Green Steel: The role of microstructure in Direct Reduction of Ores with Hydrogen
Direct reduction of iron ores with hydrogen is an attractive alternative to the common reduction with carbon, to eliminate the CO2 emissions in steel making. The kinetics of this process are not yet well understood, in particular during the wüstite reduction step. Microstructure, local chemistry and lattice defects are studied for better understanding the underlaying microscopic transport and reduction mechanisms and kinetics, aiming to open the perspective for a carbon-neutral iron production.
In this project we study the foundations of making green steel. Steel is the most important material class in terms of volume and environmental impact. While it is a sustainability enabler, for instance through lightweight design, magnetic devices, and efficient turbines, its primary production is not. Iron is reduced from its ores by using carbon as a reductant, causing 30% of the global CO2 emissions in the manufacturing sector, qualifying primary steel making it as the largest single industrial greenhouse gas emission source. Hydrogen is therefore attractive as alternative reductant. In this project we therefore study some of the basics of this reduction method. Although this reaction has been studied for decades, its kinetics is not well understood, particularly during the wüstite reduction step which is much slower than hematite reduction. Some rate-limiting factors of this reaction are determined by the microstructure and local chemistry of the ores. Here, we report on a multi-scale structure and composition analysis of iron reduced from hematite with pure H2, reaching down to near-atomic scale. During reduction a complex pore- and microstructure evolves, due to oxygen loss and non-volume conserving phase transformations. The microstructure after reduction is an aggregate of nearly pure iron crystals, containing inherited and acquired pores and cracks. We observe several types of lattice defects that accelerate mass transport as well as several chemical impurities (Na, Mg, Ti, V) within the Fe in the form of oxide islands that were not reduced. With this study, we aim to open the perspective in the field of carbon-neutral iron production from macroscopic processing towards better understanding of the underlying microscopic transport and reduction mechanisms and kinetics.
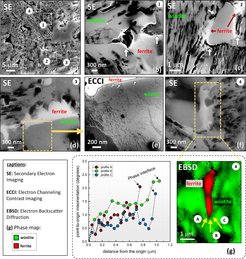
Figure: The role of microstructure in green steel making: Direct reduction of hematite iron ores with hydrogen at 700°C.
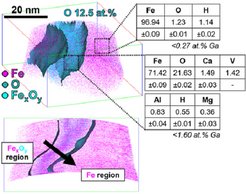
Figure: Atom probe tomography analysis in green steel making: Direct reduction of hematite iron ores with hydrogen at 700°C.