Development of High-Strength Aluminium Alloys for Additive Manufacturing
In this project we develop new aluminium alloys specifically for L-PBF that have both high strength and high resistance to solidification cracking. Modifying the chemical composition of commercial high-strength aluminium alloys and developing new alloys based on L12-Al3X-forming elements are the two different strategies.
Laser Powder Bed Fusion (L-PBF) is among the most widespread processes for the additive manufacturing (AM) of metals. L-PBF of aluminium alloys is associated with difficulties that mainly arise from various properties of aluminium, such as high reflectivity, high thermal conductivity, and a strong tendency for oxidation. So far, L-PBF has only been successfully applied to a limited number of aluminium alloys, of which Al-Si based cast alloys are the most widely utlised materials. Due to the moderate mechanical properties, aluminium cast alloys are not expected to meet the needs of demanding structural applications. The spectrum of well-processable high-strength aluminium alloys for L-PBF is still limited since traditional high-strength alloys cannot be readily processed due to their high tendency for solidification cracking.
We work on developing new aluminium alloys specifically for L-PBF that have both high strength and high resistance to solidification cracking. For this purpose, two different strategies are employed. First, the chemical composition of commercial high-strength aluminum alloys is modified with the aim of reducing the cracking tendency, enabling their use in AM. Secondly, new alloys based on L12-Al3X-forming elements are developed which

Figure 1: The formation of hot cracks in a commercial high-strength Al-Cu alloy during laser melting is suppressed by the modification of its chemical composition.
show promising combinations of processability and strength. In contrast to traditional high-strength alloys which can also be produced by conventional manufacturing, these alloys rely on the formation of a metastable supersaturated solid solution during the process and therefore exploit the high cooling rates that are a characteristic feature of L-PBF.
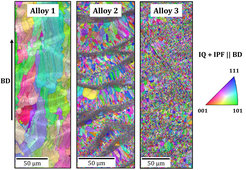
Figure 2: EBSD-IPF maps showing microstructures of three L-PBF produced aluminium alloys with different degrees of grain refinement (BD: building direction).