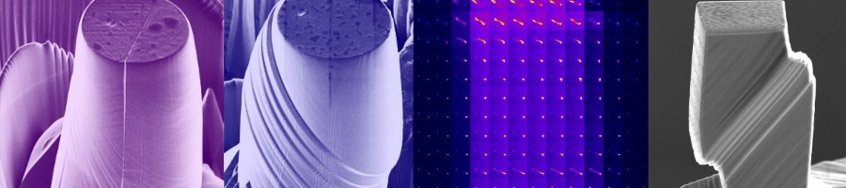
Local structure-property relationships in laser-processed materials
In this project, links are being established between local chemical variation and the mechanical response of laser-processed metallic alloys and advanced materials.
The intrinsically high local cooling and solidification rates of laser melting can lead to unique changes in chemical ordering including at microstructural defects. Within this space, we have studied the ZrCu-based bulk metallic glass system (AMZ4) regarding the role of oxygen-update in the characteristic local atomic order and the influence on the mechanical properties using macroscale fracture toughness measurements (shown in Figure below) together with analysing fingerprints of deformation with micropillar compression [1-4]. Similar approaches have been used for understanding chemical segregation and intermetallic formation in Al-alloys [5,6]. This work has been extended to optimise laser-processing of metallic glasses in collaboration with the University Duisburg-Essen, while similar concepts have also been applied to study chemical and structural damage in laser-processed [7,8] and ion beam processed [9,10] diamond.
![Highlight of work done on the laser-processed metallic glass AMZ4 [1,2]. In i) and ii) bulk-scale fracture toughness measurements were performed on both LPBF and cast AMZ4 on dimensions of width ~12 mm. From the load-displacement and SEM fractography measurements, LPBF AMZ4 showed a significantly more brittle response with KIC ~25 MPa √m compared to the plastically deformable cast AMZ4 with KQ ~120 MPa √m. The critical difference found between samples is the atomic-scale order, affected by both thermal history and oxygen content in the alloy iii). Micropillar compression measurements in iv) show that the intrinsic mechanical response varies between samples, linked to the influence of local chemical ordering on the ease for shear transformation during deformation.](/4750858/original-1646823820.jpg?t=eyJ3aWR0aCI6MjQ2LCJvYmpfaWQiOjQ3NTA4NTh9--c7880e86fc7fde82927fa39cddcc6e9d430886c5)
Publication References
- Best, J.P., et al., Fracture and fatigue behaviour of a laser additive manufactured Zr-based bulk metallic glass. Additive Manufacturing, 2020. 36: p. 101416. DOI: 10.1016/j.addma.2020.101416
- Best, J.P., et al., Relating fracture toughness to micro-pillar compression response for a laser powder bed additive manufactured bulk metallic glass. Materials Science and Engineering: A, 2020. 770: p. 138535.DOI: 10.1016/j.msea.2019.138535
- Ramachandramoorthy, R., et al., High strain rate in situ micropillar compression of a Zr-based metallic glass. Journal of Materials Research, 2021. 36(11): p. 2325-2336. DOI: 10.1557/s43578-021-00187-5
- Best, J.P. et al., Structural periodicity in laser additive manufactured Zr-based bulk metallic glass. Applied Physics Letters, 2019. 115: p. 031902. DOI: 10.1063/1.5100050
- Best, J.P., et al., Mechanical Anisotropy Investigated in the Complex SLM-Processed Sc- and Zr-Modified Al–Mg Alloy Microstructure. Advanced Engineering Materials, 2019. 21(3): p. 1801113. DOI: 10.1002/adem.201801113
- Paul, M.J., et al., Fracture resistance of AlSi10Mg fabricated by laser powder bed fusion. Acta Materialia, 2021. 211: p. 116869. DOI: 10.1016/j.actamat.2021.116869
- Mouhamadali, F., et al., Nanosecond pulsed laser-processing of CVD diamond. Optics and Lasers in Engineering, 2020. 126: p. 105917. DOI: 10.1016/j.optlaseng.2019.105917
- Cadot, G.B.J., et al., Investigation of the microstructure change due to phase transition in nanosecond pulsed laser processing of diamond. Carbon, 2018. 127: p. 349. DOI: 10.1016/j.carbon.2017.10.030
- Isa, F., et al., Stress engineering of boron doped diamond thin films via micro-fabrication. APL Materials, 2021. 9: p. 061109. DOI: 10.1063/5.0051196
- Chen, M., et al., Influence of helium ion irradiation on the structure and strength of diamond. Carbon, 2020. 158: p. 337. DOI: 10.1016/j.carbon.2019.10.078