Fe–Al - Sustainable alloys for demanding applications
Iron aluminide (Fe–Al) alloys are materials based on the intermetallic phases Fe3Al and FeAl [1, 2]. Due to their relatively high Al content they form Al2O3 scales in oxidising environments. Specifically α-Al2O3 scales, which are dense, thin and adherent, are very protective against degradation of Fe–Al in aggressive environments [3, 4]. Also due to their Al content, a passive hydroxide layer forms in humid air, which acts as a lubricant, thereby minimising friction and contributing to the excellent wear behaviour of these alloys.
The high Al content of more than 20 at.% also makes the alloys a light-weight material. The density of Fe-Al alloys is about 5.7–6.7 g/cm3, i.e. only about 80 % of that of Cr-Ni-steels or about 70 % of Ni-base superalloys. As these are typical candidates that can be possibly replaced by Fe-Al, their substitution has a number of advantages [1, 2]
- For moving parts, e.g. turbine blades, fuel saving can be expected due to the lower weight of Fe–Al.
- Better corrosion and wear resistance of Fe–Al should result in less maintenance and longer lifetime.
- The excellent corrosion resistance may also enable higher operation temperatures, thereby further reducing energy consumption.
- For large industrial facilities, support structures could be much leaner, e.g. if for a steam cracker Fe–Al tubes would be employed.
However, for industries the comparative low price of Fe–Al is of foremost interest. Fe and Al are non-strategic elements, which are actually the two most abundant metals in the earth’s crust, and Fe-Al needs comparatively little alloying for fine-tuning the properties. Consequently, there has been a large number of industrial projects within recent years, investigating various processing routes for Fe–Al and for a variety of applications [5]. It has been shown that Fe–Al can be processed on standard equipment, e.g. by induction melting in air, by sand, permanent mould or investment casting, by forging, or even by additive manufacturing [6].
“Process development for economic and efficient turbine parts made of iron aluminides (Fe–Al)” is one of these ongoing MPIE projects with partners from academia and companies of different industry branches. It builds up on previous projects, where Fe–Al–Ta alloys had already been qualified for such applications. The part where the MPIE is involved in the project now aims to elucidate whether Fe–Al–Nb could replace this more costly alloy [7].
Insufficient strength above 500 °C has for long time been an obstacle for a wider application of Fe–Al alloys [1, 2]. Specifically, at the MPIE a number of alloying strategies have been developed, which yielded Fe–Al alloys whose creep resistance matches or even surpasses that of advanced steels and of plain Ni-base alloys at 700 °C. One of these strategies relies on the formation of a metastable Heusler phase. The phase could either act as a strengthening phase by forming a fine-scaled, coherent microstructure with the matrix or through aimed transformation into the stable Laves phase. The basic mechanism of the latter transformation and how it can be influenced by doping, mechanical deformation or heat treatments are understood [8]. However, for a quantitative analysis of the transformation, specifically the chemical composition of the Heusler phase, but also their morphology and distribution within the matrix, have to be quantified. As the metastable precipitates are nanometre-sized, atom probe tomography (APT) is very well suited for their analysis.
APT provides three-dimensional chemical information at the sub-nanometre resolution [9], which allows us to study the formation of these fine L21 precipitates and their compositional evolution during heat treatments. Site specific samples can be extracted using a focused ion beam (FIB) system to pinpoint exact areas and phases of interest and compare different alloy systems [10].
Fig. 1 compares reconstructions of the L21/DO3 microstructure of Fe–25.9Al–1.6Ta (in at.%) to Fe–24.4Al–2Nb–0.03B, showing unprecedented details of the fine rectangular arrays of precipitates that formed during annealing at 700 °C. Though it is known that Heusler phases of the type Fe2AlX may have extended homogeneity ranges to leaner compositions of X than the stoichiometric 25 at.% X, the current results are quite surprising. When comparing the composition of these small precipitates, it becomes apparent that although the Al content is similar in the Heusler phase in both alloys and close to the stoichiometric value, the precipitates in the Fe–Al–Ta alloy are with about 19 at.% Ta closer to the stoichiometric composition compared to the Nb-lean precipitates, which only contain about 10 at.% Nb.
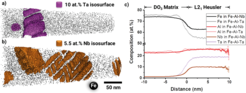
A time-temperature-transformation (TTT) diagram established from literature data and present work suggests that at a given temperature the metastable Heusler phase transforms more readily to the stable Laves phase in the Fe–Al–Nb system [7]. Before the APT investigations had been performed, it was inferred that the difference is due to the faster diffusion of Nb. The Heusler phase cannot transform directly into the Laves phase, but dissolves first in the Fe–Al matrix before nuclei of the Laves phase preferentially form on the grain boundaries [8].
The APT measurements now reveal that the difference between the Nb and Ta contents in the Heusler phase and the matrix is much larger in case of the Ta alloy, because the content of Nb or Ta in the Fe–Al matrix is 1.1 at.% in both alloys. Therefore, in addition to the slower diffusion kinetics it should also take more time for equilibrating the Ta-rich Heusler phase. Moreover, the precipitates in the Fe–Al–Ta alloy look more compact than the feathery appearance in the Fe–Al–Nb alloy (Fig. 1a, b). The latter results in a much larger surface area with the matrix, which could also contribute to a quicker dissolution. However, the current investigation gives no indication about coherency stresses between the precipitates and the matrix, which also have a stabilising effect for the metastable precipitates.
Further work will be carried out to gain insight on how the compositions of the Heusler phase vary with aging time and temperature, and what sort of compositional modulations contribute to the refinement of the subsequent Laves phase population. Knowledge on precipitate morphology and composition evolution will allow us to fine-tune the alloy chemistries and processing to achieve superior properties.
- Palm, M.; Stein, F.; Dehm; G.: Annu. Rev. Mater. Res. 49 (2019) 297.
- Palm, M.; Stein, F: Iron-Based Intermetallics, in Rana, R. (ed.) High-Performance Ferrous Alloys, Springer Nature Switzerland AG, Cham, Switzerland (2021) 423.
- Peng, J.; Moszner, F.; Rechmann, J.; Vogel, D.; Palm, M.; Rohwerder, M.: Corros. Sci., 149 (2019) 123.
- Zavašnik, J.; Peng, J.; Palm, M.; Corros. Sci.: 179 (2021) 109170.
- Moszner, F.; Peng, J.; Suutala, J.; Jasnau, U.; Damani, M.; Palm, M.: Metals, 2019 (2019) 847.
- Michalcová, A.; Senčekova, L.; Rolink, G.; Weisheit, A.; Pešička, J.; Stobik, M.; Palm, M.: Mater. Design 116 (2017) 481.
- Gedsun, A.; Stein, F.; Palm, M.: MRS Adv. 6 (2021) 176.
- Prokopčáková, P.; Švec, M.; Palm, M.: Int. J. Mater. Res.107 (2016) 396.
- Antonov, S.; Isheim, D.; Seidman, D.; Sun, E.; Helmink, R.; Tin, S.: Superalloys 2016, 13 (2016) 199.
- Antonov, S.; Isheim, D.; Seidman, D.; Tin, S.: Materialia 7 (2019) 100423.