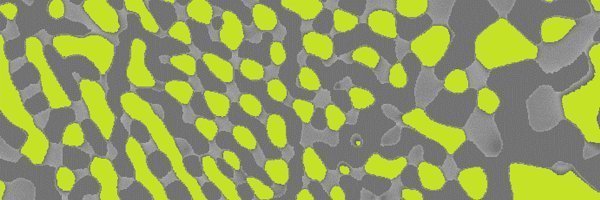
Economic and efficient processing of Fe–Al turbine parts (ProFeAl)
Because of their excellent corrosion resistance, high wear resistance and comparable low density, Fe–Al-based alloys are an interesting alternative for replacing stainless steels and possibly even Ni-base superalloys. Recent progress in increasing strength at high temperatures has evoked interest by industries to evaluate possibilities to employ Fe–Al-based alloys for various applications. These activities have matured to a point that industrial processing of parts is now investigated in more detail by considering economic aspects.
Within the project “Pro FeAl” funded by the German Ministry of Economics (Bundesministerium für Wirtschaft, BMWi; Grant No. 0324317C) a consortium of seven industries and research centers has evaluated possibilities for the economic and efficient processing of various turbine parts from different Fe–Al-based alloys. Within the project, the production of parts by sand castings for application up to 300 °C and by forging and additive manufacturing for use at higher temperatures were investigated.
For the casting route, an alloy developed at MPIE has been selected. In a first large-scale casting trial, successful production of various parts has been demonstrated. Further optimisation of microstructure and subsequent characterisation of cast parts was the task of MPIE in this part of the project.
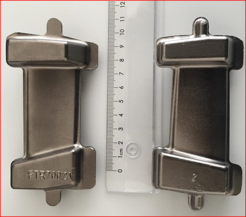
Forged Fe–Al compressor blades
For the forging route and for additive manufacturing, a new alloy had to be developed. Based on an existing alloy concept, MPIE investigated a more cost effective alternative based on Fe-Al-Nb(-B). Different alloy compositions were produced by vacuum induction melting. As a pre-requisite for the alloy development, phase equilibria in the Fe-corner of the Fe-Al-Nb system were established at 700 °C [1]. Microstructures were examined by light optical microscopy and scanning electron microscopy. Phases and their compositions were established by X-ray diffraction and electron probe microanalysis, respectively. For an aimed design of the microstructures, which are essential for the mechanical properties of the alloys, understanding the kinetics of the transformation from the metastable Heusler phase to the stable Laves phase is important. Besides establishing a TTT diagram for this transformation, knowledge of the actual composition of the phases is essential. Because the Heusler phase forms only nanometer-sized coherent precipitates, its composition was established by atom probe tomography [2].
After phase equilibria and kinetics were established, specific microstructures were attained through annealing of the alloys [3]. Basic mechanical properties such as microhardness, strength in compression and tension, brittle-to-ductile transition temperature (BDTT), KIC by charpy tests, and the creep behaviour were determined [4, 5].