Materials that can take the heat: Microstructural evolution in single crystal Ni-base superalloys
The demand for better efficiency and performance is the driving force for research on materials for turbine blades which have to operate at very high temperatures. Single crystal Ni-base superalloys (SXs) are at the moment the best material for this pur-pose. They have optimum balance of mechanical and chemical properties (creep, high temperature fatigue and oxidation resistance).
Turbine blades are the critical components of modern aviation and stationary gas turbines. They are cast in a Bridgman solidification process as [001]-orientated single crystals. The cast microstructure of Ni-based SXs is governed by the growth of dendrites and the subsequent solidification of interdendritic regions. Over ten alloying elements (Cr, Mo, W, Re, Ta, Ti, or Hf - enhance the high temperature capability; Al, Cr and Co - imprve oxidation resistance) are required to ensure the properties. Some of these segregate during solidification and therefore a homogenization heat treatment is required to achieve ho-mogeneous chemical composition throughout the alloy. The final microstructure consists of 60 – 80% volume fraction of γ’-cubes (ordered L12 phase, typical cube edge length of 0.5 μm) separated by thin γ-channels (face centered cubic microstructure, typical width: 50 nm).
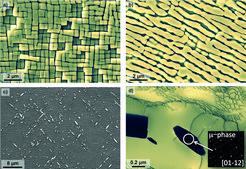
Evolution of the single crystal Ni-base superalloy during high temperature service: (a) SEM micrographs of the initial microstructure, γ’ cubes in the γ matrix; (b) rafted microstructure after creep (160 MPa at 1050 °C, 1% strain) and, (c) nucleated topologically close-packed (TCP) phases in the dendritic regions. (d) TEM micrograph showing a TCP particle and its cor-responding electron diffraction pattern.
Understanding of correlations between chemical composition, processing parameters, microstructure and thermodynamic stability is the key to proper design of efficient high temperature turbine blades. In the last 20 years the operating temperatures of Ni-base SXs could be increased by 100°C such that blades today operate close to 1100°C. This requires an increase of refractory elements, in particularly rhenium. Re improves creep strength but also promotes the formation of brittle and harmful topo-logically close-packed (TCP) phases. There has also been concern that the Re price increases significantly. Therefore, alloy development and modification represent an ongoing activity in superalloy technology. Other refractory elements like tungsten and ruthenium are considered as rhenium replacements. These questions are investigated in the new collaborative research center SFB/TR 103.
The Max-Planck Fellow Research Group on High Temperature Materials (HTM) links MPIE research activities to the interdisciplinary research in the SFB/TR 103, where single crystal super alloys are in the focus of interest. By the use of latest high-resolution characterization methods (high resolution, aberration corrected transmission electron microscopy and 3D atom probe tomography) correlations between the small and large-scale microstructural heterogeneities can be analyzed and understood. This is how activities of HTM help to develop new materials and processes that overcome limitations that currently hamper advances in high temperature single crystal technology.
Author: Aleksander Kostka