Steels for additive manufacturing
A wide range of steels is nowadays used in Additive Manufacturing (AM). The different matrix microstructure components and phases such as austenite, ferrite, and martensite as well as the various precipitation phases such as intermetallic precipitates and carbides generally equip steels with a huge variability in microstructure and properties.
Why is it worth to study steels in additive manufacturing? The answer relates to the specific features both, of the process and of the complex thermodynamcis and kinetics of steels:
A wide range of steels is nowadays used in Additive Manufacturing (AM). The different matrix microstructure components and phases such as austenite, ferrite, and martensite as well as the various precipitation phases such as intermetallic precipitates and carbides generally equip steels with a huge variability in microstructure and properties.
These features are influenced substantially through the specific boundary conditions associated with the AM processing, particularly regarding change in segregation behaviour, the rapid cooling and the repeated heating experienced by the subsequent layer build-up. Hence, any targetted design of steels suited for AM must involve the effects of these process parameters on the resulting microstructure, precipitation and transformation response and thus the properties.
The interplay of process parameters such as cooling and reheating and the resultant microstructure applies for both, AM-produced steels just as for conventionally-produced steels.
However, steels are subjected during AM processing to time-temperature profiles which are very different from the ones encountered in conventional process routes, and hence the resulting microstructures differ strongly as well. This includes a very fine and highly morphologically and crystallographically textured microstructure as a result of high solidification rates as well as non-equilibrium phases in the as-processed state. Such a microstructure, in turn, necessitates additional or adapted post-AM heat treatments and alloy design adjustments. In our projects, we study the different kinds of steels in use in fusion-based AM processes and present their microstructures, their mechanical and corrosion properties, their heat treatments and their intended applications.
This includes austenitic, duplex, martensitic and precipitation-hardening stainless steels, TRIP/TWIP steels, maraging and carbon-bearing tool steels and ODS steels.
From this research we are capable of identifying areas with missing information in the literature and assess which properties of AM steels exceed those of conventionally-produced ones, or, conversely, which properties fall behind. We close our review with a short summary of iron-base alloys with functional properties and their application perspectives in Additive Manufacturing.
Steels are the suited material choice in additive manufacturing and 3D printing for applications where the following requirements are requested:
High elastic stiffness
Corrosion resistance and general longevity under harsh environmental conditions
Strength, ductility, hardness, toughness and wear resistance
Low price and wide abundance
Unrivalled variety of achievable microstructure features ranging
from ultra-hard martensite to compliant multiphase compounds,
and/or
Functionalities such as ferromagnetism or invar effects.
The requirement of a good resistance to environmentally harsh conditions calls for stainless steels. Consequently, these steels, in particular AISI 316L/1.4404, are used in a large variety of applications where the parts to be fabricated are expected to come into contact with corrosive media at moderate temperatures during service. Where an overlap of corrosion resistance and increased mechanical strength and hardness (compared to austenitic stainless steels) is required, maraging-type precipitation-hardened martensitic stainless steel grades are often used (so called PH steel grades such as 17-4PH/1.4542 and 15-5PH/ 1.4545). This is e.g. the case in marine, power-plant and injection moulding industries.
Good yield strength, high hardness and abrasion resistance are required in the tool and die making industry, calling for tool steels. The key advantage of AM in this application is the ability to manufacture many separate, smoothly curved cooling channels close to the surface contour of e.g. injection moulding tools, leading to an efficient heat removal and thus an increased productivity and/or lifetime of the tool. The tool steels most used in conventional toolmaking processes contain a significant amount of carbon and are not easy to process, as will be described later, and thus the most popular choice of tool steel in AM processing today are the carbon-free maraging steels, in particular 18Ni-300/1.2709.
The comparably moderate price of stainless steels and their good processability also leads to austenitic stainless steels often being considered a good material for users new to AM.
Besides these main groups of steels, there is a number of other, less studied alloys in use in AM. They include for example martensitic stainless steels, duplex stainless steels, TRIP/TWIP steels and oxide-dispersion strengthened (ODS) steels. Functional application fields for steels such as custom shaped parts for electro-magnetic or invar applications require the use of Fe–Si, Fe–Ni or Fe–Co alloys.
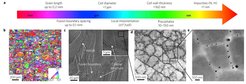
Microstructural features of an L-PBF produced 316L austenitic stainless steel at different length scales. a) Schematic showing the various length scales of the microstructural features observed. b) EBSD inverse pole figure mapping showing the grain orientations. C) SEM image of the cross section showing high-angle grain boundaries (HAGB), fusion boundaries (delineating melt pools), and the cellular solidification structure. d) Bright field TEM image of the cellular structure showing dislocation networks in the cell boundaries. e) high-angle annular dark-field (HAADF) scanning TEM (STEM) image of the solidification cells showing oxide particles.
EBSD inverse pole figure mapping showing the grain orientations. C) SEM image of the cross section showing high-angle grain boundaries (HAGB), fusion boundaries (delineating melt pools), and the cellular solidification structure. d) Bright field TEM image of the cellular structure showing dislocation networks in the cell boundaries. e) high-angle annular dark-field (HAADF) scanning TEM (STEM) image of the solidification cells showing oxide particles.