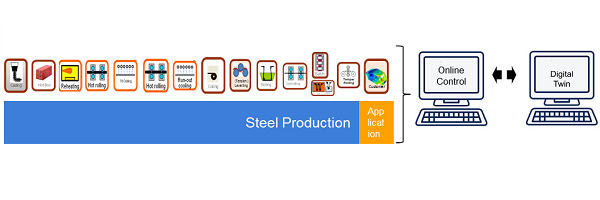
DENS - Digitally Enhanced New Steel Product Development
New product development in the steel industry nowadays requires faster development of the new alloys with increased complexity. Moreover, for these complex new steel grades, it is more challenging to control their properties during the process chain. This leads to more experimental testing, more plant trials and also higher rejections due to unmatched requirements. Therefore, the steel companies wish to have a sophisticated offline through process model to capture the microstructure and engineering property evolution during manufacturing.
The information from the sophisticated offline models needs to be translated into online process control models, which would enable the control of manufacturing processes to get the alloys with the right properties at the first time itself.
This has given rise to ‘Digitally Enhanced New Steel Product Development’ (DENS) programme at TATA Steel. The programme aims to have a through-process model to depict the evolution of process and engineering properties of new and existing alloys. This through-process model contains many sophisticated models that would strongly interact with each other. Thus, the scientific challenge of the programme is to connect all state-of-art sub models currently available into one through process modelling chain. It is envisioned that this modelling would be mature enough to shorten the time to market for new steel alloys without compromising on the production efficiency.
The whole programme is divided into 4 areas: (i) Engineering Properties (ii) Microstructure modelling (iii) Oxide Modelling (iv) Process modelling. In the case of microstructure modelling, the microstructure modelling during the deformation (hot and cold rolling) can be described through the use of the DAMASK framework.
There are two projects which have been linked to the use of DAMASK in the DENS framework: a) Multi-field RVE Simulations and b) Full-field Simulations of Dynamic Recrystallization.
Multi-Field RVE Simulations: This project focusses on combining the physical descriptions of important processes in microstructural evolution developed in other DENS projects into one multi-field crystal plasticity framework. This will be at the heart of the modelling framework for the processes involving deformation. Work-hardening [1], Phase transformations [2], recrystallization [3] and precipitation processes [4] have individual models to describe them. But, during manufacturing these processes tend to occur concurrently and tend to influence each other strongly. Therefore, a framework that allows solving of multi-field problems is required. One of the frameworks that allows solving of such multi-field problems is DAMASK [5], the multi-field crystal plasticity simulation toolkit developed at MPIE. This toolkit would be used as integration platform for different individual models developed.
Full-field Simulations of Dynamic Recrystallization: Till now the literature has numerous examples for simulation of Static Recrystallization. But, the simulations of Dynamic Recrystallization (DRX), which occurs during the high temperature deformation, have only been shown recently [6], [7]. Most of these simulations involve weak coupling with crystal plasticity [6] or small strain formulations [7]. But, this is not suited for process simulations. Therefore, modelling this phenomenon using DAMASK is an ideal starting point as it uses a finite strain formulation. This project involves development of better work-hardening models at high temperatures, developing a physically based nucleation criteria during DRX and modelling the growth of the DRX nuclei. This should help in predicting the nucleation sites in 3D microstructures and then describing the growth of these nuclei in a 3D environment. The project would also involve modifying the existing DAMASK framework to enable formation of new grains and strong coupling with growth models, which require efficient data storage and transfer between DAMASK and growth models. Based on the findings of the full-field model, an analytical model would be formulated for use in online process simulations.
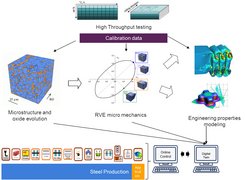