Additive micromanufacturing of 3D copper architectures
The aim of the Additive micromanufacturing (AMMicro) project is to fabricate advanced multimaterial/multiphase MEMS devices with superior impact-resistance and self-damage sensing mechanisms.
Microfabrication technologies are vital to the miniaturization of engineering components for applications in energy harvesting, electronic devices, and microelectromechanical systems (MEMS). One of the most promising emerging microfabrication techniques is localized electrodeposition in liquid (LEL), which is capable of freeform printing 3D metal microarchitectures and has the potential to transform research fields such as micro-/nanomechanics, microelectronics, MEMS fabrication and packaging, phononics, photonics, and catalysis. The aim of the Additive micromanufacturing (AMMicro) project is to fabricate advanced multimaterial/multiphase MEMS devices with superior impact-resistance and self-damage sensing mechanisms.
LEL combines electrochemical reduction with a highly sensitive force-sensing scheme, allowing real-time monitoring of the growth of each metal voxel (Exaddon AG). The local metal ions supply from the hollow AFM tip confines the electrochemical reduction to the substrate. The optical laser beam deflection system detects the completion of voxel deposition at the current location and moves the tip to the next deposition location. Therefore, LEL technique enables the printing of 3D metal microarchitectures with complex arbitrary shapes in a voxel-by-voxel layer-by-layer fashion. We are able to print different 3D architectures using LEL technique.
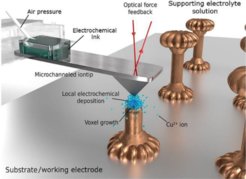
The printing of Cu micro-architectures has been successfully developed. We have successfully fabricated structures from simple micropillars to complicated octet microlattices.
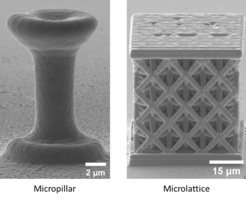
One of the aims of the AMMicro project is fabricate MEMS-based mechanical testing device that can be combined with microscopy technique to test nanomaterials at micro- and nanoscale. MEMS-based mechanical testing devices typically consist of two main parts: the sensing and the actuation. One of the key components for the MEMS-based device are springs with tunable stiffness, which cannot be fabricated in 3D shapes such as helices using traditional lithography-based fabrication method. However, such complex helix springs can be printed using the LEL technique.
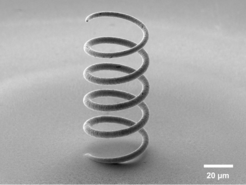