Dual-nanoprecipitation enables ultrastrong lightweight compositionally complex nanosteels
We introduce here a new approach in which we strengthen a low-density solid solution matrix simultaneously by a dual-nanoprecipitation system containing both kappa-carbides and B2 particles. Since the conventional thermodynamic working point is not accessible to realize this dual-precipitation strategy, we designed a low-density (6.6 g/cm3) steel-type alloy, which uses merits of the recently introduced multi–principal element approach referred to as compositionally complex alloys (CCAs) or high-entropy alloys (HEAs).
The design of steels with high strength, toughness, and ductility combined with low mass density is an important task for saving energy and reducing emissions at maintained safety levels in multiple transportation applications. For example, reducing a vehicle’s weight translates linearly to a corresponding reduction in fuel consumption, with a rule of thumb value of 0.5 liters less fuel per 100 kg of weight reduction. Although other lightweight materials, e.g., Al-alloys, Mg-alloys, and carbon fiber composites, are available or under development, the unique combination of absolute strength, specific strength, ductility, toughness, and cost-effectiveness makes advanced lightweight Fe-based steels particularly attractive for future key engineering applications.
In this context, the Fe-Mn-Al-C system has gained much attention since the addition of Al into the Fe-Mn-C system is effective to achieve both up to ~10% weight reduction and improved strength and ductility compared to conventional steels. More specifically, Fe-Mn-Al-C steels with austenitic [face-centered cubic (FCC)] solid solution matrix and nanosized L'12 (ordered FCC) kappa-carbides reach a tensile strength of ~1190 MPa (specific tensile strength of 183 MPa·cm3 g−1) at an elongation of ~30% under tensile loading. However, the shearing of the coherent kappa-carbides at high stresses leads to local strain softening, which can cause strain localization.
Also, at grain boundaries, the Kappa-carbides become incoherent, promoting crack initiation, which leads to embrittlement, particularly at high Al and C contents (2). Thus, for further enhancing the mechanical properties, non-shearable incoherent B2 (ordered body-centered cubic) particles, instead of kappa-carbides, have been introduced into Fe-Mn-Al-C–based austenitic steels. The uniformly distributed hard B2 particles enable pronounced local strain hardening, since the dislocations must bow out and bypass them, leaving additional dislocation loops around the particles behind, an effect referred to as Orowan strengthening. This mechanism leads to very high specific strength values of up to 233 MPa·cm3 g−1 for an alloy (referred to as high–specific strength steels (HSSSs)) with 22 vol. % of B2 precipitates. Higher strength values require larger volume fractions of B2 particles, yet only at a significant expense of ductility, due to the intrinsically brittle nature of the B2 intermetallic compound.
Because of these limitations of the existing alloy design concepts, we introduce here a new approach in which we strengthen a low-density solid solution matrix simultaneously by a dual-nanoprecipitation system containing both kappa-carbides and B2 particles. Since the conventional thermodynamic working point is not accessible to realize this dual-precipitation strategy, we designed a low-density (6.6 g/cm3) steel-type alloy, which uses merits of the recently introduced multi–principal element approach referred to as compositionally complex alloys (CCAs) or high-entropy alloys (HEAs). More specifically, we propose here a new class of compositionally complex steels (CCSs) consisting of five principal elements including C in nonequiatomic ratios with Fe holding the highest atomic fraction [48 atomic % (at. %)], and each element has an atomic fraction of no less than 5 at. %.
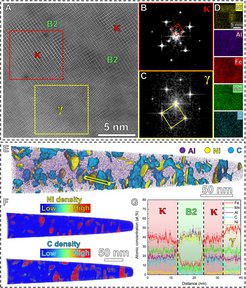