New High Strength Steels with Reduced Hydrogen Embrittlement Sensitivity
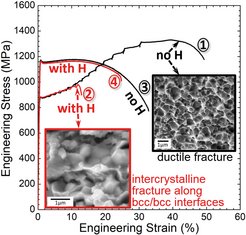
Fig. 1: Stress-strain curves for the steel from slow strain rate tensile tests. Conventionally processed sample without H (curve 1): ductile fracture and high total elongation. Charging with H (curve 2): intercrystalline fracture and high loss of total elongation. Modified processing (curve 3 and 4) increases yield strength and lower loss of total elongation by H.
We investigated a medium Mn steel with the chemical composition 0.2C-10.2Mn-2.8Al-1Si (in wt.%). Medium Mn steels combine high strength and ductility and are candidates for future automotive applications. But not much is known about HE sensitivity and embrittlement mechanisms in these multiphase steels. A method to quantify the sensitivity against HE is the slow strain rate tensile test. Curve 1 in Fig. 1 shows the stress-strain curve for this steel after conventional processing and no H charging. The yield strength is 890 MPa and the total elongation 51 %. When the steel is charged with H (curve 2), the total elongation is significantly reduced to 13 %. The difference between the total elongations of uncharged and H charged samples allows to quantify the HE sensitivity. Here, this loss in total elongation is high (38 %) and indicates a high HE sensitivity. The appearance of the fracture surfaces after tensile testing (Fig. 1) provides information about the failure mechanisms: Dimples on the fracture surface of the sample without H (curve 1) reveal a ductile fracture. This changes for the sample with H (curve 2), which shows a more brittle failure along interfaces.
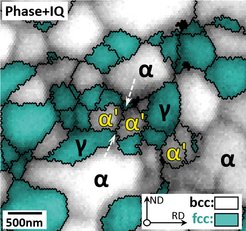
Fig. 2: Initial microstructure: austenite (g) with fcc structure and ferrite (a) with bcc structure. During plastic deformation austenite transforms to martensite (a').
A detailed characterization reveals the mechanisms leading to HE: The microstructure of the medium Mn steels shows two phases: face centered cubic (fcc) austenite (g) with a volume fraction of 60 % and body centered cubic (bcc) ferrite (a). In the bcc lattice H diffusion is much faster, but H solubility is much lower than in austenite. When charging with H, finally austenite contains much more H than ferrite. During deformation metastable austenite transforms partially into martensite (a`) (Fig. 2). This martensitic transformation is very fast. Therefore, martensite inherits all the H from austenite. This leads to drastic H oversaturation of martensite as martensite has a bcc lattice and hence a very low H solubility (Fig. 3).
Due to the high diffusivity of H in martensite, the H can escape the oversaturated lattice by moving to interfaces like a`/ a` grain boundaries. This leads to the observed embrittlement of these interfaces.
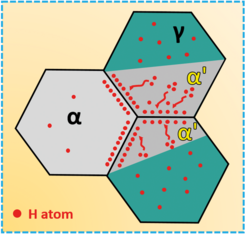
Fig. 3: Schematically: H in oversaturated martensite (a') segregates to grain boundaries. Embrittlement of these boundaries leads to observed intercrystalline failure.
To avoid these mechanisms, we lowered the heat treating temperature. This provides a finer grain size (higher yield strength of modified processed steel curve 3) and more Mn and C partitioning to austenite stabilizes the austenite. During deformation, less martensite is formed and the sensitivity against HE is decreased: The H charged sample (curve 4) in comparison to the uncharged sample (curve 3) shows a low loss in total elongation of 8 % and a ductile fracture mode. This indicates a much lower HE sensitivity, even with the higher yield strength of the modified processed steel of 1160 MPa.
This description is highly simplified but published in more detail elsewhere [1].
References:
[1] B. Sun, W. Krieger, M. Rohwerder, D. Ponge, D. Raabe: Acta Mat 183 (2020) 313.
Author: D. Ponge (MA)