Bidirectional transformation induced plasticity in dual-phase high entropy alloys
Recently developed dual-phase high entropy alloys (HEAs) exhibit both an increase in strength and ductility upon grain refinement, overcoming the strength-ductility trade-off in conventional alloys [1]. Metastability engineering through compositional tuning in non-equimolar Fe-Mn-Co-Cr HEAs enabled the design of a dual-phase alloy composed of metastable face centered cubic (fcc) and hexagonal closed packed (hcp) phases.
This microstructure emerges in a Fe50Mn30Co10Cr10 (at.%) alloy after cooling from the high temperature single phase region to room temperature through a partial martensitic transformation. Both fcc- and hcp-phases are single phase supersaturated solid solutions and the microstructural refinement associated with the martensitic transformation leads to an increase in ultimate tensile strength from ~650 MPa to ~850 MPa and total elongation from ~50% to ~75% when reducing the grain size from 45 µm to 4.5 µm [2].
We have used length scale bridging transmission electron microscopy (TEM) observations in combination with in situ straining in the scanning TEM (STEM) to unravel the underlying microstructural origin of this outstanding property combination in the dual-phase HEA (Fe50Mn30Co10Cr10 (at.%)). In the as-quenched condition, a hierarchical, nanolaminated structure is observed in both fcc (g) and hcp (e) phases. Upon bulk tensile straining, the microstructure dynamically refines and secondary strain-induced e-nanolaminates form within the g-block in the hcp e-block, a high density of phase transformation induced g-nanolaminates and -twins is developing. These static post-deformation observations suggest that both forward gàe and backward eàg transformations are the main carriers of plasticity in this metastable dual-phase high entropy alloy.
We also performed in situ straining in the STEM using a custom build Cu-straining support in a displacement controlled Gatan straining holder to probe the dynamic evolution of the hierarchical nanolaminated microstructure as shown in Fig. 1a. The pre-existing hcp e-nanolaminates in the g-block are observed to grow by the motion of their leading partial dislocation and their number density increases upon straining. Interestingly, we could observe the dynamic strain induced forward gàe and backward eàg transformation in situ in the region indicated by an orange rectangle in Fig. 1a, referred to as “bidirectional transformation induced plasticity” (Bi-TRIP) effect.
In the early stages of straining, the nucleation of e-plates (HCP-1-3) is observed (Fig. 1a), which continue to grow with increasing strain until their extension is blocked by the primary S3 twin boundary. By further straining, the HCP-1 and HCP-2 plates are reverted to fcc, as well as the HCP-3 plate at a later stage (not shown here). The trailing partial dislocation unzips the hcp nanolaminates, thus establishing the underlying mechanism for a novel reversable TRIP effect.
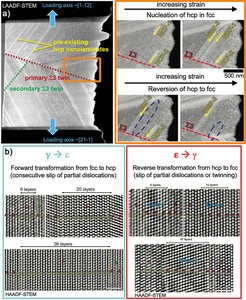
The key ingredients controlling this bidirectional transformation are the stacking fault energy, local temperature and stress-strain fields. The stacking fault energy is estimated to ~6.5 mJ/m2 for this dual-phase HEA promoting the forward gàe transformation and building the basis for the reverse transformation, since local temperature or strain fluctuations can initiate the reversion by the motion of trailing partial dislocations. The reverse eàg transformation depends on local stress or temperature fluctuations during straining, since the hcp e-phase is more stable than g at room temperature. We observed that due to such fluctuations the partial dislocations moved in some cases back, thus reversing the initial phase transformation.
This concept was further extended in an interstitial HEA by deformation-driven bidirectional transformation. Controlled cold-rolling and tempering promote the formation of dual-phase nanostructures, nano-grains and -twins in a Fe49.5Mn30Co10Cr10C0.5 (at.%) alloy resulting in an ultimate tensile strength of 1.05 GPa and a total elongation of 35 % [3]. The key design element is the tuning of the materials stacking fault energy close to its thermodynamic limit to trigger forward and reverse phase transformations upon loading. By joint activation of Bi-TRIP and twinning induced plasticity (TWIP) an excellent strength-ductility synergy can be achieved in tempered specimens with preceding-rolling reduction of 34 %.
Obtaining reliable values of stacking fault energies (SFEs) and hence relative stabilities of the fcc- and hcp-phases in these compositionally complex alloys also at non-zero temperatures is to date a big challenge. We have developed a set of density functional theory-based methods to compute the concentration dependence of SFEs [4] including magnetic and temperature effects [5]. To account for chemical disorder, different techniques are used such as the coherent potential approximation or special quasi random structures. Many of these alloys reveal complex antiferromagnetic interactions and it turned out that for achieving agreement with experimental data it is crucial to go beyond the assumption of idealized paramagnetic alloys with a careful treatment of magnetism and magnetic fluctuations [6].
References
- Li, Z.; Pradeep, K.G.; Deng, Y.; Raabe, D.; Tasan, C.C.: Nature 534 (2016) 227.
- Lu, W.; Liebscher, C.H.; Dehm, G.; Raabe, D.; Li, Z.: Adv. Mater. 30 (2018) 1804727.
- Su, J.; Wu, X.; Raabe, D.; Li, Z.: Acta Mater. 167 (2019) 23-39.
- Guo, W.; Su, J.; Lu, W.; Liebscher, C.H.; Kirchlechner, C.; Ikeda, Y.; Körmann, F.; Liu, X.; Xue, Y.; Dehm, G.: Acta Mater. 185 (2020) 45.
- Li, Z.; Körmann, F.; Grabowski, B.; Neugebauer, J.; Raabe, D.: Acta Mat. 136 (2017) 262.
- Wu, X; Li, Z.; Rao, Z.; Ikeda, Y.; Dutta, B.; Körmann, F.; Neugebauer, J.; Raabe, D.: Phys. Rev. Materials 4 (2020) 033601.