Defect phases – Thermodynamics and influence on material properties
To design novel alloys with tailored properties and microstructure, two materials science approaches have proven immensely successful: Firstly, thermodynamic and kinetic descriptions for tailoring and processing alloys to achieve a desired microstructure. Secondly, crystal defect manipulation to control strength, formability and corrosion resistance.
However, to date, the two concepts remain essentially decoupled. A bridge between them is needed to achieve a single conceptual framework. A powerful concept to establish such a bridge are defect phase diagrams, which provide systematic tools to describe and analyse the possible chemical and structural states that specific defects can have as function of key state variables, such as chemical composition, temperature or strain.
Scientists from the RWTH Aachen University and MPIE established a large scale collaborative research centre (CRC) funded by the German Research Foundation (DFG) aiming at a fundamentally new approach to achieve this goal. The key concept are defect phase diagrams, which describe the coexistence of and transitions between defect phases. The availability of such a framework will enable a paradigm shift in the description and design of future engineering materials [1].
![Fig. 1: Modelling framework of defect phase diagrams. The experimental space visualizes the experimental degrees of freedom. The variety of phase diagrams for bulk and all kinds of defects is represented in the μ-space. The engineering space considers parameter dependent materials properties. Adopted from Ref. [1].](/4694965/original-1643028360.jpg?t=eyJ3aWR0aCI6MjQ2LCJvYmpfaWQiOjQ2OTQ5NjV9--4929ebd144b9d1fe8bf91c3e8244fc07de8f725a)
Formally, a ‘defect phase’ is a structurally and chemically distinct atomic-scale defect configuration for which all physical properties can be expressed as smooth (continuous and infinitely differentiable) functions of intensive control variables such as temperature or chemical potential. A structure can only be considered a defect phase, if it is spatially confined at or next to the defect.
While the concept of defect phases has been theoretically postulated and discussed more than four decades ago, their actual observation became only possible recently with the availability of experimental techniques with atomic resolution such as aberration corrected transmission electron microscopy (TEM) and atom probe tomography (APT). For example, in a correlative study of both techniques, a local change of structure and chemistry next to dislocations in high-Mn austenitic steel and in Au-Pt alloys has been observed in the MA department [2, 3]. Nevertheless, using these highly advanced experimental techniques to systematically map defect phases (left side of Fig. 1) would be too time-consuming and due to a sensitive dependence on the thermodynamic state variables rather challenging. In the CRC we therefore aim at an alternative strategy to identify defect phases, namely guided probing. Here, physical properties of materials such as the elastic modulus or the corrosion behaviour are monitored in order to identify abrupt changes as function of the chemical potential of the involved species (right side of Fig. 1).
Since the chemical composition at and around defects is intrinsically inhomogeneous, e.g., due to segregation, the natural state variable is not the concentration like for bulk phases, but the chemical potential. The constancy of the chemical potential throughout the sample in chemical equilibrium (μ-space in Fig. 1) allows one to plot the phase diagram of the bulk material and of the individual defects in the same coordinate system. This property provides a direct route to connect bulk properties with those of various defects that give rise to the complex microstructure and surfaces of materials. For the latter, the MPIE has a long-standing expertise in deriving surface phase diagrams, which is now being applied and extended within the framework of the CRC to study, e.g., the impact of alloying Mg with Ca and Al on surface structure and stoichiometry (Fig. 2). Similar defect phase diagrams can also be constructed for phase boundaries, grain boundaries, dislocations, or point defects.
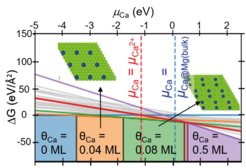
The rapid improvement of atomistic simulations revealed that defect phases are not rare exceptions, but should be a common feature in materials. For example, simulations in the CM department showed already in 2015 that dependent on the chemical potential of H in fcc Ni, the formation of a local hydride can be observed next to edge dislocations [4]. This is remarkable, because the hydride phase is not stable in the bulk at ambient conditions. Further extensive simulations have been performed in the CM department on grain boundaries, confirming the observation of defect phases in Al alloys by the SN department [5].
Recently, we have investigated stacking faults in the Nb-rich C14 Laves phase NbFe2. The bulk phase diagram of Fe-Nb suggests a rather narrow solubility of Nb in this phase, due to the formation of the competing Nb6Fe7 μ-phase. Instead of this phase, however, a large number of various types of planar defects is observed in experiment [6]. The atomic configurations of these defects have been characterized by aberration-corrected scanning TEM in the SN department and density functional theory (DFT) calculations in the CM department (Fig. 3). These studies reveal that some of the stacking faults contain one layer of the characteristic Zr4Al3 type unit of the μ-phase (red shaded crosses in the TEM image), i.e., correspond to a defect phase that is stabilized by an excess Nb content. Nevertheless, the confinement and the stacking of atomic layers does not correspond to a bulk phase, but rather fulfil the definition of defect phases provided above.
Apart from the basal defect shown in the upper part of Fig. 3 a variety of different extended and confined stacking faults, that are lying parallel to the basal or pyramidal habit planes are observed. The DFT calculations have been used to determine the relative stability of these defect structures. In the lower part of Fig. 3 the formation energy of selected stacking faults is plotted as a function of the chemical potential. The shading in grey indicates the stability region of the C14 bulk phase. Slightly below the phase equilibrium of the μ-phase (vertical line at μNb»0.01 eV), one can see the relative stability of the extended basal stacking observed in experiment. Other defect structures become lower in energy than the extended basal structure for certain chemical potentials, but do not lead to stable defect structures.
Based on these early successes, we envisage that defect phase diagrams will play the same role as their bulk counterparts. They will allow the selection of defects with a desired structural and chemical configuration, which in turn are the carriers of specific defect-property relations and, hence, enable the atomistically guided design of materials with tailored mechanical and corrosion properties.
![Fig. 3: Stacking faults phases in the Nb-rich C14 Laves phase NbFe2. Upper left: STEM image of an extended basal stacking fault. Upper right: Atomistic structure of the same defect as used for DFT calculations. Below: Defect phase diagram of several stacking faults (lines) as compared to the bulk phase diagram (shading). Adopted from Ref. [6].](/4695058/original-1643028360.jpg?t=eyJ3aWR0aCI6MjQ2LCJvYmpfaWQiOjQ2OTUwNTh9--87b98dfb2aa2128c2a436a9b1316f52788da2980)
References
- Korte-Kerzel, S.; Hickel, T.; Huber, L.; Raabe, D.; Sandlöbes-Haut, S.; Todorova, M.; Neugebauer, J.: Int. Mater. Rev. (2021) in press.
- Kuzmina M.; Herbig M.; Ponge D.; Sandlöbes, S.; Raabe, D.: Science 349 (2015) 1080.
- Zhou X.; Mianroodi, J. R.; Da Silva, A. K.; Koenig, T.; Thompson, G. B.; Shanthraj, P.; Ponge, D.; Gault, B.; Svendsen, B.; Raabe, D.: Sci. Adv. 7 (2021) 1.
- Leyson, G.; Grabowski, B.; Neugebauer, J.: Acta Mater. 89 (2015) 50.
- Zhao, H.; Huber, L.; Lu, W.J.; Peter, N.J.; An, D.Y.; De Geuser, F.; Dehm, G.; Ponge, D.; Neugebauer, J.; Gault, B.; Raabe, D.: Phys. Rev. Lett. 124 (2020) 6.
- Šlapákováa , M.; Zendegani, A.; Liebscher, C.H.; Hickel, T.; Neugebauer, J.; Hammerschmidt, T.; Ormeci , A.; Grin, J.; Dehm, G.; Kumar, K.S.; Stein, F.: Acta Mater. 183 (2020) 362.