Environmental small-scale mechanics
The field of micromechanics has seen a large progress in the past two decades, enabled by the development of instrumented nanoindentation. Consequently, diverse methodologies have been tested to extract fundamental properties of materials related to their plastic and elastic behaviour and fracture toughness. Established experimental protocols are carried out either at atmospheric conditions or at ultra-high vacuum inside an electron microscope.
Our aim at the MPIE is to expand the methodology to either minimize the influence of varying experimental and instrumental factors (such as atmospheric humidity, temperature, and oxygen content) or to mimic service conditions.
A custom-made environmental chamber was built to host a micromechanical testing device. The steel chamber can operate in vacuum UHV up to 10-6 mbar or in different gas atmospheres such as inert gas (nitrogen or argon), forming gas or dry air. In the original design a high-temperature microscale loading rig (also tailor-made) was installed in the chamber for micromechanical testing at temperatures up to 600 °C in vacuum [1]. Current adaptations to the chamber allow hosting a newly acquired nanoindentation system. Tension, compression, bending and fatigue tests can be performed in this true displacement-controlled system in standard and extreme conditions, like variable temperature (-120 to 800 °C) or high strain rates (up to ~103-104 s-1). In addition, this modular system can accommodate our custom-designed electrochemical cell for hydrogen charging and extreme conditions [2].
This system, composed by the nanoindenter adapted inside the environmental chamber, is currently shared between three newly established groups in the SN department working on micromechanics in different environments:
- The group of M. J. Duarte Correa studies the deformation processes and fracture behaviour of materials under different chemical/electrochemical environments, and particularly during hydrogen charging. A customized electrochemical cell designed in-house [2] and adapted to the modular nanoindenter system will be used to understand the mechanisms leading to hydrogen embrittlement. The gas atmosphere provided in the chamber will serve to minimize hydrogen desorption and formation of concentration gradients.
- R. Ramachandramoorthy’s group will primarily use the environmental chamber to conduct dynamic testing of micro-to-meso scale architectures under application-relevant atmospheric conditions including high-humidity (for biomaterials) and inert gas (such as argon for high/cryo temperature testing). Specifically, using a combination of optical microscope and high-speed camera the deformation processes during high strain rate mechanical testing of complex 3D architectures will be captured.
- The group of J. Best looks to investigate controlled microscale crack growth and plasticity of engineering alloys, along with variable temperature measurements, under different environmental conditions such as local oxidative or inert gas (such as argon for high/cryo temperature testing).
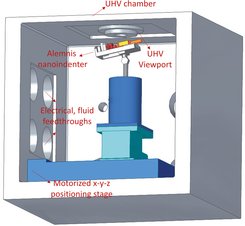
1. Arigela, V.G.; Palukuri, N.R.; Singh, D.; Kolli, S.K.; Jayaganthan, R.; Chekhonin, P.; Scharnweber, J.; Skrotzki, W.: J. Alloys Compd. 790 (2019) 917.
2. Duarte, M.J.; Fang, X.; Rao, J.; Krieger, W.; Brinckmann, S.; Dehm, G.: J. Mater. Sci. 56 (2021) 8732.