The dual role of martensitic transformation in fatigue crack growth
About 90% of all mechanical service failures are caused by fatigue. Avoiding fatigue failure requires addressing the wide knowledge gap regarding the micromechanical processes governing damage under cyclic loading, which may be fundamentally different from that under static loading. This is particularly true for deformation-induced martensitic transformation (DIMT), one of the most common strengthening mechanisms for alloys. Here, we identify two antagonistic mechanisms mediated by martensitic transformation during the fatigue process through in situ observations and demonstrate the dual role of DIMT in fatigue crack growth and its strong crack-size dependence. Our findings open up avenues for designing fatigue-resistant alloys through optimal use of DIMT. They also enable the development of physically based lifetime prediction models with higher fidelity.
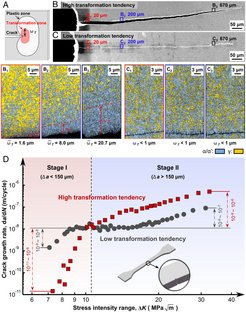
Deformation-induced martensitic transformation (DIMT) has been used for designing high-performance alloys to prevent structural failure under static loads. Its effectiveness against fatigue, however, is unclear. This limits the application of DIMT for parts that are exposed to variable loads, although such scenarios are the rule and not the exception for structural failure. Here we reveal the dual role of DIMT in fatigue crack growth through in situ observations. Two antagonistic fatigue mechanisms mediated by DIMT are identified, namely, transformation-mediated crack arresting, which prevents crack growth, and transformation-mediated crack coalescence, which promotes crack growth. Both mechanisms are due to the hardness and brittleness of martensite as a transformation product, rather than to the actual transformation process itself. In fatigue crack growth, the prevalence of one mechanism over the other critically depends on the crack size and the mechanical stability of the parent austenite phase. Elucidating the two mechanisms and their interplay allows for the microstructure design and safe use of metastable alloys that experience fatigue loads. The findings also generally reveal how metastable alloy microstructures must be designed for materials to be fatigue resistant.