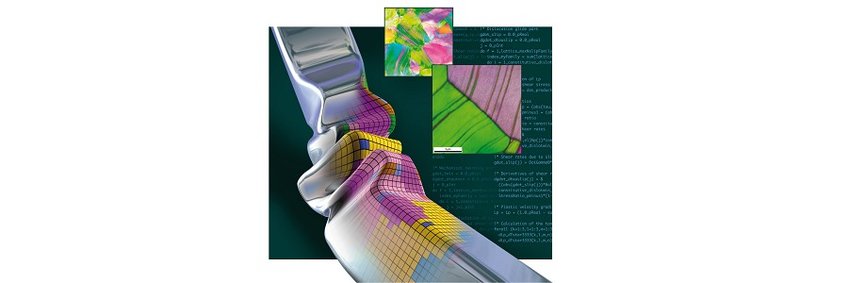
The Düsseldorf Advanced Material Simulation Kit: DAMASK
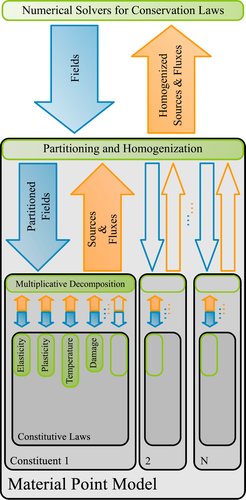
Figure 1: Hierarchy of scales as treated in DAMASK
Crystal plasticity modelling has matured into a cornerstone of computational materials science [1]. Developing this field from its original mean-field homogenization approach in conjunction with viscoplastic constitutive hardening rules into an advanced multiphysics continuum field solution strategy requires a long term initiative. The “Theory and Simulation” group is working in this field since 2000. Starting originally from Kalidindi’s numerical crystal plasticity integration scheme [2] user subroutines for the commercial FEM packages Abaqus and MSC.Marc were developed. The scientific focus of the group was, however, the development of advanced constitutive models based on dislocation densities as internal state variables, which are capable of providing microstructure based predictions [3]. As simulations of different material classes and on different length scales necessitate the use of constitutive descriptions of varying degree of sophistication, it soon turned out that the numerical implementation was not flexible enough to incorporate different constitutive models. Therefore, within the project “Computational Modelling of Polycrystals” (CMCn, the first joined MPG-FhG project ever, established in 2006) the development of a flexible framework, for crystal plasticity simulations on all scales from the single crystal up to the engineering component, was initiated. The new code is strictly modularized to allow easy incorporation of additional models on all length scales. In this way, two different homogenization schemes and seven different constitutive models for plasticity, including a non-local one treating dislocation fluxes [4, 5], have been incorporated into the code package. The ability to use different constitutive models within a single simulation is a unique feature of the code. In 2010, in collaboration with Prof. R. Lebensohn (LANL, Humboldt awardee at MPIE at that time), a spectral method based boundary value problem solver was added to complement the commercial FEM solvers. In 2011, it was decided to release the code, by now called DAMASK, as free software to the public domain. For that purpose, a website (damask.mpie.de) was launched in September 2011. The science community very well received the idea of a free crystal plasticity code. At least 15 groups, including universities like UCLA, research facilities like LANL as well as companies like Tata Steel (IJmuiden), today use DAMASK worldwide (as it can be freely downloaded we do not know the real number). These groups contribute to the further code development as well as adding new features to DAMASK including new/modified constitutive models [6]. Currently DAMASK is extended towards a multi-field solver. This will allow treating coupled problems, e.g. thermo-mechanical-chemical, in a fully consistent way.