Dynamic thermomechanical testing of dewetted microparticles
“Smaller is stronger” is well known in micromechanics, but the properties far from the quasi-static regime and the nominal temperatures remain unexplored. This research will bridge this gap on how materials behave under the extreme conditions of strain rate and temperature, to enhance fundamental understanding of their deformation mechanisms. The mechanical behavior of different material systems is investigated in a statistically relevant manner using dewetted microparticles as the test-beds.
Specifically, in this project the behavior of metals with different crystal topologies, i.e. FCC, and alloy systems such as FeAl will be investigated. To have a statistically relevant study, pristine micro-particles obtained from dewetting of thin films will be in situ tested inside an SEM, using a state-of-the-art nanoindenter capable of true displacement control. This testing platform allows the strain rates to be varied from 0.0001/s to 1000/s, along with the ability to heat (up to 800°C) or cool down (up to -150°C) the sample during the experiment.
The mechanical metrology of micro/nano-scale metallic systems has critical implications for both scientific and industrial communities. However, there are very few studies that explore the mechanical behavior at small- scales under such extreme conditions in a statistically relevant manner. Through this project, we aim to tackle this critical lack of understanding of the mechanical behavior of small-scale metals. To that end, additively manufactured metal micropillars will be used to investigate the effect of size, defect density, strain rate and temperature on their compressive behavior in an automated manner. The pillars will be annealed to tackle the grain size and hence the defects in the samples. Further, in situ compression tests on these different pillar arrays will be used to investigate the effects of strain rate and temperature interdependence. These tests will be conducted in an automated manner. In addition, microstructural characterization using TEM+EBSD analysis will be performed prior to and post-test to reveal the deformation mechanisms responsible for the mechanical behavior at such extreme loading conditions. Concurrently, this experimental dataset in combination with already existing constitutive laws will be fed into a machine learning pipeline. Here the objective is to identify the key parameters among initial sample conditions and mechanical loading conditions that significantly influence the mechanical behavior of microscale metals.
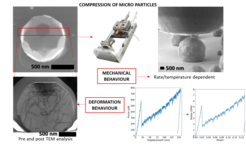