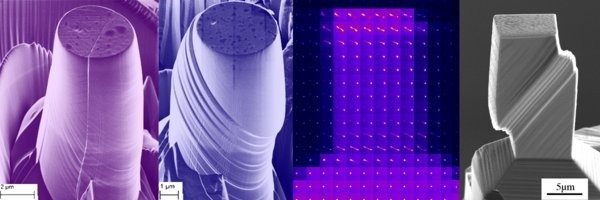
High temperature fracture toughness of interfaces of material systems
Nano- and Micromechanical experiments are nowadays widely explored to investigate site specific mechanical properties of materials and material systems which were not previously accessible in bulk dimensions [1]. Currently, the testing protocols for materials at non-ambient conditions, like high temperature or chemical non-inert atmospheres, are developed worldwide for micro/nanoscale testing (e.g. [2-4]).
During the past three years we have established a novel high temperature deformation rig allowing for micromechanical experiments at temperatures surpassing 600°C have been developed in the Structure and Nano-/ Micromechanics of Materials Department (Surmat project Viswanadh Gowtham Arigela).
Within this work we want to further the field of in situ micromechanics for materials and material systems relevant for energy applications by enabling high temperature (HT) fracture mechanics on single interfaces. For this purpose we will adopt the HT testing rig of Arigela et al. [5] to allow for testing single material interfaces. Subsequently, we will shape micron sized samples consisting of two phase materials so that a phase boundary is part of a micro specimen (see Fig. 1). Finally, we will artificially notch the samples by focused ion beam milling and fracture the samples at HT.
The aim of the project is develop different smart sample geometries to adequately measure the temperature dependent mode I and mode II fracture toughness of different interfaces of material systems.
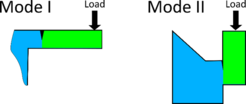
Fig. 1 Schematic of the interface fracture toughness geometries proposed for measuring mode I and mode II HT fracture toughness.