Hybrid hydrogen-based reduction of iron ores
Replacing carbon by hydrogen as the reducing agent in ironmaking offers a pathway to massively reduce the associated CO2 emissions. However, the production of hydrogen using renewable energy will remain as one of the bottlenecks at least in the next two decades. The underlying reasons are the low electrolysis productivity and the insufficient capacities in both renewable electricity and industrial infrastructures to produce sufficient amounts of green hydrogen, especially in view of the gigantic demand for currently 1.8 billion tons of steel being produced every year, with forecasts predicting 2.4 billion tons by the year 2040. We therefore demonstrate how the efficiency in hydrogen and energy consumption during iron ore reduction can be dramatically improved by the knowledge-based combination of two technologies: partially reducing the ore at low temperature via solid-state hydrogen-based direct reduction (HyDR) to a kinetically defined degree, and subsequently melting and completely transforming it to iron under a reducing plasma (i.e. via hydrogen plasma reduction, HPR)
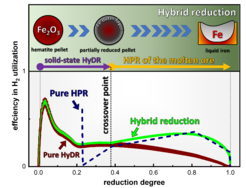
The lab-scale results suggest that an optimal transition point between the HyDR and HPR technologies occurs where their efficiency in hydrogen utilization is equal. We found that the reduction of hematite through magnetite into wüstite via HyDR is clean and efficient, but it gets sluggish and inefficient when iron forms at the outermost layers of the iron ore pellets, Figure 1. Conversely, HPR starts violently and unstably with arc delocalization, but proceeds smoothly and efficiently when processing semi-reduced oxides (Figure 2), an effect which might be related to the material’s high electrical conductivity.
We performed hybrid reduction experiments by partially reducing hematite pellets via HyDR at 700°C to 38% global reduction (using a standard thermogravimetry system) and subsequently transferring them to HPR, conducted with a lean gas mixture of Ar-10%H2 in an arc-melting furnace, to achieve full conversion into liquid iron. This hybrid approach allows to exploit the specific characteristics and kinetically favourable regimes of both technologies, while simultaneously showing the potential to keep the consumption of energy and hydrogen low (green line in Figure 1) and improve both, process stability and furnace longevity by limiting its overexposure to plasma radiation.
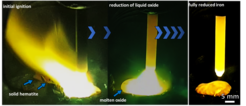