Green nickel for sustainable electrification
Scientists at the Max Planck Institute for Sustainable Materials have developed a carbon-free, energy-saving method to extract nickel for batteries, magnets and stainless steel.
To the point
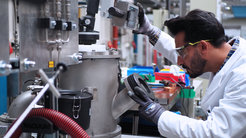
- Challenging nickel demand: the demand for nickel is expected to double while conventional nickel production emits around 20 tons of CO2 per one ton of nickel
- Sustainable new process for nickel production: Researchers found a way to extract nickel from low-grade ores using hydrogen plasma instead of carbon. The one-step process is CO2-free and saves energy and time.
- Upscaling possible: For upscaling, implementing short arcs with high currents, integrating an external electromagnetic stirring device beneath the furnace, or employing gas injection, is needed, making sure that the unreduced melt continuously reaches the reaction interface.
To combat climate change and achieve a climate-neutral industry, carbon emissions must be drastically reduced. A key part of this transition is replacing carbon-based energy carriers with electricity, particularly in transport and industrial applications. However, this shift heavily depends on nickel, a critical material used in batteries and stainless steel. By 2040, the demand for nickel is expected to double due to the increasing electrification of the infrastructures and transport systems. Yet, producing one ton of nickel currently emits around 20 tons of CO2, raising concerns about shifting the environmental burden from transportation to metallurgy. Researchers at the Max Planck Institute for Sustainable Materials (MPI-SusMat) have now developed a carbon-free, energy-saving method for nickel extraction. Their approach also enables the use of low-grade nickel ores, which have been overlooked due to the complexity of conventional extraction processes. The Max Planck team now published their results in the journal Nature.
One single step to green nickel
Manzoor and his colleagues have developed a new method to extract nickel from ores in a single step, using hydrogen plasma instead of carbon-based processes. If the CO2 emissions generated during the mining of nickel ore and its transport are considered, the new process reduces CO2 emissions by 84%. In addition, the process is up to 18% more energy-efficient when renewable electricity and green hydrogen are used, as the repeated heating and cooling of the ore, which is common in conventional processes, is avoided.

Traditionally, industry relies on high-grade ores, as extracting nickel from lower-grade ores is far more complex due to their chemically intricate composition. Unlike iron, which can be reduced in a single step by removing oxygen, nickel in low-grade ores is chemically bound within complex magnesium silicates or iron oxides. Conventional extraction involves multiple stages like calcination, smelting, reduction, and refining, which are energy-intensive and have a large carbon footprint. A major breakthrough of this method is its ability to process low-grade nickel ores (which account for 60% of total nickel reserves) in a single reactor furnace, where smelting, reduction, and refining occur simultaneously, producing a refined ferronickel alloy directly.
Towards industrial application
This method not only reduces emissions and energy consumption, but also broadens the spectrum of usable nickel ores, making extraction more cost-effective and sustainable. The next step for the Max Planck team is scaling up the process for industrial applications.
This can be achieved by implementing short arcs with high currents, integrating an external electromagnetic stirring device beneath the furnace, or employing gas injection. These are well-established industrial techniques, making integration into existing processes feasible.
The green nickel production route opens the door to a more sustainable electrification of the transport sector. The reduced nickel alloy can be used directly in stainless steel production and, with additional refinement, as a material for battery electrodes. Additionally, the slag produced during the reduction process can serve as a valuable resource for the construction industry, including brick and cement production. The same process can also be applied for cobalt, which is used in electric vehicles and energy storage systems.
The research was funded by an Advanced Grant of the European Research Council.
Author: Yasmin Ahmed Salem