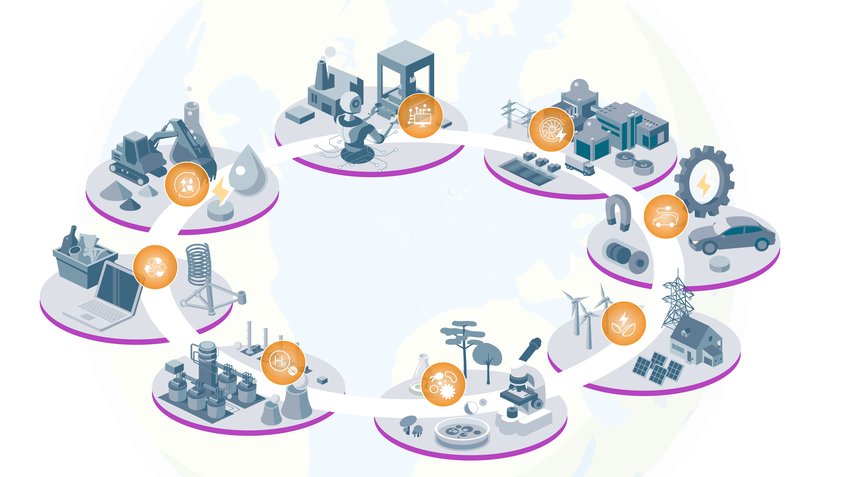
Sustainability of and through materials
Shaping our future in terms of sustainable technologies, new materials and industrial processes is one of the most important topics of our generation and we are in need of scientific and engineering answers. How can we avoid the use of carbon as energy and reductant carrier in the entire field of materials science and engineering? How can we make better and rare-earth free permanent magnets for electrical vehicles? How can we render alloys sustainable and improve recycling rates? Which are the novel materials that can withstand embrittlement caused by hydrogen? And what is the potential of new thermoelectric and solar cell absorber materials for green power generation? We have devoted our efforts to provide answers to these pressing questions, showing you here some of our current research in the field of sustainability.
Explanatory Videos
All topics concerning sustainability and decarburization