Laser powder bed fusion based CuCrZr alloy lattices: fabrication and characterization
Within this project, we will use an infra-red laser beam source based selective powder melting to fabricate copper alloy (CuCrZr) architectures. The focus will be on identifying the process parameter-microstructure-mechanical property relationships in 3-dimensional CuCrZr alloy lattice architectures, under both quasi-static and dynamic loading conditions.
Additive manufacturing is changing the industry with freedom of design, fast prototyping, and waste minimization. For metals, the laser powder bed fusion (LPBF) in which raw powder material is melted by focused laser beam and solidification, is one of the promising techniques among a variety of additive manufacturing processes. Through intensive studies, it has been demonstrated that various metals and alloys with dense microstructure can be fabricated through LPBF. Current research is focused not only on the microstructure of the LPBFed metal but also on the complex geometries that can give functionality to the printed structures.
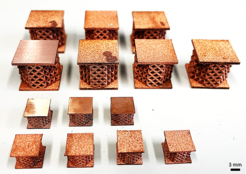
CuCrZr alloys possess a unique combination of high thermal/electrical conductivity and high strength. Pure Cu structures are unfortunately difficult to fabricate using infra-red laser based LPBF processes owing to the laser reflection. But thanks to the alloying elements, CuCrZr alloy can be successfully fabricated using the infra-red laser based LPBF process. 3-dimensional periodic structures such as lattices realized by the LPBF process can give new functionality to the CuCrZr alloys such as energy absorption. Specifically, in this project, we will fabricate CuCrZr alloy lattice structures through the LPBF process with the infra-red laser. By varying the fabrication process parameters, we plan to investigate the process parameter-microstructure relationships in LPBFed CuCrZr alloy lattice structures. Subsequently, the mechanical performance of the lattices will be evaluated by conducting compression tests under both quasi-static (upto a strain rate of 1/s) and dynamic loading conditions (upto a strain rate of 1000/s).