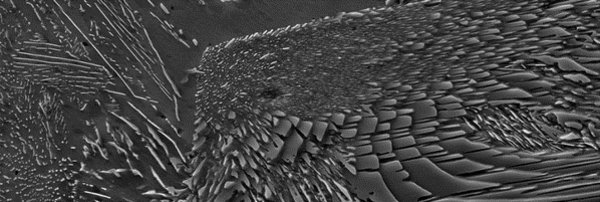
Combinatorial Metallurgy and Processing
The main focus of the group lies on the development of in-situ metal-matrix-composites with an improved mechanical and physical property profile, mainly a raised stiffness/density ratio. Fe-based composites, also termed high modulus steels (HMS), are especially attractive due the high inherent stiffness of the matrix, the multitude of equilibrium and non-equilibrium phase transformations and low alloy costs. Main challenges are the strongly decreased ductility by the incorporation of inherently stiff particles such as oxides, nitrides, borides or intermetallic compounds, as well as the complex synthesis of such hybrid materials. We aim at contributing to the following main topics in order to allow knowledge based alloy design: (i) theoretical and experimental identification of most suitable particles regarding property profile and production, (ii) elucidation and optimisation of the co-deformation processes of matrix, particles and their mutual interaction, and (iii) development of novel liquid metallurgy synthesis production techniques suitable for volume production of novel HMS.
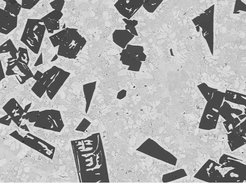
Another mission is to open innovative pathways for the compositional and thermo-mechanical high-throughput bulk combinatorial investigation of structural materials. Innovative methods for the accelerated synthesis, processing and testing of bulk metallic structural materials are developed and deployed, so that the associated basic metallurgical questions (e.g. alloy- and processing-sensitive changes in complex strain hardening phenomena) and corresponding engineering issues (such as texture evolution, sheet forming or joining behaviour) can be addressed more rapidly and efficiently. We refer to such methods as “Rapid Alloy Prototyping” (RAP). They allow to evaluate the mechanical properties of groups of alloys that are systematically varied in terms of the chemical compositions and the imposed thermo-mechanical treatments simultaneously and thus with a higher throughput than with conventional methods and step-by-step iterations of these parameters. Thus the time between a design idea and the final evaluation of the materials´ mechanical and microstructural properties is reduced from several weeks or even months down to hours.
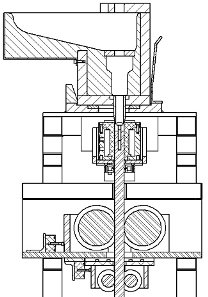
Furthermore we develop novel methods to locally control constitution, morphology, dispersion, and transformation behaviour of multiphase materials. The approach is based on the targeted, site-specific formation and confined dissolution of precipitated carbides or intermetallic phases. These dispersoids act as ‘vessels’ or ‘containers’ for specific alloying elements forming controlled chemical gradients within the microstructure upon precipitation and subsequent (partial) dissolution at elevated temperatures. The basic processing sequence consists of three subsequent steps, namely, (i) matrix homogenisation (conditioning step); (ii) nucleation and growth of the vessel phases (accumulation step); and (iii) (partial) vessel dissolution (dissolution step). The vessel phase method offers multiple pathways to create dispersed microstructures by variation of plain thermo-mechanical parameters such as time, temperature and deformation. This local microstructure design enables to optimise the mechanical property profiles of advanced structural materials such as high strength steels at comparatively lean alloy compositions.
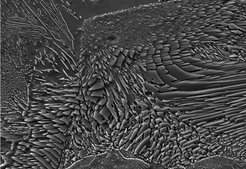
Another research field is concerned with the development of thermo-mechanically controlled synthesis for producing layered bulk samples built-up of the constituting phases of structural materials for the analysis of multiphase co-deformation phenomena. Following a thermo-mechanically controlled roll bonding procedure, the intrinsic properties of the microstructural components – down to the nanometric range – as well as their mutual mechanical interaction and interfacial phenomena can be systematically investigated in highly controlled model microstructures of reduced complexity. Special emphasis is laid on how the plasticity of martensite within a ferrite, as a key parameter required for understanding and optimising dual phase steels, can be investigated following the proposed approach. In this context, design of advanced blade and tool steels as well the analysis of the actual wear mechanisms is also undertaken.
Furthermore, we are concerned with fundamental research into the role of intermetallic phases in dissimilar joining of Al alloys to steel with the following objectives: (i) investigate the fundamental reactions governing the phase formation and evolution at the interface between Fe or steel and Al alloys; at temperatures below and above the melting point of Al. (ii) Study the role of alloying elements on build-up and growth of reaction layers in direct comparison to experiments with pure Al. (iii) Investigate the mechanisms how intermetallic reaction layers influence the mechanical properties of dissimilar joints between steel and Al alloys. We aim at providing engineers with guidelines to optimise joining and coating technology.
Within the service group “Metallurgy” a wide range of complex metallic materials is produced and processed for in-house co-operations as well as for external scientific and industrial partners. The spectrum of materials ranges from novel lightweight materials such as Gum-titanium or magnesium-based alloys with additions of rare-earth elements, intermetallic materials such as Laves phases to amorphous alloys such as bulk metallic glasses. The main expertise, however, lies on the synthesis and processing of innovative iron based materials, for example lightweight-construction steels containing high amounts of manganese, novel creep resistant steels for energy conversion applications or high-nitrogen alloyed austenitic and martensitic steels. To cover the wide spectrum of materials and requirements, a broad range of equipment is available.
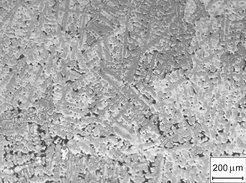