How to avoid 3.5 billion tons of carbon dioxide per year
The team of the Max-Planck-Institut für Eisenforschung investigates a new route to produce green steel through hydrogen plasma
Germany, Europe and almost all countries in the world are heading towards climate neutral economies in the future. This aspect means to minimize as much CO2 emissions as possible plus compensating for the remaining emissions. However, this target is not yet met by current technology. One of the biggest industrial CO2 emitters, the iron- and steelmaking industry, still lacks the possibility of producing green steel and is till now, responsible for about 7% of all CO2 emissions worldwide. Facing these challenges, a team of the Max-Planck-Institut für Eisenforschung (MPIE) explores the possibility to use hydrogen plasma for the reduction of iron ore instead of using coke or reformed natural gas. The scientists published their latest findings in the journal Acta Materialia.
“Using pure hydrogen instead of coke or reformed natural gas to reduce iron ore can be one way to save CO2 emissions. However, the chemical reaction using pure hydrogen requires an external supply of energy to proceed. The use of hydrogen plasma instead, allows us to conduct the reduction reaction with less energy. Inside the plasma arc domain, H2 molecules collide among themselves and also with electrons, leading to the formation of high energy species (for example, ionized and atomized hydrogen). These species are accelerated towards the iron ore to be processed and partially release their energy at the reaction interface between oxide and plasma arc. This released energy serves as the energy needed for the reduction reaction. And that’s why using hydrogen plasma is favourable here.”, explains Dr. Isnaldi Souza, postdoctoral researcher at the MPIE and first author of the publication.
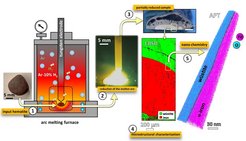
Using hydrogen plasma also allows the production of liquid iron ore in one single step melting and reducing the ores simultaneously with a less need for agglomeration or refining processes. “We investigated the nano-chemistry, interface structure and composition and phase transformation kinetics. Our results show that the hydrogen plasma reduction could take place in the established industrial electric furnaces without major modifications. Nevertheless, the effects of the hydrogen plasma on the electrode and refractory materials will be further evaluated.”, states Dr. Yan Ma, postdoctoral researcher in the same team with Souza and co-author of the publication.
The latest MPIE investigations show the thermodynamics and kinetics of the hydrogen plasma reduction of iron ores thus providing an alternative route for the production of green steel. In general, the MPIE established several groups dealing with the different aspects of sustainable metals. Souza and Ma are both working in the interdepartmental group “Physical Metallurgy of Sustainable Alloys”. Related groups are “Hydrogen in Materials”, “Hydrogen Mechanics and Interfaces”, “Computational Sustainable Metallurgy” and in cooperation with the RWTH Aachen University the group “Sustainable Materials Science and Technology”.
Author: Yasmin Ahmed Salem