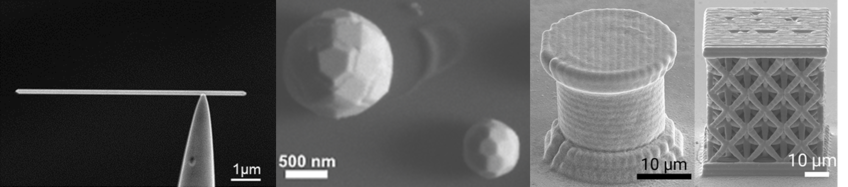
Nanomechanical Instrumentation and Extreme Nanomechanics – XNano
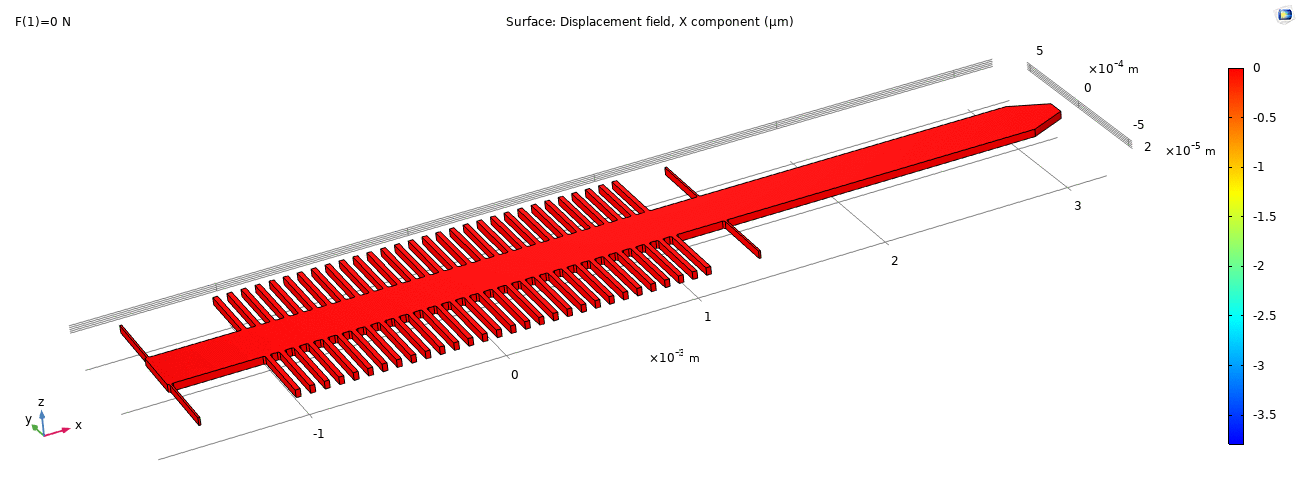
Relentless pursuit of miniaturization has resulted in micro and nanoscale materials being ubiquitous in a plethora of applications. Understanding the material behavior of such small-scale materials at high strain rates is critical for the design of these structures, which would be subjected to day-to-day mechanical and thermal overloads such as drops, impacts and vibrations. From a fundamental scientific perspective, experimental determination of high strain rate properties at the micro- and nano-scale will allow the bridging of time scales between simulations (molecular dynamics/discrete dislocation dynamics) and experiments, leading to a direct comparison between the two complementary research methods.
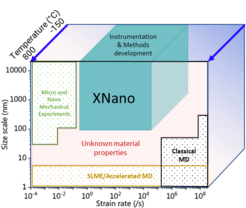
The research vision of “Nanomechanical instrumentation and extreme nanomechanics – XNano” group is to push the envelope of in situ SEM and TEM based micro-/nano- mechanical testing techniques towards application-relevant high strain rates and non-ambient temperatures. The primary research focus is on instrumentation development for in situ micro-to-meso scale multimodal (tension, compression and fatigue) mechanical investigations at strain rates between 0.001/s to 10000/s and temperatures between -160°C and 1000°C. Case studies using such customized instrumentation will help extract the structure(architecture)-microstructure-mechanical property relationships in small-scale metallic architectures (nanowires, micropillars, microparticles and microlattices) under extreme loading conditions. The second key area of research will be on the application and development of additive micromanufacturing methods for fabricating micro-to-meso scale metallic architectures. This will allow 3D printing of metals with sub-micron resolution and help achieve high-throughput fabrication of small-scale architectures with complex geometries.
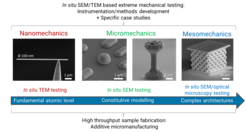
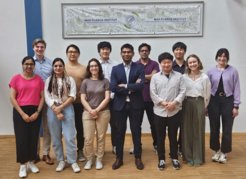
Back row from left to right: Hendrik Holz, Kuan Ding, Jeongin Paeng, Lalith Kumar Bhaskar, Jongbin Go