Smart Alloys
Dr. Loschen (L): What does “Adaptive structural Materials“ actually mean?
Dr. Tasan (T): Structural means that materials are used for generating structures, e.g. automotives, bridges, buildings etc. “Adaptive“ is the actual key word here: we aim at designing materials that are able to adapt to varying external conditions.
L: How do you achieve this adaptive behaviour?
T: We plan to introduce metastable phases into the material that transform when they experience e.g. stress.
Dr. Grabowski (G): Imagine a crack propagating in a material: when the crack tip, which exerts a lot of stress to its environment, reaches one of those metastable nanoparticles, the stress causes the metastable nanoparticle to transform to a stronger phase and thus stops the crack from expanding.
L: Why are there two scientists as a head of this group?
G: Cem, the experimentalist and me, the theoretician, will work complementarily. Metastable phases are experimentally difficult to analyse, but with DFT methods, these are methods based on quantum-mechanical principles, we can set the parameters to a point where the system is metastable and calculate the properties under the given conditions. Parameters such as temperature, stress or volume can be changed step by step until the phase transforms. Theory can predefine not only conditions but also compositions and thus reduce time and material needed for finding the optimum alloy. On the other hand, we need the experimentalists to validate our calculations.
L: But DFT methods are usually restricted to 0 Kelvin?
G: The department “Computational Materials Design“ has been developing various methodologies to include finite temperatures into the DFT description, thus enabling us to calculate systems up to their melting point with high accuracy and efficiency.
L: How are the materials produced in the end?
T: We closely collaborate with our metallurgy and processing group. This unique combination is only possible at the MPIE where you have all these facilities under one roof: Design (theoretical and experimental), production and analysis.
L: How does the interplay between theory and experiment work?
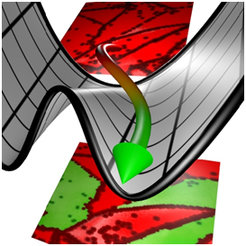
Logo of the group showing the intimate coupling between experiment and theory: The red fields show EBSD images of a material before and after phase transformation. The black/grey surface shows the energy dependence of a stable and unstable phase.
G: At first we discuss possible starting points and work in parallel. After a few results we discuss which direction to take, we reach our aim by small iterations.
L: What composition do you have in mind to start with?
T: The aim is of course an iron based alloy, but right now we are not restricting ourselves to any specific elements. Our first investigations are dedicated to a specific Ti-based alloy which is known as “gum metal“ because it reveals ideal plasticity. The mechanism is complicated but we try to understand it with in-situ microstructural analysis and simulation and then we transfer this knowledge to other, e.g. iron alloys.
L: What is the biggest challenge for each of you within the project?
G: Taking into account magnetic structures especially when it comes down to Fe-based alloys is a challenge, but our department has already been working on several approaches. Another challenge is finding the most accurate and efficient approach for simulating instable phases and calculating the chemical disorder, as typical DFT calculations are limited to only several 100 atoms. Advantageous in this respect is the expertise I have developed over the recent years in computing DFT based phase diagrams.
T: Analysing transformation processes is always a challenge. We have the advantage that we can employ many in-situ techniques here, but still the time resolution of the analytic instruments is not always sufficient. The second challenge is the spatial resolution: nanoparticles are difficult to analyse, but fortunately here at the MPIE we have strong tools available such as the atom probe tomography. In a nutshell, it is a risky project, but it seems that we have all the necessary tools at hand here to overcome these challenges.