Chemical boundary engineering
Grain boundary engineering has been for long the most effective approach to tailor mechanical properties of metallic materials. There are limits to the fineness and types of microstructures achievable because of the low thermal stability of crystallographic boundaries, which leads to a rapid increase of grain size after exposure to thermal loads. Our unique chemical boundary engineering approach (CBE) enables us to create a material with an ultrafine hierarchically heterogeneous microstructure even after heating to high temperatures. For plain steels with a carbon content only up to 0.2 weight% ultimate strength levels over 2.0 GPa in combination with good ductility (>20%) can be achieved. The CBE design approach, shown here for plain carbon steels, can also be used for other alloys.
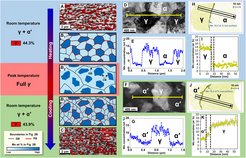
(A) EBSD image quality map with superposed phase color map of the face-centered cubic (FCC) phase (red region) of the ART-processed steel, showing the equiaxed microstructure of austenite (γ) with ferrite (α), and (C) the ultrafine dual phase microstructure of γ and martensite (α′) of the CBE-processed steel. (B) Sketch of the microstructural evolution of the steels during ultrafast heating and quenching via the CBE strategy to illustrate the role of GBs, PBs, and CBs. (D and E) TEM images with EDS analysis showing the microstructure and Mn concentration profile between γ and α of the ART-processed steel, while (F and G) is that between γ and α′ of the CBE-processed steel. Near-atomic level Mn distribution is revealed by 3D-APT, (H and I) between γ and α, and (J and K) between γ and α′.