The MPIE’s next top model
How can we increase the safety of cars? This is a question which has been bothering scientists and car producers for several decades. The steels used in cars must be able to quickly absorb the shock energy of a crash. To do this, the material has to deform without breaking. The MPIE is developing a new model of TWIP steels (twinning induced plasticity). This kind of austenitic steel forms twins that lead to a prolonged characteristic hardening effect and an elongation at fracture of up to 60%. Moreover, TWIP steels are very light and thus help saving energy.
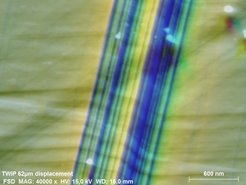
Nanotwins in Fe-22 wt-% Mn-0.6 wt-% C TWinning Induced Plasticity (TWIP) steel. Three separate forward scatter electron diodes produce individual RGB signals, allowing qualitative misorienta-tion to be seen by color differences in the image.
A new model makes TWIP steels applicable in the automotive industry
Former problems that occurred during deformation processes could be solved soon. David Steinmetz, a PhD student and materials scientist at the MPIE, is developing a model for the strain hardening behavior of TWIP steels: “the model I am working on is based on microstructural investigations of grain size and dislocation structures, including twins and dislocation cells. New investigations have revealed the importance of these microstructural features within the network of deformation structure.” Additionally, the model can accurately predict stress, strain and hardening behaviour over a temperature range of 400 Kelvin and it reveals that the high formability of TWIP steels is due to the interaction of twins and dislocations.
Desired properties are achieved by computational methods
The new model allows the understanding of the hardening behaviour of TWIP steels so that the automotive industry can save a lot of money and time. The simulation can teach us how to process sheets or to form crash-relevant parts of the car. The low stacking fault energy (SFE) of these high-manganese alloys, which is the key parameter for twinning, can nowadays be calculated by ab initio methods, performed in the department of Computational Materials Design headed by Prof. Jörg Neugebauer. In combination with the present model, this enables scientists of the MPIE to tailor the alloy composition and its SFE in order to achieve the desired macroscopic properties.