
Precipitation kinetics during non-linear heat treatment in Laser Additive Manufacturing
As the awareness for sustainable development is increasing, industries are actively looking to make their processes and products more environmentally friendly. This often involves reducing the amount of waste generated during manufacturing and optimizing component design for better efficiency. As the designs are becoming more and more complex, they are becoming limited by the capability of the existing manufacturing processes. Additive manufacturing (AM) can offer a solution to these problems. As the name suggests, it is fundamentally different from existing manufacturing processes based on metal removal or subtraction. In AM, parts are built from layer by layer fusion of raw material (eg. wire, powder etc.). Such layer by layer application of heat results in a time-temperature profile which is fundamentally different from any of the contemporary heat treatments. Previous work in the group has established that this unique thermal profile can be exploited for microstructural modifications (eg. clustering, precipitation) during manufacturing. The aim of this work is to develop a fundamental understanding of such a strongly non-linear, peak-like thermal history on the precipitation kinetics. This understanding can then be used to develop alloys that exploit this intrinsic heat treatment to attain the desired final properties.
To study the precipitation kinetics during the intrinsic heat treatment, a CALPHAD-based simulation approach will be taken in this work. In the first stage, a model alloy will be selected based on previous work in the group and initial simulations using TC Prisma precipitation module in ThermoCalc. Then, in-situ (eg. Differential Scanning Calorimetry) and ex-situ (ex. Atom Probe Tomography) measurements will be performed using linear time-temperature profile heat treatments to capture the precipitation kinetics for simple time-temperature profiles. A kinetic model will be established by fitting unknown input parameters using the experimental results.
Next, this model will be applied to non-linear thermal profiles as experienced during AM to predict precipitation from intrinsic heat treatment during the process. The results will be compared to and validated by ex-situ measurements. Finally, the model will be used to study the effect of thermal and chemical inhomogeneity introduced in the material during the AM process on the precipitation kinetics.
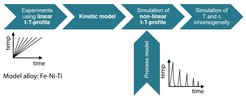