Modulus
Laser Powder Bed Fusion (LPBF) is the most commonly used Additive Manufacturing processes. One of its biggest advantages it offers is to exploit its inherent specific process characteristics, namely the decoupling the solidification rate from the parts´volume, for novel materials with superior physical and mechanical properties. One prominet example are so called High Modulus Steels, where the combination of strong, ductile and tough metallic matrices with stiff ceramic particles allows the specific modulus (E/ρ) to be increased compared to conventional materials such as aluminum or steel, thereby reducing weight. The aim of this project is to elucidate the synthesis/microstructure/property causalities of high modulus steel fabricated with the LPBF process.
New lightweight construction concepts and the resulting reduction in weight are constantly presenting the development of new materials and processes with new challenges. A promising way to reduce weight is the combination of new materials and additive manufacturing, especially the LPBF process. The material used here is an iron-based high-modulus steel with TiB2 particles, which forms nanometer-sized particles in-situ in a ferritic base matrix through processing with the LPBF process. The combination of strong, ductile and tough metallic matrices with stiff ceramic particles allows the specific modulus (E/ρ) to be increased compared to conventional materials such as aluminum or steel, thereby reducing weight. The aim of this project "MODULUS" is to enable the processing of the HMS with the LPBF process into pore-free components and to gain a deeper understanding of the mechanisms within the material.
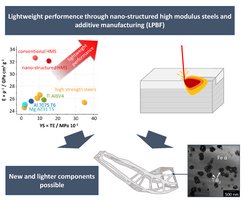