Understanding hydrogen embrittlement by scale-bridging and experimental-informed simulations
Scale-bridging modelling of hydrogen embrittlement
Robert Spatschek and his group from the Computational Materials Design Department combine various computational and theoretical tools on the atomistic scale, which characterize the fundamental atomic properties. The information from these tools is carried over to larger scales, where the material failure becomes visible. The initiative is part of the DFG Collaborative Research Center 917 “Steel ab initio” as a joint programme of RWTH Aachen and MPIE Düsseldorf.
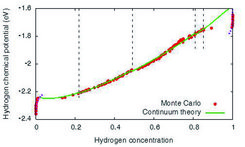
Hydrogen chemical potential in Ni at fixed volume. The red data points are calculated with molecular statics Monte Carlo simulations, the green curve segments are the pre-dictions from the continuum theory. Depending on the hydrogen concentration different hydride precipitate shapes are found.
Using high manganese steels as an example, interstitial hydrogen is preferentially located in manganese rich environments, which is mainly attributed to volumetric effects at the atomistic scale. This observation already indicates that mechanical effects play a central role for the understanding of hydrogen in metals. A focus of the present activities is on the formation of brittle hydrides, which favour crack propagation because of their low fracture toughness. The requirement to link bonding information between the different elements on the atomistic level up to the description of phase separation and crack formation on much larger scales requires the development of a consistent and seamless chain of modelling tools. This tool-chain involves, apart from ab initio methods, also atomistic approaches like Monte Carlo techniques, both of which methods are limited to a restricted number of atoms. Both methods cannot account for long-range elastic effects. Therefore, the de-velopment of quantitative continuum methods is central for a successful scale bridging. Here, we have developed a description which uses the atomistic information in micrometre-scaled phase field models, which allow to efficiently describe hydride formation in mesoscopic systems under different mechanical loading conditions while maintaining the accu-racy of the Monte Carlo simulations. Together with Steffen Brinckmann from the department structure and Nano-/ Micromechanics of Materials (SN), Spatschek‘s group has verified the mechanical response by finite element simulations.
The sample geometry is of central importance. However, commonly the thermodynamics of phase separation is considered for bulk systems. Recently Spatschek found out that the behaviour of hydride formation strongly differs near surfaces and interfaces due to mechanical stress relaxation. Near free surfaces – like cracks – hydride formation occurs at significantly lower hydrogen concentrations than in the bulk. This observation implies that materials, which are usually not considered to be hydride formers under the given environmental conditions, can form these brittle phases near free surfaces.
Experimentally-informed fracture simulations
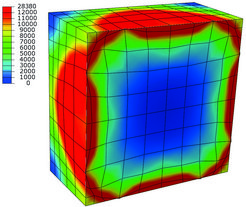
Stress distribution in MPa during hydride growth in anisotropic Ni. The hydride has an eigenstrain that results in the deformed grid highlighting the growth of the spherical inclusion in the restricted, i.e. periodic, space.
Brinckmann calculated the stress induced by hydride formation in the anisotropic metal. Conventionally, isotropic descriptions are used, which assume that the material behaves in each direction identically. However, the atomistic cubic structure found in metals results in strong variations in different directions, which is termed anisotropic behaviour. The volumetric expansion is a key in understanding hydride formation: the hydride is larger than the originating metal.
Initially in hydride growth, the hydrides are small and well separated, i.e. their stress fields do not interact. However, during growth the hydrides account for increasing amounts of material and these hydrides interact elastically.
Finally, as the space separating the hydrides becomes increasingly smaller, the volumetric expansion and the induced stresses dominate the coalescence of three dimensional hydride islands. In collaboration with Christoph Kirchlechner, also from the SN department, the material properties in hydrogen environments are determined by micromechanical experiments. Kirchlechner heads the group Nano-/ Micromechanics of Materials and focuses on fracture and plasticity experiments on small length-scales. In these experiments, a focused ion beam is used to carve geometries out of the bulk metal. Then these specimens are deformed with a nanoindenter, which measu-res forces and displacements, from which the material properties can be obtained. Conventionally, these experiments are executed in air or vacuum conditions. In this project, the micromechanical experiments are performed in electrolytes. Upon charging the sample, hydrogen from the electrolyte will diffuse into the metal and determine the material fracture toughness and plasticity. The material properties are then used in finite element simulations on the micrometre length-scale. These simulations take the geometry specific stresses as well as the hydrogen diffusion into account. Stresses and diffusion interact: the stresses drive the hydrogen diffusion and the hydrogen concentration results in volumetric expansion, hence additional stresses.
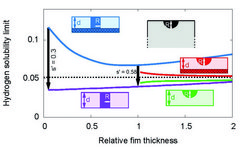
Hydrogen solubility limit in thin films of Nb at room temperature. The predictions stem from scale bridging simulations. For films which are attached to a rigid substrate, the solubility limit is increased in comparison to bulk samples. Detachment of a thin film leads to a drop of the solubility limit by about a factor 1/3, in agreement with experiments.
Authors: Steffen Brinckmann, Robert Spatschek