Max Planck materials scientist wins Starting Grant of European Research Council
Dr. Rajaprakash Ramachandramoorthy will explore ways to produce more reliable microelectronics via additive micromanufacturing
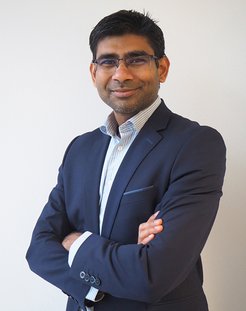
Notebooks, smartphones and many other electronic devices rely on microelectromechanical systems (MEMS). Their reliability and lifetime are influenced by drops, vibration and their surroundings. However, till now it is not possible to perform mechanical reliability tests under realistic conditions. Moreover, the design and choice of materials of these MEMS, which are key for the functionality of our electronics, are limited due to the way they are manufactured. Aiming to address these challenges, the European Research Council (ERC) now awarded Dr. Rajaprakash Ramachandramoorthy with a starting grant of 1.5 million euros for five years. The leader of the groups “Extreme Nanomechanics” and “Additive Manufacturing” at the Max-Planck-Institut für Eisenforschung (MPIE) aims to explore a way to fabricate and test 3D metal microarchitectures with envisioned applications in MEMS through additive micromanufacturing. This new fabrication technique will circumvent the current manufacturing limits.
Localized electrodeposition enables broader design spectrum
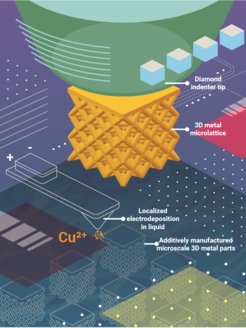
“I’m super happy, grateful and proud that the ERC selected my project for funding. The grant enables me to further pursue my research and is also an important step in my career”, says Ramachandramoorthy. Currently used microelectronics in mobile phones, laptops and other electronic devices are all fabricated with the help of UV lithography. This method is stable and easily upscaled to industrial needs. However, it is limited in terms of design opportunities and choice of materials as it is only usable with silicon and a few metals. “In my project, I will use additive micromanufacturing to print 3D metallic architectures with micron and nanoscale resolution. This fabrication method will enlarge the design freedom for microelectronic applications, among others. Moreover, the fabrication is based on localized electrodeposition, making it highly versatile and enables printing with a variety of different metals such as copper, gold, cobalt, nickel, silver”, adds Ramachandramoorthy. Localized electrodeposition in liquid uses an electrochemical salt solution that flows through a small nanoscale orifice containing metal ions, which get reduced at the working electrode to form the microscale metal droplet. Using nanometer precise piezo positioners droplet-by-droplet 3D metal micro-objects are fabricated.
Another big plus of the new approach is that liquids could be encapsulated in the metal microarchitectures, opening a new engineering design phase space. Such metal-liquid microarchitectures have interesting applications for example in drug delivery, temperature sensing, etc. Moreover, the printed microarchitectures could also be filled with liquids containing fluorescence markers, which flow out locally during impacts/deformations thus acting as damage sensors. Knowing where and when an electronic device is damaged, helps in finding ways to repair the device – one step towards sustainability.
Targeted application determines technique of choice
After fabricating the 3D microarchitectures with multimetals and metal-liquid micro-containers, Ramachandramoorthy and his team will further devise reliability protocols to characterize the micro/nanomechanical properties of such architectures under application relevant extreme speeds, penetrations and temperatures.
Cost-wise, UV lithography is very costly while setting up the technique, but becomes less expensive during the manufacturing of MEMS devices. Setting up the additive micromanufacturing process to be explored in this ERC project is less expensive and as soon as the process is parallelized, it gets even less costly. “I think in the future, a combination of both techniques is ideal. UV lithography will remain the method of choice when it comes to fabricating silicon based 2.5D microarchitectures. Whereas additive micromanufacturing becomes interesting whenever 3D microarchitectures with a wider choice of metals is needed or the incorporation of liquids is targeted”, explains Ramachandramoorthy.
Rajaprakash Ramachandramoorthy joined MPIE as group leader in August 2020. Before working here, he was a Marie-Curie postdoctoral fellow at the Swiss Federal Laboratories for Materials Science and Technology (Empa). Ramachandramoorthy did his PhD at Northwestern University (USA) in theoretical and applied mechanics. His research focuses on the mechanical behaviour of small-scale materials using mainly in situ scanning and transmission electron microscopy and microfabrication using additive techniques.
The grants of the European Research Council are regarded as one of the most prestigious international research grants. 2932 proposals were submitted Europe-wide in this application round whereby 408 scientists were successful.
Author: Yasmin Ahmed Salem