Smart as skin: intelligent corrosion protection
Research in corrosion protection has been increasing since the 18th century, especially with respect to steel. Galvanizing is a common protective means, but during the production process initial corrosive spots are formed right at the cut-edge. The idea that is developed at the MPIE is to incorporate microcapsules, which are filled with corrosion inhibitor, e.g. polyphosphomolybdate, into the zinc coating. As soon as the steel sheet is cut, the zinc starts to corrode and dissolve. This is the starting shot for the intelligent, second protective system: the capsules are released from the zinc onto the steel and smeared along the surface by the cutting device. The inhibitor can be released and thus protects the steel surface.
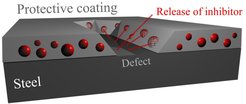
The microcapsules filled with corrosion inhibitor are released when the steel sheet is cut.
Modification with thiols facilitates the integration into the zinc
“This is an intelligent protective system that automatically realises when and where corrosion happens, becomes active and stops again when the respective spot is healed”, explains Dr. Rohwerder, group leader in the department of Interface Chemistry and Surface Engineering. It works like a scratch in the skin: it is detected, healed and the initial status is restored.
For preparing these smart coatings, three work steps must be performed: loading of the silica microcapsules with the inhibitor, sealing them to avoid premature leaching and finally incorporating the capsules into the zinc layer. The sealing procedure, however, has of course an immense influence on the release kinetics. By rinsing with water glass solution, the release is steady and slow. The in-corporation into the zinc layer is the most difficult part. Unmodified, the hydrophilic particles are repulsed by the zinc and only adsorb on the surface. Tabrisur Rahman Khan, a PhD student from Bangladesh, has now fixed the problem. He modifies the particles with zinc affine functional groups, such as thiols, which make the solvation feasible.
Max-Planck & Fraunhofer collaboration on intelligent corrosion coatings
Everything solved? Well, not completely. For efficient protection, a higher loading of the pores with the inhibitor must be realised. This is the focus of current research. Additionally, the concept of intelligent corrosion coatings has been expanded to systems with polymer coatings. The joint project ASKORR (Aktive Schichten für den Korrosionsschutz, active coatings for corrosion protection) is a successful collaboration between the Max-Planck and the Fraunhofer Society in this field. Two Max-Planck and two Fraunhofer Institutes are sharing their competences with respect to nanocomposite coatings, agent containers, zinc coatings and the analysis of effective mechanisms in order to improve the protective coatings. “It is a huge challenge, but present results look very promising”, states Rohwerder.
Author: Michael Rohwerder