Sustainable, ultra-strong and ductile steel through advanced processing
International researcher team presents a novel microstructure design strategy for lean medium-manganese steels with optimized properties in the journal Science
A researcher team designed a new processing route for compositionally lean medium-manganese steels reaching tensile strength values of 2.2 GPa at an elongation of 20%, a so far unprecedented combination, exceeding the energy absorption capacity of current steels by a factor of 2.
Cars, buildings, infrastructures – all unimaginable without steels. While metallic materials have been known and manufactured since more than 5000 years, there is permanent need of further property improvement, especially as new processing opportunities emerge while at the same time sustainability concerns associated with alloying elements become more important. This shifts a few main constraints in the research focus: sustainability, strength and ductility, considering also costs and industrial applicability. A researcher team mainly from the Northeastern University (China) and the Max-Planck-Institut für Eisenforschung (MPIE, Germany) designed a new processing route for compositionally lean medium-manganese steels reaching tensile strength values of 2.2 GPa at an elongation of 20%, a so far unprecedented combination for a material with such a lean alloying content, exceeding the energy absorption capacity of current steels by a factor of 2. They published their latest results in the journal Science.
Processing leads to optimized microstructure
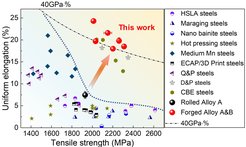
Steels – like all alloys - usually suffer from a trade-off between mechanical strength and ductility, which limits workability and damage tolerance. Commonly used maraging steels reach a strength of 2 GPa. However, they are less ductile and use expensive and non-sustainable alloying elements such as cobalt, nickel, molybdenum or titanium. Compared to maraging steels, deformed and partitioned steels reach similar strength, but can be elongated above 15%. However, their processing is complicated, thus costly, and their deformation is inhomogeneous. What all these ultra-high strength steels have in common is a dominant martensite microstructure that is not following any topological design nor shape criteria. This microstructure contributes to the alloy’s strength, but decreases its ductility and hence leads to embrittlement. “Our approach now consists of a microstructural design concept including multiple forging steps, a cryogenic treatment and tempering. This activates numerous micromechanisms that strengthen the material and make it more ductile”, explains Professor Dierk Raabe, director at Max-Planck-Institut für Eisenforschung and corresponding author of the publication. The new processing route transforms most of the austenite into martensite and stabilizes the remaining austenite. Moreover, the formed martensite is laminated and twofold topologically aligned. “The laminated microstructure reminds of a typical Damascus steel, which gains strength through folding and combining different iron alloys. Here, we don’t combine different alloys, but use a similar hierarchical microstructure order”, says Raabe.
The researchers used advanced transmission and scanning electron microscopy, and atom probe tomography to characterize the material and see the influence of each processing step. Forging for example leads to a higher density of dislocations and more highly dispersed nanoprecipitates, which result in a higher yield strength. The high ductility is an effect of dislocation slip in the martensite and gradual deformation- stimulated phase transformations.
New design route applicable in standard industrial manufacturing
The developed design route is compatible with existing industry processes, which makes it simple and efficient in upscaling. The researchers are now aiming to further adjust the alloy composition and adjust the design route for other martensitic alloy classes with the aim of combining high strength and ductility.
Author: Yasmin Ahmed Salem