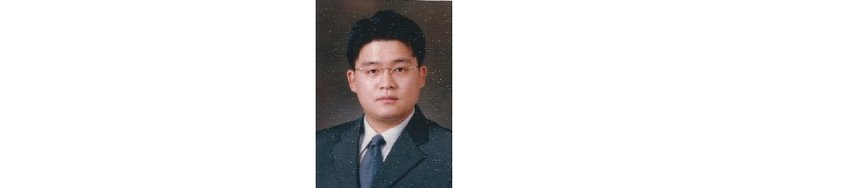
ECO-Al approach and ECO-Almag alloys
Al alloys: There are 2 principle groups of Al alloys - casting alloys with a three-digit identification number and wrought alloys with a four-digit number. The typical alloying elements are Si, Cu, Zn, Mn, and Mg and all Al alloys except pure Al have Mg as a first or second main alloying element. Major casting Al alloys are 3xx series (356, 383, etc.) which mainly utilize Si and Mg in terms of castability and Mg2Si precipitation hardening while wrought Al alloys contain Mg such as Cu (+ Mg) for 2xxx, Mg for 5xxx, Si + Mg for 6xxx, and Zn + Mg for 7xxx series. However, Mg is easily oxidized even at low levels in Al alloys due to so-called break-away oxidation therefore casting Al alloys are generally designed with 0.3wt% Mg and wrought ones have the practical limit of 5.5wt% Mg.
ECO-Al approach: The ECO-Al approach is so simple. ECO-Al alloys can be produced by alloying Mg + Al2Ca instead of Mg as an alloying element for Al alloys. Without Be addition and under ambient atmosphere through conventional processes, the addition of Mg + Al2Ca can give us controlled oxidation during meting and holding, minimized fluidity drop during casting, and controlled surface oxide layer. One thing to be made clear is that ECO-Al approach can be applied to all types of Al alloys except 1xx and 1xxx Al series. The best scenario of ECO-Al approach for conventional Al alloys is to improve 10-20% strength and maintain elongation level by maximizing Mg content in given range or alloy little more Mg over the range.
ECO-Almag alloys: Unlike Si, Cu, and Zn which have the content limits over which strength values no longer improve but currently are being used over the limits to get precipitation hardening, Mg can increase proportionally strength up to 17.2wt% by solid solution strengthening and work hardening but has the practical limit of 5.5wt%. As explained in ECO-Al approach, Mg + Al2Ca compound alloying can give us Al-(6-15)Mg-X alloys without Be and under ambient atmosphere through conventional processes and result in very high strength (VHS) over 600 MPa yield strength (the top value of conventional Al alloys is less than 550 MPa) or very high ductility (VHD) over 30 % elongation (the typical values of conventional Al alloys are 5-15% after heat treatment while 15-25 % in solutionized T4 condition and annealed O temper). The lighter density and higher strength or high ductility would give a novel value proposition through life-cycle to aerospace and automotive industry, respectively.
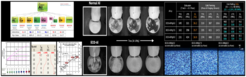
Professor Shae K. Kim
156, Gaetbeol-ro, Yeonsu-gu
Incheon 21999
Rep of Korea
Phone | Cellular (Canada) 1 438 503 9522 |
(Korea) 82 10 3735 9522 | |
Prof. S. K. Kim | |
Prof. S. K. Kim | |
Http | KITECH (English) |
UST (English) | |
ECO-Mg and ECO-Al |