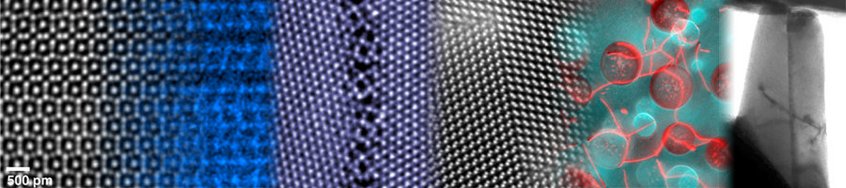
Advanced Microstructural Characterization of in situ Alloyed Nickel-Based Alloys by Welding
Nickel-based alloys are a particularly interesting class of materials due to their specific properties such as high-temperature strength, low-temperature ductility and toughness, oxidation resistance, hot-corrosion resistance, and weldability, becoming potential candidates for high-performance components that require corrosion resistance and good mechanical properties. This unparalleled combination of properties is achieved by adding alloying elements and changes in microstructure. This research project blended Ni-based metal welds produced by in situ alloying using the tandem GMAW process in a previous research project developed by the Welding Research and Technology Laboratory team at the Federal University of Ceará, in Brazil.
Despite evaluating various aspects of these prominent Ni-based alloys, several aspects concerning their microchemistry and phase transformations need to be evaluated at the nano- and atomic-scale to fully understand the Ni-based alloys' behaviors. Therefore, this research project is focused on the advanced microstructural characterization of in situ alloyed Ni-based alloys using high-resolution transmission electron microscopy and atom probe tomography.
The primary purpose of this research project is to evaluate these novel in situ blended Ni-based alloys on the nano- and atomic-scales to understand the relationship between the alloy composition, the microstructure evolution during processing (welding and heat treatment), and its correlation with the mechanical properties and corrosion resistance. This knowledge will be used to evaluate the suitability of these alloys for industrial applications.
Current state
The development of novel alloys with superior corrosion resistance and mechanical strength results in greater efficiency in using high-cost advanced materials. Many industrial applications require stainless steel or nickel-based alloy dissimilar welding and claddings, which are good options for corrosion protection at a low cost. However, in either case, it is not always possible to select the best alloy for a specific application due to several factors, including not being commercially available. Therefore, the development of new alloys to assure high strength associated with high toughness or improved corrosion resistance for aggressive environments are required for various industries.
The first step was adapting the tandem gas metal arc welding (T-GMAW) process as a technology for in situ manufacturing of specific alloys, using different commercially available alloys. This step was supported by the Brazilian funding agencies FUNCAP and CAPES under research project number AE1-0079-000490100/13 and carried out at the Welding Research and Technology Laboratory at the Federal University of Ceará in Brazil. This research was not limited to developing the methodology necessary to produce specific Ni-based alloys by in situ alloy welding but also to evaluate the microstructure, mechanical properties and corrosion resistance in the as-solidified state and after ageing treatments of these new alloys. The performance of the aforementioned in situ alloys produced by the T-GMAW process was seen to be outstanding. However, despite evaluating various aspects of these very promising Ni-based alloys, their microchemistry and related phase transformations need to be evaluated at the nano- and atomic-scale to further advance the properties of these joint material systems.
The next step of this research performed at MPIE aims to shed new light on the phase formation, including atomic-scale and nanoscale chemical variations along dislocations, grain boundaries, and interphases due to segregation induced during in situ alloying or post thermal heat treatment. Resolving the local structure and composition of the materials will enable us to investigate the formation the precipitate phases in the weld zone, their crystallography and composition as well as any defect structures. More detailed information on the 3D arrangement of nanoprecipitates and segregation of impurities and alloying elements along dislocations, grain boundaries, sub-grain boundaries and interphase boundaries will be obtained by APT. The atomic structure of interfaces will be analyzed by aberration-corrected scanning TEM. Revealing the underlying phase formation and transformations is crucial to understand the fundamental structure-property relationships, enabling us to tailor the properties of the joints by fine-tuning of the processing conditions to develop materials with outstanding mechanical stability under harsh environmental conditions.
The knowledge gain from this project will significantly impact the scientific and technological development in the field of metallurgy and materials science. Furthermore, establishing an academic and scientific cooperation between the Max-Planck-Institut Für Eisenforschung GmbH in Germany and the Federal University of Ceará in Brazil will provide adequate conditions for the strengthening of the collaboration between the partner countries, contributing to the needs of a globally functioning knowledge-based society.
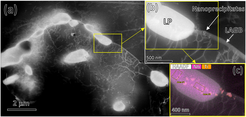