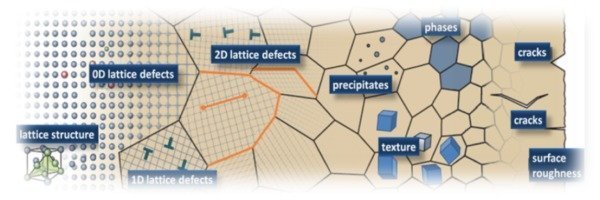
Multistage strain hardening through dislocation substructure and twinning in a high strength and ductile low-density Fe–Mn–Al–C steel
In this project we investigate the kinetics of the deformation structure evolution and its contribution to the strain hardening of a Fe–30.5Mn–2.1Al–1.2C (wt.%) steel during tensile deformation by means of transmission electron microscopy and electron channeling contrast imaging combined with electron backscatter diffraction.
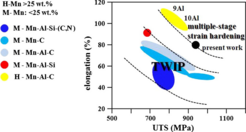
Ultimate tensile stress (MPa) vs. elongation chart for several high-Mn steel grades. M–Mn: steels with Mn content lower than 25 wt.% Mn; H–Mn: steels with Mn content higher than 25 wt.% Mn. TWIP: twinning-induced-plasticity effect. Chemical composition in wt.%.
The alloy exhibits a superior combination of strength and ductility (ultimate tensile strength of 1.6 GPa and elongation to failure of 55%) due to the multiple-stage strain hardening. We explain this behavior in terms of dislocation substructure refinement and subsequent activation of deformation twinning. The early hardening stage is fully determined by the size of the dislocation substructure, namely, Taylor lattices, cell blocks and dislocation cells. The high carbon content in solid solution has a pronounced effect on the evolving dislocation substructure. We attribute this effect to the reduction of the dislocation cross-slip frequency by solute carbon. With increasing applied stress, the cross-slip frequency increases. This results in a gradual transition from planar (Taylor lattices) to wavy (cells, cell blocks) dislocation configurations. The size of such dislocation substructures scales inversely with the applied resolved stress. We do not observe the so-called microband-induced plasticity effect. In the present case, due to texture effects, microbanding is not favored during tensile deformation and, hence, has no effect on strain hardening.