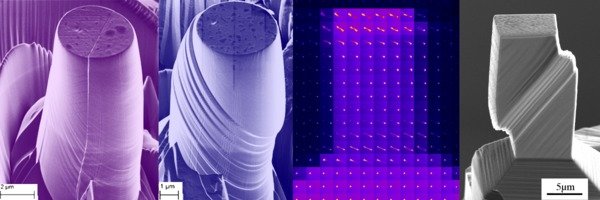
Nano- and micromechanics facilities
The largest share of small-scale samples at the MPIE is currently produced via a focused ion beam (FIB) based route, for which a Zeiss Auriga® Crossbeam system was installed in 2013. The FIB is operated with 5 keV to 30 keV Ga+ ions focused typically to a beam-size in the range of some nanometres. In contrast to standard FIBs, the attached nano patterning and visualisation engine (NPVE, Fibics Inc, Ottawa, Canada) gives full access to the beam control. Thus, complex shapes with varying geometries requiring different dwell times locally can easily be set and manufactured in an automised way. The NPVE helps us to surpass one of the bottle necks during micromechanical experiments: the manufacture of a statistically sound number of samples. Typical sample sizes produced via this route vary from several tens of nanometres up to 20 µm, which is in a size regime where a transition from a deterministic to a stochastic behaviour is observed, and therefore a high number of experiments is required.
On top of the dedicated sample manufacture, also testing rigs spanning over several orders of magnitude had been implemented in past years. Our instrumented nanoindentation systems are either able to operate at a synchrotron beamline without obstructing the X-ray beam, are operated inside a scanning electron microscope (SEM), or in the transmission electron microscope (TEM). Moreover, the capabilities of testing at high strain rates and from cryogenic temperatures to 800°C have recently been introduced. The variety of testable sample sizes ranges from some tens of nanometres over several tens of micrometre to almost 500 µm. The various new loading rigs provide significant overlap in maximum force and strain rate and complement the existing (macroscopic) straining rigs at the MPIE. Thus, we are now able to probe material responses from the low nanometre regime up to macroscopic sample and component dimensions, giving us the unique ability to understand material behaviour across the relevant length scales.
All of the newly installed machines are aimed for in situ operation – i.e. advanced characterisation tools as for instance the electron contrast channelling imaging (ECCI as pioneered in the MA department) or dedicated environmental loading conditions using a hydroelectric cell (in collaboration with the GO department) – and thus, are well suited for answering advanced questions in various material systems.
Along with the Asmec Unat II (shown in Fig. 1) the group also utilises the Hysitron PI-88 indenter system with low-load and high-temperature modules, and the Alemnis ASA system with high strain rate, low-temperature and high-temperature modules. These instrumented nanoindentation devices are used within a Zeiss Gemini® FEG-SEM or JEOL JSM 6490 SEM.
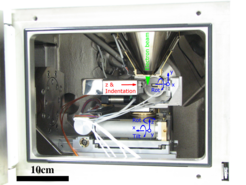