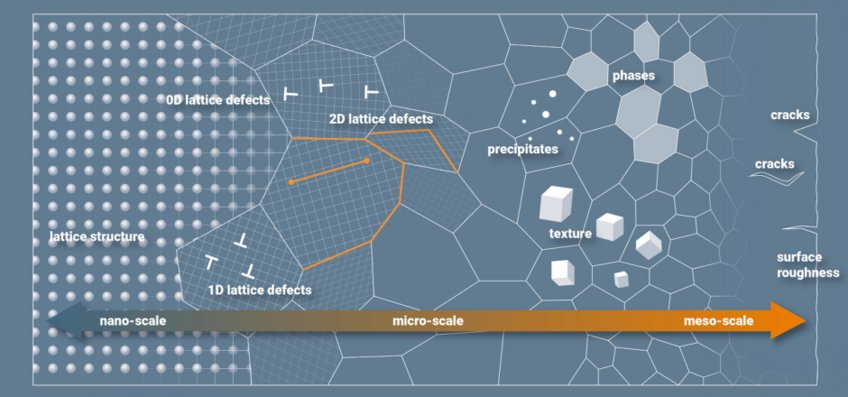
Microstructure Physics and Alloy Design
The department ‘Microstructure Physics and Alloy Design’ investigates the fundamentals of the relations between synthesis, microstructure and properties of often complex nanostructured materials. The focus lies on metallic alloys such as aluminium, titanium, steels, high and medium entropy alloys, superalloys, magnesium, magnetic and thermoelectric alloys. We investigate the microstructures and properties using theory and advanced characterization methods from the single atom level up to the macroscopic scale.
Our latest Research Groups
Mission Statement
We study microstructures and their influence on the properties of materials, mostly metals. Microstructure comprises the structure, size, dimension, patterning and chemistry of all lattice defects including vacancies, dislocations, and interfaces. We study individual defects such as single vacancies (with Field Ion Microscopy and atomistic modeling) and also large statistical defect ensembles such as light years of entangled dislocation lines (for instance by X-ray diffraction and crystal plasticity modeling).
Microstructure affects all materials, from pure single crystals to complex engineering alloys. It can change, by orders of magnitude, a material’s mechanical behaviour (e.g. strength, ductility), electrochemical response (e.g. corrosion, charging behaviour) and functional properties (e.g. magnetic hysteresis, electrical conductivity).
For tailoring microstructures and chemistry we work on alloy design, metallurgical processing, combinatorial synthesis, sustainable production and additive manufacturing.
Our main analysis tools are computational materials science, machine learning as well as multiscale and multi-probe characterization.
With this expertise we have developed a knowledge-based approach in contrast to the traditional try-and-error-approach to the development of new materials, microstructures, processes and property combinations, often by reconciling sometimes antagonistic properties such as mechanical strength, ductility and soft magnetic behaviour.
Impact on Society
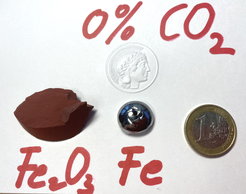
Since the dawn of mankind, complex materials have been the backbone of human society. Today, they are indispensable in the fields of energy, industry, transportation, health, construction, safety and manufacturing. With >2 billion tons produced every year, particularly metals stand for massive economic growth, job safety and wealth increase. Due to the sheer quantities produced and used, they also play a central role in sustainability.
Currently, we enter from the age of linear industry into a circular and digitalized economy. This offers huge opportunities to revolutionize the way how production, transport and energy supply work. These changes affect the daily lives of billions of people. Advanced metallic alloys, their production and downstream use, also at large scales, are key to this transition, as they enable a carbon-free, digitalized and electrified industrial and urban future.
Therefore, we devote all our efforts to understand, invent and enable advanced materials for a sustainable and safe future.
The research activities in the department are the interplay between all the defects that make up an alloy’s microstructure and their local chemistry. For revealing the underlying scientific laws of these interactions we conduct well-designed experiments and run them in concert with predictive simulations. The aim is the physics-based design of materials with superior properties and sustainable processes for the fields of energy, mobility, infrastructures and health.
Material Classes and Fields of Research
Our group works on the fundamentals of the relations between synthesis, microstructure and properties of often complex and nanostructured materials. Focus is on metallic alloys such as aluminium, titanium, steels, high and medium entropy alloys, superalloys, magnesium, magnetic and thermoelectric alloys. We aim to understand the fundamental relationships between specific thermodynamic and kinetic features of materials and the evolution of microstructure and thus their effects on mechanical and functional properties. We therefore select, synthesize, process and probe materials along specific intrinsic property gradients, such as their phase (meta-)stability, solid solution content, stacking fault energy, (athermal) transformation behaviour, magnetic hysteresis or chemical reactivity.
We also study how such materials behave in reactive and harsh environments such as high and cryogenic temperatures, high fields and mechanical loads, as well as under corrosive and hydrogen exposure. Our experiments aim at profound and general insights, based on theoretical concepts. We combine computational materials science, machine learning, synthesis, processing with characterization down to atomic and electronic scales. Many projects are pursued in close cooperation with other departments and extramural partners.
Fields of Special Methodological Expertise
Computational materials science: Our expertise in this field lies in the theory of micromechanics and its non-linear interplay with chemistry and phase transformations using constitutive modelling. We have also started to include the interaction of micromechanics and redox reactions in our simulations, such as needed to describe material decay, corrosion and reduction processes in energy conversion applications, harsh environmental conditions and metallurgical sustainability. Over more than 25 years our research experience and simulation codes have been cast into the software package DAMASK, a free simulation kit for modelling multi-physics crystal plasticity, thermal, phase transformation and damage phenomena from the single crystal up to the component scale.
Multiscale and multi-probe microstructure characterization: In this domain we apply fully correlative atomic-scale and mesoscale probing of structure, defects and chemistry to the exactly same material position, to jointly probe structural, chemical and property features e.g. of chemical decoration and transformation phenomena at internal interfaces, environmental degradation, dislocations or even single vacancies. Therefor we use combinations of atom probe tomography (APT), electron channelling contrast imaging under controlled diffraction conditions (ECCI), 3D electron imaging and backscatter diffraction (EBSD), cross-correlation EBSD, and field ion microscopy (FIM), often coupled with theory and machine learning, for enhanced quantification of the data.
Alloy and process design: In this field we work on making materials that have property profiles with often conflicting features, such as high mechanical strength and good ductility, fracture toughness, thermoelectric performance, hydrogen embrittlement resistance or functional properties. In the research quest of processes, mechanisms and materials for sustainability and a circular economy, the microstructure-centered approach enables us to identify pathways towards enhanced sustainability of metallic materials. This includes areas such as reduced-carbon-dioxide primary production, recycling of metals, scrap-compatible alloy design, contaminant- and hydrogen tolerance of alloys, hydrogen-plasma based reduction, electrolysis for the reduction of oxides and hydrogen-based direct duction of iron ores.
Processes, Mechanisms and Materials for Sustainability and a Circular Economy: The microstructure-centered approach of the department enables us to address our latest research quest, namely, to identify pathways towards enhanced sustainability of metallic materials, in areas which include reduced-carbon-dioxide primary production, recycling of metals, scrap-compatible alloy design, contaminant- and hydrogen tolerance of alloys, hydrogen-plasma based reduction, electrolysis for the reduction of oxides and hydrogen-based direct reduction of iron ores. For this purpose we have designed and modified a number of laboratory-scale reactors in which corresponding experiments can be conducted, under well-controlled reactive boundary conditions and temperature control as well as permanent in-operando monitoring through mass spectrometry. These experiments are conducted in close cooperation with the group of M. Rohwerder in the department for Interface Chemistry and Surface Engineering.
Topics with high activity are currently hydrogen-based direct reduction of iron oxides, hydrogen plasma-based production plus melting of oxides in electric arc furnaces and the design of alloys that can tolerate highest possible scrap and thus impurity fractions.
Department Structure and Research Groups
The department structure and organization reflects our understanding of fundamental yet highly flexible research. Some of the research groups pursue long-term visions of high strategic and methodological relevance for the department’s mission.
Some other groups are non-permanent, and they are usually extramurally funded. Funding agencies are for instance the MPG-FhG collaboration scheme, ERC, DFG, BMBF or VW Stiftung. This helps to rapidly establish new initiatives and to provide opportunities to young science leaders to pursue their own ideas and grow new initiatives.
Another category of groups, interdepartmental & partner groups, is placed between the departments and between MPIE and partner institutions elsewhere. These groups are often also funded by extramural third party funds or by partnership programs of the Max-Planck Society. They establish new research fields which are placed between the individual departments and thus form centers for intense cross-disciplinary research, tapping competences from all departments and from centers outside of the institute.
The long terms research groups, permanent groups, in the department work on Atom Probe Tomography (Baptiste Gault), Mechanism-based Alloy Design (Dirk Ponge), Microscopy and Diffraction (Stefan Zaefferer), MIcrostructure and Interfaces of Battery Materials (Yug Joshi) and Theory and Simulation (Franz Roters), Fig. 1.
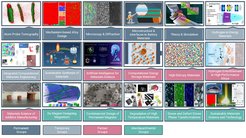