Design of tough metallic glasses
The promising mechanical properties of metallic glasses (MG) such as high hardness, yield strength, and toughness [1] are desirable to exploit for structural applications. Monolithic MGs lack grains and grain boundaries; thus, the mechanical properties of MGs are depending on the chemistry as well as processing and testing conditions. However, despite the promising properties, catastrophic failure is often observed, especially under uniaxial tension.
While most investigations on the mechanical properties of MGs have focussed on the topology of the atomic motifs, attention must also be placed on the nature of the local chemical bonding, which is the basis of atomic cohesion and hence mechanical properties [2]. However, while elastic properties can be directly calculated from ab initio calculations, mechanical properties such as fracture toughness, which involves the rearrangement of atoms, need new predictors and their validation [2]. Here, we present a predictor for the fracture toughness of MGs based on the electronic structure.
The brittle to tough transition cannot be universally predicted based on the Poisson’s ratio [2]. Instead, based on a comparison of the ab initio electronic structure and the fracture toughness of Cu70Zr30 and Pd57Al24Y8Cu11, we hypothesize that the fraction of hybridized bonds with respect to the overall bonds is a qualitative fingerprint of fracture toughness [3]: The lower the fraction of hybridized bonds, the higher the fracture toughness. Hence, the fraction of metallic bonds needs to be maximized to enhance fracture toughness [4]. Since the fraction of hybridized bonds can be obtained from ab initio calculations by calculating the crystal orbital overlap population (COOP) [5], the predictor for fracture toughness focuses on minimizing the COOP. For purely metallic bonding the electrons at the Fermi level Ef are delocalized. Hence, for an ideal MG in terms of toughness, COOP(Ef) = 0 [2, 4].
The experimental fracture toughness of MG scales with the COOP(Ef) (Fig. 1) [4]. Based on the fit of the data, the unknown fracture toughness of a Pd57Al24Y8Ni11 can be predicted to be 95 ± 20 MPa m0.5 [4]. However, as indicated by the negative COOP(Ef) in Fig. 1a, not only the fraction of hybridized bonds is crucial, but also the anti-bonding bonding character at Ef, which leads to a higher energy in the system and promotes bond separation [4].
![Fig. 1: (a) Fracture toughness of five different MGs as a function of crystal orbital overlap population (COOP) at the Fermi level Ef. The red solid line is a linear fit of the data points. The dashed blue line indicates the COOP(Ef) of Pd57Al24Y8Ni11 and the dotted blue line indicates the predicted fracture toughness. (b) In-lens-SE micrograph of the notch region of a micro-cantilever after micro-bending to 4 µm deflection. Severe shear band formation is observed around the notch as well as on the compressive side of the cantilever (see arrows) [4].](/4694738/original-1643028154.jpg?t=eyJ3aWR0aCI6MjQ2LCJvYmpfaWQiOjQ2OTQ3Mzh9--cd20f7b73c3fc25cf18561bda5bb2f176ee29b0f)
To critically appraise this new predictor for the fracture toughness of MGs, micro-mechanical bending tests on magnetron sputtered Pd58Al25Y5Ni12 thin films were performed. In these experiments, the cantilevers showed formation of multiple shear bands confined by the stress gradient (Fig. 1b), with no crack extension [4]. Hence, the fracture toughness exceeds the boundaries of micromechanical fracture experiments, which is consistent with the high toughness predicted for this material [4]. However, despite the large plasticity observed here in a complex stress state and with a small size, strain localization in uniaxial tension can still lead to catastrophic failure by strain localization.
Glass-matrix composite materials can prevent strain localization by exploiting plasticity of MGs for spatially confined geometries. By combining MGs with e.g. nanocrystalline high-entropy alloys (HEAs), ductile materials with near-theoretical strength can be obtained [6].
By doping a magnetron sputtered Cr-Fe-Co-Ni HEA with the glass-forming elements B and Si, a nanocomposite structure composed of a ~1 nm-thick amorphous phase surrounding the 8 nm-thick crystalline HEA columnar grains was formed [6]. In micro-mechanical compression tests, the crystal-glass composite exhibits a yield strength of 4.1 GPa (Fig. 2), which is higher than that of the nanocrystalline reference alloy with a similar composition. Moreover, the crystal-glass high-entropy nanocomposite reveals homogeneous plastic deformation without formation of visible shear bands (Fig. 2) [6].
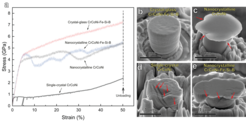
During plastic deformation of the crystal-glass nanocomposite, the nanograins are gradually subdivided, creating additional interfaces against dislocation motion [6]. The formation of additional interfaces compensates the work softening from de-twinning. Stress-concentrations by dislocation pile-ups at the grain boundaries are prevented by the absorption of dislocations in the amorphous phase. The interplay of continuous partial dislocation formation, movement, and annihilation promotes the homogeneous and compatible plastic deformation of the crystal-glass composite [6].
In conclusion, the here introduced predictor for fracture toughness based on the electronic structure obtained by ab initio calculations enables the identification of MG compositions with promising fracture toughness in silico. This offers a resource- and time-efficient navigation through the vast composition space of MGs. Combining the beneficial properties - high yield strength and toughness – with the high ductility of crystals, a new material class called crystal-glass high-entropy nanocomposite was developed. It reveals enhanced yield strength and ductility compared to the fully crystalline reference alloys. With both the prediction of fracture toughness and tuneable yield strength in these crystal-glass composites, a toolbox for tailoring mechanical properties of crystal-glass HEA composites has become available.
References
- Ashby, M.; Greer, A. L.: Scr. Mater. 54 (2006) 321.
- Evertz, S.; Schnabel, V.; Köhler, M.; Kirchlechner, I.; Kontis, P.; Chen, Y.-T.; Soler, R.; Nagamani Jaya, B.; Kirchlechner, C.; Music, D.; Gault, B.; Schneider, J. M.; Raabe, D.; Dehm, G.: Front. Mater. 7 (2020) 89.
- Schnabel, V.; Nagamani Jaya, B.; Köhler, M.; Music, D.; Kirchlechner, C., Dehm, G.; Raabe, D.; Schneider, J. M.: Sci. Rep. 6 (2016) 36556.
- Evertz, S.; Kirchlechner, I.; Soler, R.; Kirchlechner; C.; Kontis, P.; Bednarcik, J.; Gault, B.; Dehm, G.; Raabe, D.; Schneider, J. M.: Mater. Des. 186 (2020) 108327.
- Hoffmann, R.: Angew. Chem. Int. Edit. 26 (1987) 846.
- Wu, G.; Balachandran, S.; Gault, B.; Xia, W.; Liu, C.; Rao, Z.; Wei, Y.; Liu, S.; Lu, J.; Herbig, M.; Lu, W.; Dehm, G.; Li, Z.; Raabe, D.: Adv. Mater. 32 (2020) 202619.