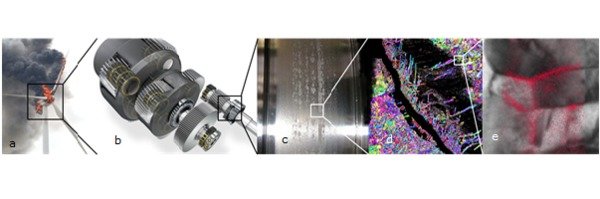
White Etching Crack Formation in bearings
The unpredictable failure mechanism of White Etching Crack (WEC) formation in bearing steels urgently demands in-depth understanding of the underlying mechanisms in the microstructure. The first breakthrough was achieved by relating the formation of White Etching Areas (WEAs) to successive WEC movement.
White Etching Crack formation causes severe microstructure decay during rolling contact fatigue of bearings which drastically reduces their expected service lifetime. Starting from non-metallic inclusions crack networks develop below the raceway which eventually reach the raceway surface and lead to catastrophic failure by spalling. On the micro scale, significant microstructure alteration is observed in direct vicinity of the WEC - the formation of nano-crystalline White Etching Areas (WEAs).
In this project, we contribute to the understanding of premature WEC failure by following two strategies: (i) First, we investigate actual failure cases from industrial applications and focus our analysis on a failed gear box bearing from a wind power plant field. This is beneficial as the complex loading conditions in such gear boxes hinder any direct in-situ analysis and make lab-scale experiments challenging. (ii) Second, we tailor our experimental approach towards advanced high resolution probes such as ECCI, EBSD, EDX and APT which are applied in a correlative manner. This is necessary because WEC formation involves nano-scale mechanisms such as carbide dissolution, thermomechanical mixing, nano-recrystallization and carbon segregation.
Recently, we achieved a breakthrough from our post-mortem microstructure analysis by formulating a new consistent WEA formation mechanism [1]. During cyclic loading WECs do not only move forward in terms of conventional crack propagation but also move normal to their crack plane. The white etching crack continuously changes its position and leaves behind a severely plastically deformed area consisting of ferritic nano-grains, i.e. the WEAs. The atomic-scale delocalization of the crack plane in a single loading cycle adds up to micron-sized WEAs during repetitive loading and unloading. Crack face rubbing and partial fusion of crack faces cause the WEC to open at a slightly shifted position with respect to the prior crack location after each loading cycle.
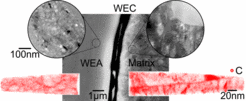
Fig.: Multi-scale ECCI+APT characterization of WECs in 100Cr6 bearing steel.