Tomographic orientation microscopy (3D EBSD) on steels using a joint FIB SEM technique
S. Zaefferer, D. Raabe, A. Khorashadizadeh
We present our recent progress in 3D high resolution characterization of crystalline microstructures. Our approach uses automated serial sectioning by means of a focused ion beam (FIB) and the sequential characterization of each section in terms of orientation microscopy based on electron backscatter diffraction (EBSD) in a combined FIB-scanning electron microscope (SEM). The instrument integrates a Zeiss Crossbeam FIB-SEM and an EDAX-TSL EBSD system reaching spatial orientation resolutions as small as 503 nm³. The maximum observable total volume is in the order of 503 μm³. The 3D EBSD approach allows the characterization of microstructure parameters that cannot be accessed by 2D methods, for instance the full crystallographic characterization of interfaces, including the morphology and the crystallographic indices of the interface planes. The current paper reflects the technical background as well as the limits of the technique and presents a number of steel-related examples.
1 Introduction
Metallography for the characterization of microstructures is typically conducted on 2D sections. Although stereological statistics allow one to study certain 3D aspects of microstructures [1,2] nu merous cases exist where a direct 3D observation is required for understanding the evolution of microstructures and its relation to material properties. Cases where such direct 3D information is important are, for instance, the topology of grains in conjunction with grain growth investigations, the size and shape of deformation-induced strain fields, or the full characterization of nucleation phenomena. One set of parameters that is completely missing in conventional 2D observations is the crystallographic characterization of interfaces. In 2D EBSD studies the misorientation across a boundary can be determined; however, since the spatial orientation of the boundary plane is unknown, the orientation of the boundary plane relative to the abutting crystal lattices remains unknown.
The 3D analysis of microstructures can be conducted using 2 principal approaches, either by destructive serial sectioning or by observation with transmissive radiation. The latter techniques retrieve the 3D information from bulk samples either by reconstruction from a large number of extinction images taken from different directions or by a ray-tracing technique. The latter method allows crystallographic information to be obtained [3-6]. The current spatial resolution of these techniques is of the order of some μm³ [7, 8].
Simpler than these bulk methods for 3D characterization of crystalline materials are the serial sectioning tomographic techniques. These approaches use a sequence of cuts through a given microstructure, record the microstructure in each slices (using e.g. EBSD or EDX), and reconstruct from all sequential slices the 3D aggregate, e.g. by stacking the recorded 2D data maps.
For serial sectioning different methods can be used, e.g. mechanical cutting, sequential polishing, chemical polishing, laser cutting, or electrical discharge ablation. For characterizing the microstructure in each serial section, all standard microscopic techniques are available, e.g. light optical or SEM backscattered electron imaging. The main challenge associated with many of the sectioning methods lies in controlling the sectioning depth, obtaining flat and parallel surfaces, and correctly re-detecting and aligning the observation area. On the observation side, the main obstacle is that most observation techniques do not allow certain microstructural features such as grain boundaries or individual grains to be separated because the contrast conditions are not well enough defined. Finally, most of serial sectioning methods are extremely laborious. Examples for various sectioning methods are discussed in [9].
A technique that avoids in an ideal way these sectioning and imaging problems is the combination of serial sectioning with an ion beam and EBSD (electron backscatter diffraction)-based orientation microscopy in the form of a combined FIB (focused ion beam)-SEM (scanning electron microscope). The focused ion beam consists of Ga+ For observing the microstructures in each serial section, EBSD-based orientation microscopy is an excellent technique since it allows one to clearly identify the different phases, grains, and interfaces in terms of their lattice parameters and crystallographic orientation, respectively [15-22]. ions, accelerated to, for example, 30 keV. The impact of the beam onto a sample leads to localized sputtering of the target material and can therefore be used to cut into the material of few nanometers in width. Irradiating a material surface in grazing incidence allows preparation of smooth surfaces at negligible radiation damage [10-12]. Some earlier papers describe the use of this technique for the preparation of TEM specimens [12]-[14].
The aim of this work is to give an introduction to the emerging tomographic 3D EBSD technique based on serial sectioning using a FIB and 2D EBSD-based orientation microscopy. We illustrate the technique with some steel-related examples from our Max-Planck group in Düsseldorf. Some earlier results, obtained in part by a non-automated 3D EBSD method, were documented in preceding publications [9,23,24].
2 Technical set-up for 3D microstructure characterization in a FIB-SEM
2.1 Geometrical set-up of the system
We use a Zeiss-Crossbeam XB 1540 FIB-SEM which consists of a Gemini-type field emission gun electron column and an Orsay Physics ion beam column mounted 54° from the vertical. For EBSD, a computer-control Digiview camera of EDAX-TSL is used. An energy dispersive X-ray spectroscopy (EDX) detector is mounted such that EBSD and EDX signals can be simultaneously detected. The EBSD camera and EDX detector are mounted opposite of the ion column, figure 1a.
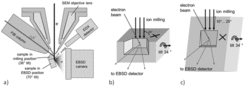
For EBSD analysis the investigated surface is usually tilted 70° from the horizontal position. This requires a sample tilt between grazing incidence ion milling and EBSD of 34°, figure 1b.
When using this kind of tilt set-up two measurement strategies can be pursued. The first one, hereafter referred to as grazing-incidence edge milling (GIEM) method, is shown in figure 1b. The sample is prepared by grinding and polishing to produce a sharp edge. Milling is then performed under grazing incidence to one surface at this sample edge. After milling has created a smooth surface, the sample is moved into EBSD position by a 34° tilt and a corresponding y-movement of the stage. EBSD is performed on this surface. After EBSD has completed, the sample is returned to the milling position and the next cut can be carried out.
The second method, referred to as low-incidence surface milling (LISM) approach, is illustrated in figure 1c: The initial sample preparation produces a polished surface. For milling on the free surface the sample is tilted such that the ion beam hits the surface at a 10 to 20° angle. As in the GIEM method, the sample is subsequently tilted by 34° and EBSD analysis is performed on the milled surface.
For both types of set-up the size and shape of the milled area is determined, on the one hand, by the size of the investigated surface. On the other hand, it has to be considered that the edge of the milled area projects a shadow onto the EBSD camera. The shadow increases with increasing distance of the milled area from the free sample surface and decreasing distance between EBSD camera and sample surface. For high-speed EBSD, a large acceptance angle of the diffraction pattern is beneficial. At a camera position of 20 mm we obtain an acceptance angle of approximately 120°. This means that the milled area must be bound by at least 60° angles on all three edges in order to allow shadow-free diffraction patterns. This additionally milled volume may significantly increase milling time at large milling depths or when applying the LISM method. A reasonable alternative is to remove the shadowing areas with a large ion beam current and mill only the investigated surface with a small and therefore finely focused ion current. This is accomplished in our system by setting-up a milling list which holds a number of user-defined milling areas. For both measurement strategies, a position marker is required that allows accurate positioning of the sample after movement from EBSD observation to milling or vice versa. As a position marker we use a cross that is milled next to the measured area into the sample surface.
2.2 Automatic 3D EBSD microscopy
Running the 3D milling and EBSD cycle fully automatically requires a number of instruments and processes to be synchronized: for orientation microscopy the SEM, the EBSD program, the camera slide controller, the camera controller and the electron image drift correction program have to cooperate. For sectioning, the FIB and the FIB image drift correction program are required. Finally for changing between milling and EBSD position the sample stage needs to be accurately controlled. All participating processes are controlled by one 3D measurement program. Once the software is configured, it runs the milling and EBSD cycle until a predefined number of cycles has been reached. Each analysis cycle consists of the following steps: First, the EBSD camera is moved into position. Second, the position marker is detected by image cross-correlation and the sample is placed to its reference position using beam shift functions. Third, a reference image is taken in EBSD position. Fourth, 2D EBSD mapping is conducted using the predefined camera control parameters. Fifth, after orientation mapping the camera is retracted, the stage is moved to the predefined milling position and the FIB gun is switched on if it was off. Sixth, the microscope is switched to FIB mode and the position marker is detected by cross correlation. A shift of the FIB beam brings the milling area into reference position. Seventh, a reference image is taken using the FIB beam to document the milling progress from the FIB position. Eighth, the FIB switches to milling mode, steps the beam forward to the desired z-step size, and performs the milling list. Finally, when the milling process is over, the FIB-gun is turned off and the stage is moved back to its predefined EBSD position.
For the analysis of the 3D EBSD data we use a batch processing function of the EDAX-TSL OIM Analysis software. This function allows to conduct similar operations to any number of measured data sets, for example rotation of the reference system, clean-up, map construction and saving of images to disk. Our in-house developed software allows one to determine the crystallography and morphology of interfaces. Subsequently the local grain boundary normals in the sample and crystal reference systems can be calculated. An important precondition for rendering 3D data is the precise alignment of the underlying 2D EBSD slices. Although this is achieved to a large extent during the data acquisition process the final 2D data can in some cases still show misalignment between the slices. For this reason we developed an alignment tool which is based on the calculation of a correlation function. Another well-known software package for 3D rendering is, for example, the program IMOD that is based on the construction of 3D wire-frame models from 2D cuts [9,25]. Other groups have developed software that allows one the selection of 3D grains and the determination of volume properties of these grains [21]. A powerful 3D representation of grain boundaries has been presented by Rowenhorst et al. [26], who use a coloring of grain boundaries according to the position of its local crystallographic normal vector in a standard orientation triangle. A more detailed discussion of the basics of the novel 3D EBSD technique is given in [27].
3 Examples of tomographic 3D EBSD investigations
3.1 Basics
In this part some examples of 3D EBSD studies are presented which made use of the approach introduced above. The main strength of the current system lies in the high spatial EBSD resolution which allows us to identify complex microstructures even in deformed or multiphase materials. The limits of the system are the relatively small total volume that can be accessed and, in certain cases, possible irradiation damage effects due to the ion beam bombardment used for cutting.
For all measurements presented, the ion beam column was operated at an accelerating voltage of 30 kV with beam currents between 100 pA and 2 nA. For EBSD, an electron accelerating voltage of 15 kV was used. The EBSD camera was positioned approximately 20 mm away from the sample. All EBSD measurements were performed at a high measurement rate of 65 to 70 patterns per second. This could only be accomplished by minimizing pattern indexing calculation time. To this end, in multiphase materials only the simplest phase was indexed online. The complete indexing for all phases was then performed offline from the recorded Hough-peak data using the full crystallographic information. Further details are given in [27].
3.2 Pearlite
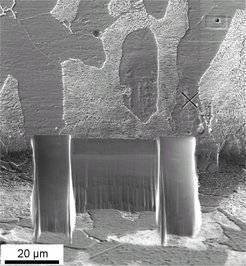
Pearlite is a lamellar arrangement of α-ferrite and cementite formed in an eutectoid reaction from austenite. In 2D investigations, pearlite often exhibits characteristic bending of the lamella structure which is related to a significant orientation change of the ferrite and likely also of the cementite. The latter aspect has not been well analyzed so far because the crystal orientation of cementite is very difficult to measure by electron diffraction techniques due to its low structure factor. The occurrence of bending and of the related orientation change is an interesting hint on the physical mechanism of phase transformation. Various models were proposed to explain pearlite formation [28-30]. For two reasons the 3D investigation of pearlite lamellae may yield new and otherwise inaccessible information: First, the direction of the maximum occurring orientation gradients may be determined and spatially correlated with the strength of lamella curvature. Second, the ferrite-cementite phase boundary can be characterized with respect to the ferrite grain boundary normal.
For the current study a Fe-0.49wt.% C steel has been selected. The sample was heated to 950°C and then cooled at a rate of 0.1 K/s. Figure 2 shows the sample after milling. The cementite lamella (white) had a width of 100 to 200 nm and a distance varying between 200 and 400 nm. 50 slices of 30 x 20 μm² were milled with a step size of 100 nm. EBSD was also conducted at a lateral step size of 100 nm. Only the ferrite phase was indexed since cementite did not produce indexable patterns.
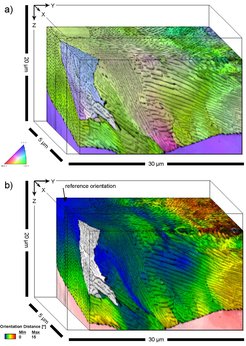
Figure 3a displays the result of the measurement in the form of a 3D orientation map where the color of each voxel (volume pixel) is a combination of the diffraction pattern quality which defines the brightness of the voxel and the orientation of the measurement plane normal which defines the color according to the inverse pole figure color triangle. Though cementite could not be indexed, the reduced ferrite diffraction pattern quality indicates the position of the lamellae. The figure shows the high alignment accuracy of the data: at many positions, it is possible to track the pearlite lamella in full 3D. Figure 3b reveals the strong orientation change across the volume, where the color code denotes the misorientation angle of a given voxel with respect to a reference orientation. As reference, the orientation of the lamella-free area in the upper back corner is selected. The maximum indicated misorientation is 15°. The data reveal that the pearlite consists of 2 grains and several colonies. While strong continuous ferrite orientation gradients run parallel to the pearlite lamellae, generally no continuous orientation change occurs perpendicular to the lamellae; in contrast, small angle grain boundaries are found to lie mainly parallel to the lamellae. The convergence of the orientation gradient with the lamella position shows that the orientation gradient is directly related to the growth process of the lamellae.
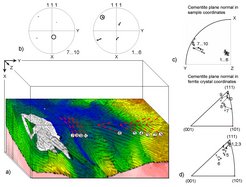
The results of some first interface investigations are demonstrated in figure 4: Two colonies of pearlite lamellae, 1 to 6 and 7 to 10 have been investigated. As indicated by the pole figures in fig. 4b, in each of the lamellae groups the ferrite crystals continuously rotate about a (111) plane. The rotation pole, however, is different for both groups. The positions of the lamellae normals relative to the sample reference frame are displayed in the pole figure in fig. 4c and, relative to the ferrite crystal orientation, in inverse pole figures in fig. 4d. The inverse pole figures show that the ferrite phase boundaries are close to (111); albeit, with a significant deviation of up to 16°. It has been shown by TEM investigations that the atomic habit plane of ferrite-cementite lamellae may be ( 1 2 5), (1 1 2) or (0 1 1) [31],[32] depending on the orientation relationship between both phases. While the (111) plane determined here deviates considerably from these results, it has, in fact, been shown that there is not necessarily any correspondence between the atomic habit plane and the macroscopic one [33]. Furthermore, from the present results it seems that there is also no clear relationship between crystal orientation and macroscopic habit plane.
3.3 Nanocrystalline NiCo deposits
Electrodeposition from aqueous solution has been intensively studied as a method to create metallic films with nanocrystalline microstructure [34-39] The deposition parameters, such as solution composition, current density and bath movement strongly influence the developing microstructure. The exact mechanisms of microstructure formation are still largely unknown, also because a precise characterization of the microstructure has rarely been undertaken. In a recent study [40] we applied high resolution EBSD to obtain a deeper knowledge on the microstructure of electrodeposited thin films of NiCo. Most of the investigated films consist to a large volume fraction of columnar crystals with cross sections in the sub-micrometer range but lengths in the order of more than 30 µm. For all columnar grains <112̅0> direction is close to the growth direction of the crystal column. Only in niches besides these crystals areas of truly nanocrystalline material do exist. We found furthermore that the elongated crystals are in most cases growing in triples of 3 parallel crystals which are related to each other by a twin orientation relationship. The existence of these triples can be seen on the free grown surface of the electrodeposited material in the form of 3-fold pyramids. We suspect that the existence of twins stabilizes the growth of columnar grains by formation of low energy boundaries.
3D orientation microscopy was performed on a full, 100 µm wide cross section of an electrodeposited material. The sample was manually ground and polished on the cross sections to produce a sharp rectangular edge. A step size of 100 nm in all dimensions was selected and 60 maps covering a volume of 83 x 16 x 6 µm³ were measured. The results are shown in figure 5a in form of a material block, colored according to the inverse pole figure of a direction perpendicular to the growth direction. Usual large angle grain boundaries are colored black while all possible twin boundaries are displayed as white lines. In the centre of the block a part has been cut out to display a typical twin-triple.
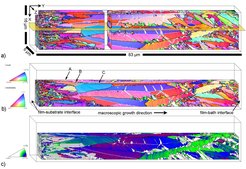
In figure 5b the block is cut along the plane that contains the twin triple indicated in fig. 6. The triple is not growing straight but it is curved. Together with this curvature the orientation of the triple changes as shown in figure 5c which displays the deviation of the macroscopic growth direction from the <112̅0> crystal direction. The crystal orientation is continuously deflected by the regular occurrence of some sort of lattice defects. The nature of these lattice defects, visible in form of inclined stripes in figure 5c, is not yet clear. In the centre of the measured block the twin triple consists of 3 grains with two 56° <112̅0> twin relations between them and an approximately 66° <112̅0> relationship on the remaining boundary. On the basis of our earlier 2D investigations [40] we proposed the following formation mechanism for the triple. A primary crystal (1) twins independently with the same twin relationship into two twin variants (2) and (3) such that all three crystals show a <112̅0> direction parallel to the macroscopic growth direction optimum for quick growth. The boundary between the crystals (2) and (3) is then automatically fixed to a 66° <112̅0> relationship. In the light of the new 3D data this explanation no longer seems totally correct. Following the triple in growth direction we first notice that the grains (1) and (2) exist as twins with a sharp 57° <112̅0> relation already when they first enter into the measurement area (marked as point A in figure 5b) (note that grain (2) is not visible in the figure as it is on top of grain (1)). At point B, grain (3) nucleates and grows for the first approximately 10 µm as a very thin tube parallel to grains (1) and (2). At the position where the grains reach a position for optimum growth (i.e. <112̅0> parallel to the macroscopic GD) grain (3) also expands and grows larger (point C). At this position we applied the 3D analysis program to determine the grain boundary characteristics.
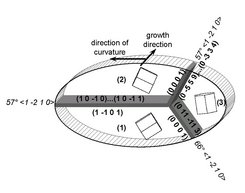
The results are displayed in figure 6: between grain (1) and (2) we observe the {101̅1} twin boundary, typical for these twins [41]. Grain (3), although it shows a precise twin orientation relation with grain (2), does not have a twin boundary with the latter, i.e. the plane indices on both sides of the grain boundary are different, the one of grain (2) being very precisely the (0001) basal plane, the other one being some quite highly indexed one. The same is true for the boundary with grain (1) although this grain boundary even does not show any typical twin orientation relationship. We conclude that grain (3) is a twin of grain (2) but its boundary is incoherent and therefore of a quite different quality than that between (1) and (2). We suppose furthermore that the (0001) basal planes that appear in the triple grain arrangement form low energy boundaries both in case of the incoherent twin ((2)-(3)) as well as in case of the less specific large angle grain boundary ((1)-(3)).
3.4 Cu-0.17wt%Zr deformed by equal channel angular pressing (ECAP)
This is an example about a tomographic EBSD study of the 3D microstructure of Copper with 0.17wt% Zr deformed by equal channel angular pressing (ECAP). Prior to the ECAP deformation, the material was annealed for 10 hours at 940°C. After the first ECAP pass the sample was annealed at 650°C for 1 hour in order to obtain a homogeneous microstructure. Specimens with 10mm×10mm cross-section and 60mm length were machined from these annealed bars. ECAP deformation was carried out at room temperature with 4 and 8 passes, respectively, with a 90° die angle corresponding to a total equivalent strain of about 4.6 and 9.2, respectively. Deformation was conducted using a process route which is characterized by a 90° rotation of the billet around its longitudinal axis after each pass at constant sense of rotation. After ECAP deformation samples were cut by spark erosion. After electrochemical preparation the samples were investigated as described above.
Fig. 7a shows a sequence of some selected 2D EBSD slices that are used for 3D grain reconstruction and the full 3D EBSD view of the Cu0.17wt%Zr specimen after 4 ECAP passes. The slices represent crystals in terms of an inverse pole figure color code, where each orientation is indicted by a specific color according to its current normal direction axis. Fig. 7b shows the sample after 8 ECAP passes. It is worth noticing that although both ECAP samples were highly deformed the serial sectioning as well as the EBSD data acquisition was possible with about 50 % of successfully indexed points. This is a relatively small value compared to well annealed samples but it is excellent for heavily strained samples.
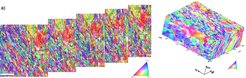
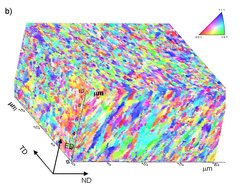
As can be seen from the 3D microstructure representations, the structure of the ECAP sample after 8 passes is more homogeneous with more equiaxed grains than the ECAP sample after 4 passes. Both samples reveal elongated grains under 45° with respect to the extrusion direction (ED). The crystallographic textures observed after 4 and 8 passes are similar to those observed for other FCC structured materials which were deformed by the ECAP process.
3.5 Dislocation patterning below nanoindents in Cu single crystals
As another application of the 3D EBSD method we conducted a study on the microstructure and crystallographic orientation pattern formed during Nan indentation in Cu single crystals [25,42-46]. The background of this project is to obtain a better understanding of the dependence of the mechanical properties of metals on the volume portion under load. This phenomenon is referred to as mechanical size effect. It means that specimens resist at different scales differently to mechanical stresses. In this study we investigate jointly the lattice defects that are assumed to create the size effect and the hardness and, thereby, show that existing theories of the size effect do not apply to the present case.
To be more specific, the mechanical size effect has been explained in terms of an inverse relationship between the size scale of an experiment and the magnitude of the strain gradients that form in the deformed volume affected. Strain gradients have been associated with geometrically necessary dislocations (GND) [47]. These are linear lattice defects that accommodate lattice curvature and their density is assumed to determine the effect on the size scale of the experiment on the local hardness. This interpretation of the mechanical size effect implies that the smaller the scale of a deformation experiment is (e.g. Nan indentation), the higher the strain gradients and hence, the GND densities should be.
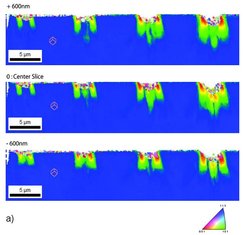
Owing to this background we study the link between the indentation size effect and the GND density by using the following approach: Four indents with different indentation depth and hardness were placed in a Cu single crystal using a conical indenter with spherical tip of radius 1mm. Next, the deformation-induced lattice rotations were monitored in 3D below the indents at 50 nm resolution using the tomographic 3D EBSD method introduced above (3 of the 50 subsequent 2D EBSD slices are shown in figure 8a). Finally, the GND densities were calculated from the measured rotations using the dislocation density tensor which connects lattice curvature to the GNDs. This approach allows us to directly quantify in one experiment both the mechanical parameters (depth, hardness) and the lattice defects (GNDs) that are held responsible for the Nan indentation size effect.
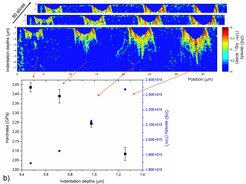
Fig. 8: b) What is the reason for mechanical size effects in Nan indentation? Top row: GND density distribution around the four indents. Bottom row: GND density obtained from 5 center slices. The data reveal that the GND density is not responsible for the mechanical size effect, as commonly suggested by corresponding theories, but actually drops with smaller size scale.
Fig. 8b shows the GND distribution around the four indents and their total density determined from the 5 inner layers. The data reveal three main points: First, the GND arrangement reveals pattern formation. Second, the distribution of the GND density is anisotropic with respect to the center slice. Third and most importantly, the density of the GNDs does not increase with decreasing indentation depth but it drops. More precisely, while the hardness increases from ~2.08 GPa for the largest indent (1230 nm) to ~2.43 GPa for the smallest one (460 nm) the GND density decreases from ~2.34×1015 m-2 (largest indent) to ~1.85×1015 m-2 (smallest indent).
The first two observations, viz. patterning and anisotropy of the lattice curvature were reported before [25,42-46,48]. The third observation, though, is quite surprising and contradicts the commonly expected inverse relationship between the indentation depth and the density of the GNDs.
3.6 Analysis of an abnormally growing Goss grains in Fe-3wt.%Si
Silicon steel is a soft magnetic material that is used in electrical power transformers, motors and generators. It has a high silicon content of about 3.2 mass %, which increases the electrical resistivity of iron and, therefore, reduces eddy current losses. Grain-oriented silicon steel that is used for non-rotating applications, i.e. transformers, is characterized by a strong preferred crystallographic orientation. In iron the directions of easiest magnetization are the <001> crystal directions. In grain-oriented silicon steel the Goss orientation, i.e. the {110}<001> orientation, is technologically realized to minimize magnetic losses in electrical transformers [49-53]. Overview on the evolution of the Goss orientation in silicon steels has been given in [54-59].
The strong Goss texture of grain-oriented silicon steel is the result of a complex processing scheme, i.e. of a long microstructural and textural inheritance chain. The origin of the evolution of the Goss orientation in the final sheet product lies particularly in the hot rolling stage, where the Goss orientation develops close to the sheet surface due to shear deformation [60-65]. The particular importance of this Goss-containing subsurface layer has been demonstrated by experiments where this layer was removed, resulting in incomplete secondary recrystallisation [56,57,66]. In the cold rolled material, the fraction of the Goss orientation is, considering a misorientation of up to 15°, about 1% as measured using electron backscatter diffraction (EBSD), i.e. the Goss component is too weak to be detected by x-ray diffraction as used in earlier studies. In the subsequent primary annealing step, the material recrystallizes and the Goss component slightly increases. In the final secondary high-temperature annealing process, normal grain growth is inhibited by particles. But some of the Goss grains that are present in the recrystallized material grow abnormally giving rise to a sharp Goss texture with an average misorientation from the exact Goss orientation of about 3°-7°. The exact mechanisms of inheritance of the Goss orientation through the process chain and details of abnormal Goss grain growth in the secondary annealing stage are still unclear.
Since all existing theories on abnormal Goss grain growth (see overviews in [54-59]) only consider the misorientation of the grain boundary, but not its orientation in space, we conducted 3D EBSD orientation measurements to reconstruct a Goss grain boundary in 3D. Fig. 9a shows the underlying microstructure observed during FIB sectioning of the grain structure under observation. Fig. 9b gives a number of sequential EBSD maps which were used for the full 3D reconstruction of the interfaces between the large Goss grain and a small neighbor crystal with large curvature. Fig. 9c shows the shape of the small grain which abuts the much larger Goss crystal and fig. 9d shows the corresponding interface of the Goss grain.
The grain boundary with the exceptionally high curvature between the Goss grain and the round-shaped grain with approximately {123}<311> crystal orientation (figs. 9b,c) indicates its very low mobility. The misorientation is 36° about a <112> axis. The grain boundary does not reveal any pronounced faceting.
4 Conclusions
This study presented the basics and some steel-related examples of a novel 3D orientation microscopy technique that is based on automated serial sectioning via ion beam milling and EBSD-based orientation microscopy in a FIB-SEM. The technique is capable of conserving all powerful features of the well known 2D EBSD-based orientation microscopy technique and extends them into the 3rd spatial dimension. It yields a multidimensional data vector for each voxel of the measured volume, including the crystal orientation, the crystallographic phase, a value for the lattice defect density, and, if measured by simultaneous EDS analysis, the elemental composition.
5 References
[1] B.L. Adams, Met. Trans. 17A, (1986) 2199
[2] B.L. Adams, P.R. Morris, T.T. Wang, K.S. Willden, S.I. Wright, Acta Met 35 (1987) 2935
[3] H.F. Poulsen et al., J. Appl. Cryst. 34 (2001) 751
[4] B.C. Larson et al., Nature 415 (2002) 887
[5] W. Yang et al., Micron 35 (2004) 431
[6] A. Preusser, H. Klein, H.J. Bunge, Solid State Phenomena 105 (2005) 3
[7] E.M. Lauridsen, S. Schmidt, S.F. Nielsen, L. Margulies, H. F. Poulsen, D. Juul-Jensen, Scripta Mat. 55 (2006) 51–56
[8] L. Margulies, G. Winther, H.F. Poulsen, Science 291 (2001) 2392
[9] J. Konrad, S. Zaefferer, D. Raabe, Acta Mat. 54 (2006) 1369
[10] S.V. Prasad, J.R. Michael, T.R. Christenson. Scripta Mat. 48 (2003) 255.
[11] J.R. Michael, J. Schischka, F. Altmann, in: HKL Technology EBSD Application Catalogue 2003, HKL Technology, Hobro, Denmark
[12] T.L. Matteson, S.W. Schwartz, E.C. Houge, B.W. Kempshall, L.A. Gianuzzi, J. Electronic Mater. 31, 2002, 33 - 39
[13] Z. Cheng , T. Sakamoto, M. Takahashi, Y. Kuramoto, M. Owari, Y. Nihei, J. Vac. Sci. Technol. B 16 (1998) 2473
[14] H. Jin, P.D. Wu, M.D. Ball and D.J. Lloyd, Mater. Sci. Technol., 21 (2005) 419
[15] A. J. Schwartz, M. Kumar, B. L. Adams (eds.), Electron Backscatter Diffraction in Material Science. Kluwer Acad./Plenum Publ., New York 2000
[16] F.J. Humphreys, J. Mat. Sci. 36 (2001) 3833
[17] D. J. Dingley, J. Microscopy 213 (2004) 214
[18] G. Spanos, Scripta Mat. 55 (2006) 3, Viewpoint set no. 41 “3D Characterization and Analysis of Materials”
[19] M.D. Uchic, M. Groeber, R. Wheeler IV, F. Scheltens, D.M. Dimiduk. Microsc. Microanal. 10 (2004) 1136
[20] J.J.L. Mulders, A.P. Day, Mat. Sci. Forum, 495-497 (2005) 237
[21] M.D. Uchic, M.A. Groeber, D.M. Dimiduk and J.P. Simmons, Scripta Mat. 55 (2006) 23
[22] M.A. Groeber, B.K. Haley, M.D. Uchic, D.M. Dimiduk, S. Gosh, Mat. Character. 57 (2006) 259
[23] S. Zaefferer., J. Konrad, D. Raabe, (2005), Microscopy Conference 2005, Davos, 63
[24] N. Zaafarani, D. Raabe, R.N. Singh, F. Roters, S. Zaefferer, Acta Mat. 54 (2006) 1863
[25] J.R. Kremer, D.N. Mastronarde, J.R. McIntosh, J Struct Biol. 116 (1996) 71.
[26] D.J. Rowenhorst, A. Gupta C.R. Feng and G. Spanos, Scripta Mat. 55 (2006) 11
[27] S. Zaefferer, S.I. Wright, D. Raabe, Metall. Mat. Trans. A, 39, 374 (2008).
[28] F.A. Khalid and D.V.Edmonds Acta Mat. 41 (1993) 3421
[29] M. Durrand-Charre, Microstructures of steels and cast irons, Springer, (2004)
[30] G.J. Shiflet, Mater. Sci. Eng., 81 (1986) 61
[31] D.S. Zhou, G.J. Shiflet, Met Trans 23A (1992) 1259
[32] G. Spanos, H.I. Aaronson, Acta Metall. Mater. 38 (1990) 2721
[33] S.A.Hackney, G.J. Shiflet, Scripta Metall. 20 (1986) 389
[34] A.Vicenzo, P.L. Cavallotti, Electrochimica Acta 49 (2004) 4079
[35] D. Golodnitsky, Yu. Rosenberg, A. Ulus, Electrochimica Acta 47 (2002) 2707
[36] E.Gómez, J. Ramirez, E. Vallés, J. Appl. Electrochem. 28 (1998) 71
[37] K. Daheum, D.-Y. Park, B.Y. Yoo, P.T.A. Sumodjo, N.V. Myung, Electrochimica Acta (2003) 819
[38] A.M. El-Sherik, U. Erb, J. Mater. Sci. 30 (1995) 5743
[39] B.Y.C.Wu, P.J.Ferreira, C.A. Schuh, Met. Mater. Trans. A, Vol.36A (2005) 1927.
[40] A. Bastos, S. Zaefferer, D. Raabe, C. Schuh, Acta Mater. 54 (2006) 2451
[41] P. G. Patridge, Met. Rev. 12 (1967) 169
[42] N. Zaafarani, D. Raabe, F. Roters, S. Zaefferer, Acta Mater. 56 (2008) 31-42
[43] D. Kiener, R. Pippan, C. Motz and H. Kreuzer, Acta Mater. 54 (2006) 2801
[44] Y. Wang, D. Raabe, C. Klüber, F. Roters, Acta Mater. 52 (2004) 2229
[45] N. Zaafarani, F. Roters, D. Raabe, Mater. Sc. For. 550 (2007) 199
[46] M. Rester, C. Motz, R. Pippan, Acta Mater. 55 (2007) 6427
[47] M.F. Ashby, Philos. Mag. 21, 399 (1970).
[48] W. Yang, B.C. Larson, G.M. Pharr, G.E. Ice, J.Z. Tischler, MRS Symp. Proc. (2003) 779, W5.34.1
[49] A. Morawiec: Scripta Mater. 43 (2000) 275
[50] H. Homma and B. Hutchinson: Acta Mater. 51 (2003) 3795
[51] P. Lin, G. Palumbo, J. Harase and K.T. Aust: Acta Mater. 44 (1996) 4677
[52] N. Chen, S. Zaefferer, L. Lahn, K. Günther, D. Raabe, Acta Mater. 51 (2003) 1755
[53] D. Dorner, S. Zaefferer, D. Raabe, Acta Mater. 55 (2007) 2519
[54] D. Dorner, S. Zaefferer, L.-Lahn, D. Raabe, J. Magnetism Magnetic Mater. 304 (2006) 183
[55] M. Matsuo, ISIJ International 29 (1989) 809
[56] S. Mishra, C. Därmann, K. Lücke, Acta Metallurgica 32 (1984) 2185
[57] N. Pease, D. Jones, M. Wise, W. B. Hutchinson, Metal Science 15 (1981) 203
[58] K. Ushioda and W.B. Hutchinson: ISIJ International Vol. 29 (1989), pp. 862-867
[59] S. Zaefferer, T. Baudin and R. Penelle: Acta Materialia Vol. 49 (2001), pp. 1105-1122
[60] M. Hölscher, D. Raabe, K. Lücke, Steel Research 62 (1991) 567
[61] D. Raabe, K. Lücke: Scripta Metall. 26 (1992) 1221-1226
[62] M. Hölscher, D. Raabe, K. Lücke, Acta Metall. et Mater. 42 (1994) 879
[63] D. Raabe, K. Lücke, Mater. Sc. Techn. 9 (1993) 302
[64] D. Raabe, Acta Mater. 45 (1997) 1137
[65] D. Raabe, Steel Research 74 (2003) 327
[66] A. Böttcher, K. Lücke, Acta Metall. Mater. 41 (1993) 2503
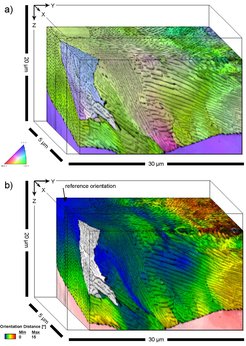