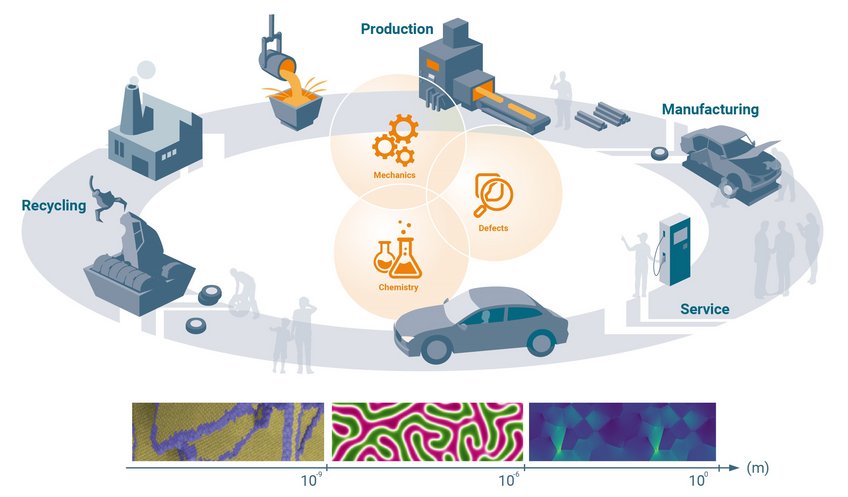
Computational Sustainable Metallurgy
The impact of humanity on the environment and climate has long been scientific fact. Acceptance of this fact in the non-scientific world has finally reached the point where many societies and governments have started to adopt policy and to implement measures geared toward reduction or even elimination of this impact. Prominent examples of this include the idea of a “climate-neutral” or “green” economy and production, or the idea of sustainability. An example of this is the on-going shift in many countries away from fossil fuels toward renewable and sustainable energy sources. A number of scientific and technological challenges remain in this and other areas such as material engineering, metallurgy, steel production, energy storage, battery technology, or recycling. Solving these outstanding scientific challenges requires proper understanding of the underlying mechanisms and casting them into interdisciplinary, multi-physics and multi-scale modeling approaches. Advances in the understanding of chemical reactions, chemo-mechanical interaction, mechanical behavior, defect evolution and material degradation, from atomistic scales up to continuum level, are required to resolve many of the most pressing challenges and achieve the goal of material sustainability. These cover every aspect of material life from extraction to production, processing, manufacturing, service life and recycling. This group focuses on applying and developing computational methods to solve various challenges related to materials and processes with important environmental impact, focusing on problems where the interplay of chemistry, phase transformation, microstructure, mechanics and damage plays an important role.
Note that 30% of the global CO2 emissions in the manufacturing sector is related to steel production, which translates to 6.5% of all CO2 emissions. Thus, direct hydrogen-based reduction of iron ore is considered as an alternative method of steel production with considerably lower emission compared to conventional carbon-based reduction. Modeling the reduction process by coupled chemo-mechanical phase-field methods including microstructure and defect evolution is an on-going research topic at this group. Close connection to underlying physics at atomistic scales as well as experimental observation are maintained in the projects in this group.
In sustainable manufacturing, waste reduction, lowering manufacturing steps, and component optimization are important topics in research. Advanced manufacturing methods such as additive manufacturing (AM) are promising in this regard. For example, tuning mechanical properties of highly adaptive composites and meta-materials using additive manufacturing methods will result in weight and waste reduction. Smart and adaptive optimization of the on-demand composite structure based on mechanical load requires accurate computational models capable of predicting hot spots of damage in highly anisotropic AM-based composites. Modeling such composites through combined phase-field and cohesive zone models calibrated against experiments are focus of this group.
Corrosion and damage evolution during life cycle of metals is one of the most important underlying reason of component failure. Topics such as hydrogen embrittlement, stress corrosion cracking, Li-ion battery degradation are important for clean energy storage (either hydrogen storage or electricity) and focus of projects in this group. Interplay of chemistry, mechanics, and damage development at different scales is again important in these topics.
Phase-field, finite element, molecular dynamics, Monte Carlo and machine learning methods are the computational approaches used in this group at various projects. Software packages such as the Düssseldorf Advanced Material Simulation Kit (DAMASK), MOOSE framework, LAMMPS and TensorFlow are among the tools employed in our group.