Instrumentation development for ultra-high strain rate micromechanics
A fundamental understanding of the microscale deformation mechanisms during high speed impacts is vital for developing technologies for protection in demanding applications such as micrometeorite impact with spacecrafts, cold spray coating technology and microparticle impacts on aircraft turbines. Regardless, owing to lack of testing platforms, the majority of micromechanical testing focusses only on quasi-static testing. As such there is lack of experimental data on the behavior of microscale samples under short-time scales. This project will aim at addressing this specific knowledge gap, by the development of testing platforms capable of conducting quantitative micromechanical testing under extreme strain rates upto 10000/s and beyond. This will necessitate extensive hardware modifications to an in situ micromechanical testing system including the voltage supply, actuating mechanism, load-sensing system and support electrical systems for high-rate signal acquisition. Additionally, protocols and methods specific for such extreme micromechanical testing will be developed to address problems such as system resonances, inertia, wave propagation and low signal-to-noise ratio. This will allow for reliable and repeatable measurements under loading conditions never achieved before at the micron scale.
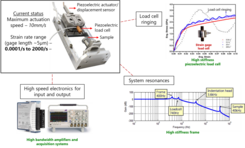
Instrumentation development for micromechanical testing at ultra-high strain rates