Exploring nanomechanical behavior at extreme strain rates
The aim of the work is to develop instrumentation, methodology and protocols to extract the dynamic strength and hardness of micro-/nano- scale materials at high strain rates using an in situ nanomechanical tester capable of indentation up to constant strain rates of up to 100000 s−1.
Metallic alloys and ceramics are integral to numerous engineering applications due to their exceptional mechanical strength and durability. Traditionally, the mechanical behavior of these materials under quasi-static conditions has been the focus for the design and development of components across various demanding fields. However, real-world scenarios often subject these materials to rapid mechanical stimuli, resulting in strain rates ranging from 103 to 107 s−1 over mere microseconds. This abrupt increase in energy demands an in-depth understanding of the dynamic strength and failure mechanisms of materials. In the macroscopic scale (ranging from millimeters to centimeters), dynamic testing commonly relies on techniques such as the Kolsky bar and Split Hopkinson Pressure bar. However, these methods are inadequate for investigating the dynamic properties of materials at the micro- and nano-scales, where nanoindentation and microcompression are typically employed.
In this work a high-speed piezo-based micromechanical experimental setup was engineered to achieve indentation strain rates of 100000 s−1. Furthermore, a custom-modified electronics hardware and essential experimental protocols required to capture precise load-displacement signals during such high-strain rate indentations and extracting hardness values from them was developed. Subsequently, the work focuses on obtaining and understanding the material behavior response, specifically the hardness, for different classes of materials under these extreme strain rates.
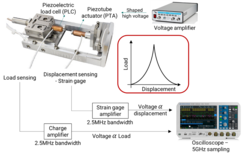