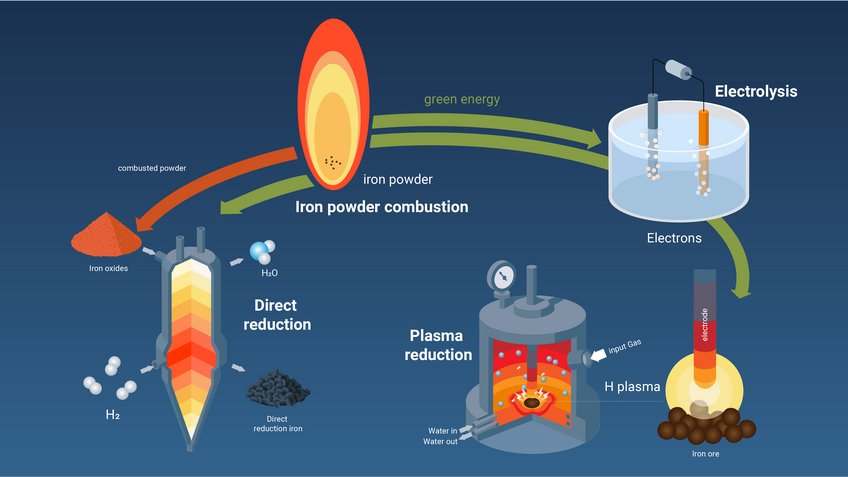
Sustainable Synthesis of Materials
This research group aims to increase the direct sustainability of structural and functional metals. The research topics cover reduced CO2-intensive primary production, low-energy metallurgical synthesis, metal recycling, scrap-compatible alloy design, green steel, sustainable semiconductors, improved longevity of alloys, and green energy generation via combustion of metal powders. The scientific focus lies in the study of the physical and chemical foundations for improving the direct sustainability of structural metals.
This group is concerned with sustainable materials and metallurgy, fields also referred to as green materials science and sustainable metallurgy. Engineering materials and particularly metallic alloys have enabled technological progress over millennia. Metallic materials have historic and enduring importance in our society. They have paved the path of human civilization with load-bearing and functional applications that can be used under the harshest environmental conditions, from the Bronze Age onwards. Only metallic materials encompass such diverse features as strength, hardness, workability, damage tolerance, joinability, ductility, and toughness, often combined with functional properties such as corrosion resistance, thermal and electric conductivity as well as hard and soft magnetism. The high and accelerating demand for load-bearing (structural) and functional metallic alloys in key sectors such as energy, construction, safety, and transportation is resulting in predicted production growth rates of up to 200% until 2050. Yet most of these metallic materials, specifically steel, aluminum, nickel, and titanium, but also semiconductors, require a lot of energy when extracted and manufactured and these processes emit large amounts of greenhouse gases and pollution. The huge success of metallic products and industries also means that they have an important role in addressing the current environmental crisis. The availability of metals (most of the elements used in structural alloys are among the most abundant), efficient mass producibility, low price, amenability to large-scale industrial production (from extraction to the metal alloy), and manufacturing (downstream operations after solidification) have become a substantial environmental burden: worldwide production of metals leads to the total energy consumption of about 53 exajoules (1 EJ = 1018 J) (8% of the global energy used) and almost 30% of industrial CO2-equivalent emissions (4.4 gigatons of CO2 equivalent) when counting only steels and aluminum alloys (the largest fraction of metal used by volume). This group studies the basic physical and chemical foundations for improving the direct sustainability of structural metals, in areas including reduced CO2 intensive primary production, low-energy metallurgical synthesis, recycling, scrap-compatible alloy design, improved alloy longevity, and green energy generation via combustion of metal powders. The group is also concerned with the effectiveness and technological readiness (TRL) of individual measures in Sustainable Metallurgy and works on novel materials that enable improved energy efficiency through their reduced mass, higher thermal stability, and better mechanical properties than currently available alloys.
The ongoing scientific activities of this group lie in the exploitation of green routes for iron production using different types of hydrogen carriers as reducing agents as well as via electrolysis. The hydrogen-based reduction approaches include solid-state direct reduction of iron ores exposed to molecular hydrogen and hydrogen plasma-based reduction of molten ores. Electrolysis of iron ores suspended (or dissolved) in liquid media is conducted at low temperatures (i.e. up to 200 °C) as an alternative to the aggressive high-temperature electrolysis of molten iron ores. The focus of such scientific studies is placed on the underlying mechanisms and associated phase transformations, microstructural evolutions, and chemical partitioning on both micro and nanoscopic scales that occur during the reduction of iron ores into iron. This group also investigates the impact of microstructural aspects of iron powder on their combustion for green energy generation.