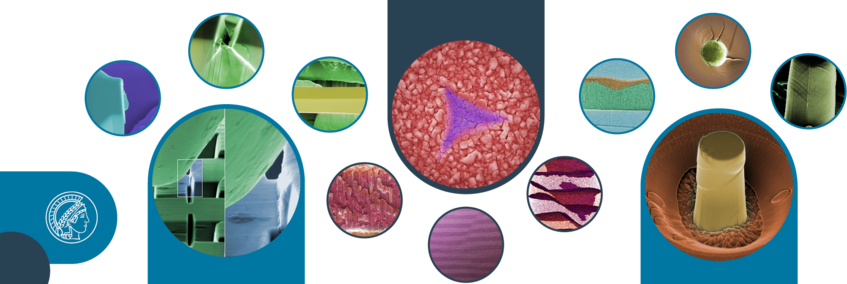
Temperature dependent nano- and microplasticity
Material strength and underlying plasticity mechanisms can change when deformed at micro- and nanometre length-scales. While being of fundamental scientific interest, such observations have significant implications for the design of advanced material systems, as for thin-films.
Nano- and microscale plasticity plays a critical role in various technological applications such as unravelling size dependent material behavior in modern miniaturized materials such as thin films in MEMS, in the case of local attrition based processes involved in solid state hydrogen reduction of iron oxide pellets for green steel making, or even unveiling the role of defects such as vacancies on the strength of alloys.
The concepts determined by testing bicrystals of Cu are extended to thin-films of Ag-doped Cu, containing a complex nanocrystalline nanotwinned structure. The segregation of Ag to Cu twin/GB nodes through mild heat treatment leads to an increase of the strength, where through collaboration with Dr. Tobias Brink we seek to understand and better describe mechanistically dislocation/GB interactions by atomistic simulations.
High-temperature deformation of iron oxide single crystals: In hydrogen-based direct reduction processes, iron oxide phases such as hematite and magnetite serve as the primary feedstock, with Wüstite acting as an intermediate phase, resulting in reduced alpha iron. However, contemporary solid-state reactors face notable challenges including excessive particle adhesion at temperatures surpassing 750°C, and the formation of a reaction layer on the outer surface, often leading to an unreacted Fe2O3 core, undermining process efficiency. Efforts to design future reactors must focus on promoting controlled fracture and delamination at the weakened metal/oxide interface induced by hydrogen. Nonetheless, there remains a considerable gap in understanding the micromechanical properties of iron oxide phases at elevated temperatures (600-800°C) and small length scales. The FeOx-HOTMECH project, funded by the KSB-Stiftung and undertaken by PhD student Shreehard Sahu, aims to elucidate the plasticity mechanisms of iron oxide phases in small volumes using nanoindentation and micropillar compression techniques, extending up to 800°C. This research will also investigate the brittle-to-ductile transition through microcantilever fracture analysis and further link with the plasticity mechanism. The findings from this project will provide crucial material parameters essential for the design of next-generation fluidised bed ironmaking processes with reduced environmental impact. Moreover, these insights will also facilitate the optimisation of ore grinding processes before fluidisation or pelletisation, as precise measurements of the fracture toughness of iron ores hold significant scientific and industrial relevance.
![Fig 1: Post deformation SEM image of [0-110] oriented hematite micropillar showing prismatic slip <-1120>{1100}; unpublished work of Shreehard Sahu](/5069024/original-1740655297.jpg?t=eyJ3aWR0aCI6MjQ2LCJvYmpfaWQiOjUwNjkwMjR9--1b2feb802bd51f6d665523da9f2f949d0922f4e8)
The unusual mechanical behaviour of B2 FeAl compounds: Fe-Al-based alloys with maximum Al contents of 50 at.% are regarded as potential structural material candidates for applications up to 800 °C owing to their excellent corrosion resistance, wear-resistance, relative low density, and comparably lower cost than high-alloyed steels or Ni-base superalloys. Nevertheless, B2-ordered FeAl alloys possess constitutional and thermal vacancies, which subsequently affect the alloy strength. Consequently, a direct evaluation and comparison of the mechanical properties of B2 FeAl alloys is in principle not possible if the alloys have different thermal histories or processing routes. Therefore, the aim of PhD student Jung-Soo Lee’s project, in a DFG-funded collaboration with Dr. Frank Stein and KIT, is to measure and compare the mechanical properties of different compositions of FeAl alloys using in situ nano- and micromechanical techniques by producing them in a single diffusion couple specimen. Based on this research, we aim to reveal the fundamental interrelation of the parameters (Al content, vacancy concentration, temperature etc.) on the mechanical properties, and couple to the results on larger specimens at KIT.
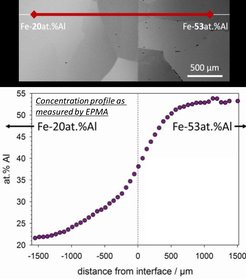
Extreme micromechanics of Cu grain boundaries: This project, led by PhD student Hendrik Holz and in collaboration with Dr. Ramachandramoorthy, aims to investigate the influence of grain boundaries on mechanical behavior at ultra-high strain rates and low temperatures. For this micropillar compression on copper bi-crystals containing different grain boundaries will be performed. Previous studies have shown that the strain rate sensitivity between single-crystalline and bi-crystalline micropillars of penetrable high angle grain boundaries differ significantly at quasi static strain rates pointing to the need of rearranging of dislocations when passing grain boundaries of such type (N.V. Malyar, et al., Scripta Mater.). This thermally activated process might be suppressed at high strain rates and low temperature which will be investigated within this project. Additionally, it is known that at higher strain rates the yield strength and deformation mechanism of materials changes significantly (J. W. Edington, et al., Philos. Mag. A J. Theor. Exp. Appl. Phys.). So far, the influence of individual grain boundaries on the rate-dependent behavior of metals remains largely unexplored. Additionally, the influence of temperature on the grain boundary interaction with dislocations and its influence on the mechanical response of metals also remain open for investigation. New developments in micromechanical testing equipment now enable displacement-controlled micropillar compressions in the ultra-high strain rate regime (upto 10000/s) (G. Guillonneau, et al., Materials and Design), at low temperatures (J. Ast, et al., Materials and Design), and also combined high strain rate and cryogenic conditions (J. Schwiedrzik, et al., Materials and Design). Using such a novel small-scale mechanical testing device, this project aims to unravel the mysteries of grain boundary interactions at ultra-high strain rates and low temperatures using bicrystal micropillar compression testing of copper and nanoindentation in the vicinity of grain boundaries. Additionally, the mechanical testing device will be adapted, so that it can perform high strain rate measurements at cryogenic conditions.
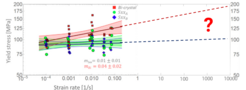
(Adapted from N.V. Malyar, et al., Scripta Materialia, 138 (2017))