How does hydrogen pressure affect hydrogen-based direct reduction for sustainable ironmaking?
Hydrogen-based reduction (HyDR) of iron ores is a major step toward sustainable ironmaking, to mitigate the gigantic CO2 emissions in the current iron and steel industry (~8% of the global CO2 emissions). HyDR is a multistep solid-state reaction, where iron ores (hematite or magnetite) are gradually reduced to iron at high temperatures of 500-1100 °C. H2 reduces the iron oxides by removing the chemically bound oxygen in iron oxides to produce metallic iron (Fe). During HyDR, pores form due to the removal of oxygen and the formation of cracks. The formation of pores and their connectivity are critical for the overall reduction kinetics since they provide fresh surfaces for chemical reactions and transport pathways for gaseous reductant (H2) and product (H2O).
Direct reduction is a mature technology that produces fresh iron currently with steam-reformed natural gas and gasified coal as reductants. The commercial reduction technologies used today are usually operated at elevated pressures. For example, the MIDREX and HyL/Energiron processes, using iron ore pellets (10-16 mm in diameter), are operated at 2 bar and 6-8 bar total pressure, respectively. To facilitate the furnace design and process optimization of future HyDR, it is crucial to understand the effect of H2 gas pressure on reduction behavior, particularly, on the reduction kinetics and microstructure evolution of hematite pellets.
In this project, we investigated the reduction kinetics and microstructure formation during HyDR as a function of H2 pressure (at 1, 10, 50, and 100 bar) under both static (without H2 gas flow) and dynamic conditions (under H2 gas flow). Our results showed that the reduction kinetics of hematite pellets increases with an increase in H2 pressure, Figure a. Also, we found that the microstructure of iron is altered by H2 gas pressure. By characterizing the microstructure of the partially reduced samples, we observed the formation of dense iron at 1 bar (S1 bar) yet porous iron at 100 bar (S100 bar) under static conditions, Figure b. The morphology of pores in fully reduced iron changes notably with varying hydrogen gas pressures. Under dynamic gas conditions, the metallic iron forms large and elongated pores at 1 bar, whereas, at 50 bar, it exhibits a fine, random shape morphology, Figure c. The formation of ultrafine iron grains (1.0±0.8 μm) was observed in the pellet at 50 bar. This finding also inspires the fabrication of ultrafine porous microstructure via hydrogen-based direct reduction. Thus, the results offer new insights into the crucial role of H2 pressure in the HyDR process, guiding future furnace design and process optimization for sustainable ironmaking.
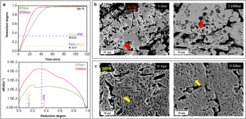