Max Planck Partner Group “Environmental degradation of high temperature materials in service conditions”
S. K. Makineni1, D. Raabe2, B, Gault2
1Department of Materials Engineering, Indian Institute of Science, Bangalore
2Department of Microstructural Physics and Alloy Design, Max-Planck-Institut für Eisenforschung, Düsseldorf
Gas turbine engines power passenger/military aircrafts, ships and power plants. High temperature materials used in the engines experience a severe pressurized gaseous mixture environment during their operation at temperatures up to 1600°C i.e. higher than the melting temperature of the material used for the engine components. A combined usage of cooling systems and thermal barrier coatings, more specifically on blade material, prevents them from melting. However, the gaseous mixture consisting of hot water vapor (steam) containing sodium, sulfur, vanadium and halide groups intensifies/accelerates oxidation, sulfidation and corrosion of the components that causes rapid consumption and degradation of materials, eventually leading to engine’s catastrophic failure. Several aircraft accidents leading to loss of lives happened due to the inability to prevent and/or detect the material degradation at an early stage. The preventive measures can be possible by comprehensive analysis of underlying material degradation mechanisms on exposure to sever/harsh corrosive environment.
Commercial materials that are being used for engine blades and disks are Ni-based superalloys in single- and poly-crystalline form respectively. These alloys are multi-element with dual phase microstructure comprising face-centered-cubic (fcc) γ matrix phase and strengthening L12 ordered γʹ precipitates. During engine operation, the blades and disks go through stress induced deformation and accumulation of strain takes place in the material by formation of a large number density of defects that includes dislocations, stacking faults (SFs), anti-phase boundaries (APBs) and micro-twins that are distinct in both chemistry and structure from the parent material (figure 1).
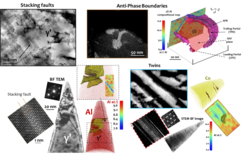
Figure 1: Structure and composition of different types of creep induced defects in γ/γ′ superalloys.
Although several studies were made to assess and identify the degradation mechanisms, but they were carried out mostly on a macro-scale with a qualitative approach. Another important challenge is to mimic the dynamic operation conditions of the turbine engines to obtain similar concurrent exposure of stress, environment and temperature to the components. No experiments were performed for evaluating specifically the effect of material deformation i.e. the role of defects (dislocations, SFs, APBs and micro-twins) on its corrosion behavior, as it takes place dynamically during the operation of the engine.
Hence, the main goal of the group is to explore, understand the atomic-scale degradation behavior of high temperature superalloys exposed to severe/harsh environmental conditions at high temperatures, the role of deformation induced defects on the degradation and define material design routes to slow down or suppress aspects of the degradation. The studies will be focused on γ/γʹ Ni-based superalloys and new CoNi based superalloys. More specifically, the atomic-scale environmental degradation of superalloys and their mechanisms will be explored by correlative use of electron microscopy and atom probe tomography. This includes the degradation of the alloys caused by oxidation, sulphidation and corrosion at high temperatures.