Fundamentals of sustainable hydrogen-based metallurgy
The massive CO2 emissions associated with modern iron- and steelmaking have become one of the largest environmental burdens of our generation, and the international steel market is forecast to grow by at least 30–35 % during the next 30 years [1, 2]. Therefore, the institute conducts interdisciplinary and multiscale research on the physical and chemical foundations for improving the sustainability of steels, with a focus on reduced CO2-intense production and low-energy synthesis. These goals can in principle be reached by combining several types of iron carriers, such as oxidic fines, lump ore, or scrap, with a variety of carbon-free reduction media, such as hydrogen or ammonia, in different types of furnaces.
The interplay of multiple mechanisms and influencing factors both, from the reactive metallurgy side and from the advanced processing side, requires the cooperation of several departments on this topic. This includes the design and operation of fully instrumented reactor set-ups in which the different feedstock materials can be charged, while the underlying redox reactions can be monitored through the spectroscopy of the intermediate and final reaction products.
The specific focus of this cross-departmental initiative is currently placed on hydrogen-based direct reduction [3] and hydrogen-based plasma smelting reduction of iron ores [4]. As raw materials, commercial pellets and ore fines are used, as well as well-defined oxide single crystals. The hydrogen-based direct reduction of iron oxides is a solid-gas reaction. The kinetics of this process is not well understood, particularly during the wüstite reduction step, which is nearly an order of magnitude slower than the hematite reduction.
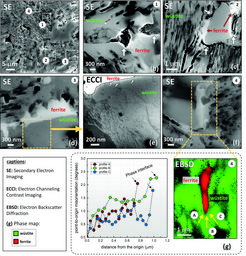
The rate-limiting factors of this reaction are investigated and related to the microstructure and local chemistry of the ores, using a multiscale structure and composition analysis of iron reduced from hematite with pure molecular hydrogen reaching down to near-atomic scale [3]. During reduction, a complex pore- and microstructure evolves, due to oxygen loss and several non-volume-conserving phase transformations. The microstructure after reduction is an aggregate of nearly pure iron crystals, containing inherited and acquired pores and cracks (Fig. 1). We observe several types of lattice defects that accelerate mass transport as well as several chemical impurities (Na, Mg, Ti, V) within the Fe in the form of oxide islands that were not reduced.
Hydrogen-based plasma smelting reduction offers an attractive alternative to green steel production. Therefore, the basic mechanisms behind the reduction of hematite using hydrogen plasma are studied [4]. The reduction kinetics depends on the balance between the input mass and the arc power. For an optimized input mass-arc power ratio, the complete reduction was obtained within 15 min of exposure to the hydrogen plasma. In such a process, wüstite reduction is again the rate-limiting step. Nevertheless, its rates are comparable with those found in hydrogen-based direct reduction. The possible advantage of the reduction of ores through a reductant plasma in an electric arc lies in the fact that reduction and liquification are done in a single process step.
Micro- and nanoscale chemical and microstructure analysis revealed that the gangue elements partition to the remaining oxide regions (Fig 2). Si-enrichment was observed in the interdendritic fayalite domains, at the wüstite/α -iron interfaces, and in the primarily solidified oxide particles inside the iron. With proceeding reduction, however, such elements are gradually removed from the samples so that the final iron product is nearly free of gangue impurities. The studies provide microstructural and atomic-scale insights into the composition and phase transformations during hydrogen-based plasma smelting reduction, enabling better understanding of the underlying thermodynamics and kinetic barriers of this process, as a basis for the design of suited furnace concepts for CO2-free ironmaking.
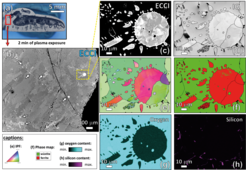
The hydrogen-based direct reduction of iron oxides is also investigated theoretically. A chemo-mechanically coupled phase-field model is currently under development, to explore the interplay between phase transformation, chemical reaction, component diffusion, elastoplastic deformation, and microstructure during the reduction of wüstite with hydrogen (Fig. 3).
The phase-field simulation is coupled to Gibbs free energy data that are fitted from corresponding thermodynamic databases. The simulation reveals the important role of elastic and plastic deformation during the reduction and allows first insights into the different mass transport pathways along the highly defected microstructure. The model also allows to better understand both, the main decelerating factors (oxide-core-metal-shell structures) and accelerating factors (delamination and fracture at the hetero-interfaces) determining the overall reduction kinetics.
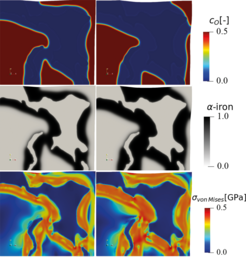
- IEA. Iron and Steel Technology: Towards More Sustainable Steelmaking (International Energy Agency, 2020).
- Pei, M.; Petäjäniemi, M.; Regnell, A.; Wijk, O.: Metals 10 (2020) 972.
- Kim, S.H.; Zhang, X.; Ma, Y.; Souza Filho, I.R.; Schweinar, K.; Angenendt, K.; Vogel, D.; Stephenson, L.T.; El-Zoka, A.A.; Mianroodi, J.R.; Rohwerder, M.; Gault, B.; Raabe, D.: Acta Mater. 212 (2021) 116933.
- Souza Filho, I.R.; Ma, Y.; Kulse, M.; Ponge, D.; Gault, B.; Springer, H.; Raabe, D.: Acta Mater. 213 (2021) 116971.